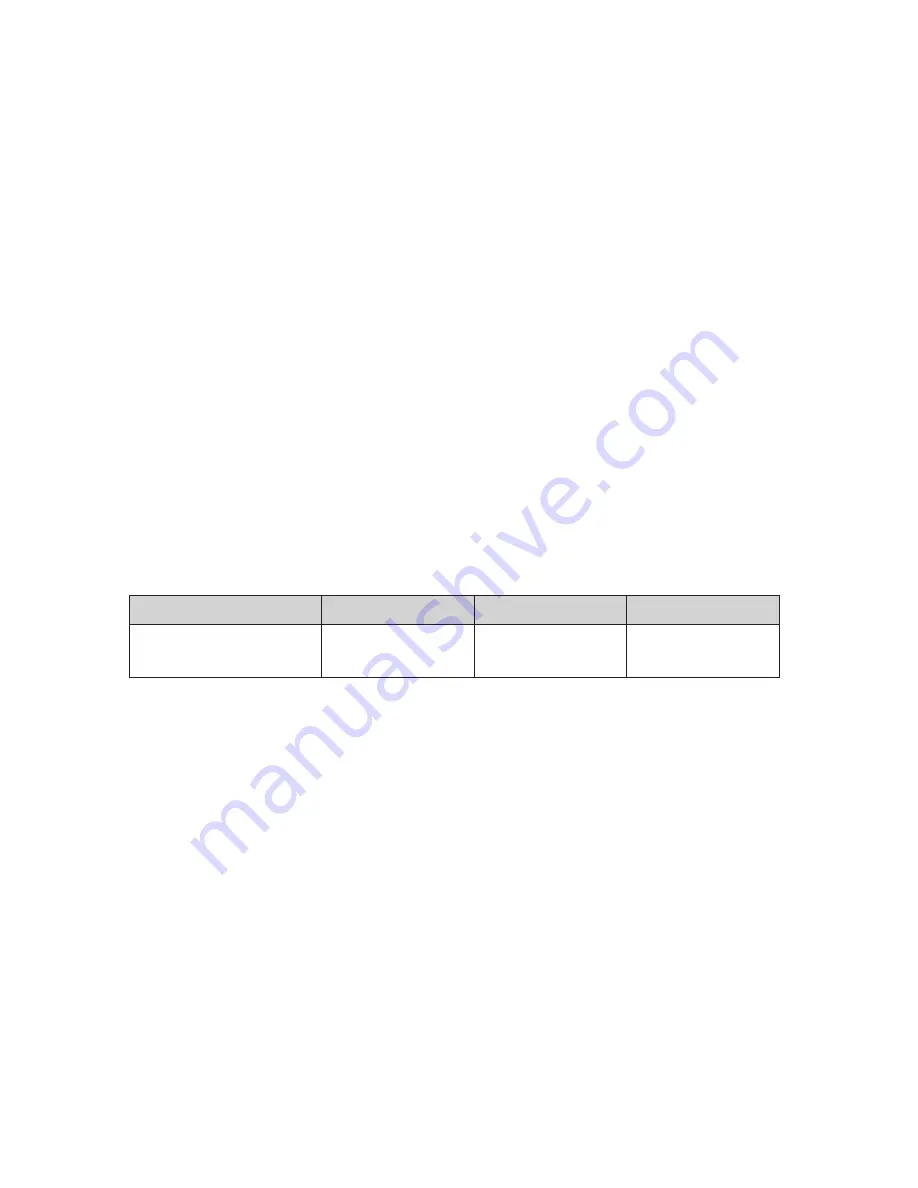
9
7. OPERATION
Only operate the NX cooler within the temperature and pressure limits shown on the
assembly drawing
When installing, ensure that the seal cooler, piping, and vent locations provide com-
plete venting of gas/air from both the coil and case systems. This requires the vents
to be located at the highest point in each system.
Before start-up, ensure that all piping is properly attached to the appropriate connec-
tions for both the coil and case systems to prevent fluid leaks and achieve expected
cooler efficiencies.
Before start-up, ensure that all the gas/air is vented from both the coil and shell sys-
tems to provide the system efficiencies expected and prevent a vapor lock condition.
At start-up, ensure that the flush fluid flow and coolant fluid flow are set and stabilized
at the prescribed flow rates determined for the application.
Do not allow the case system coolant fluid flow rate to be operated below minimum
flow rates. Lower flow rates will encourage fouling which reduces the seal cooler heat
transfer capabilities. See table below for minimum required case side flow rate
Cooler size
.500
.625
.750
Minimum Coolant Flow
2.5 GPM
[9.5 LPM]
3 GPM
[11.4 LPM]
6.5 GPM
[24.6 LPM]
Table 1: Minimum Case Side Flow Rate.
Seal cooler performance should be monitored periodically. Baseline temperatures
should be gathered soon after equipment commissioning. Target case side base line
temperature differential should be 11°C (20°F) or lower. Exceeding this differential
temperature could result in a reduction of heat transfer and shell side fouling.
Note:
For pressure and temperature limits, see the drawing included with the NX seal
cooler.
Periodically, shell and tube side temperature differential should be monitored. With no
change in process temperature and flow rate, coil side outlet temperature should not
exceed 5.5 - 11°C (10-20°F) rise from base line. With no change in cooling fluid tem-
perature and flow rate, case side differential temperature should not vary significantly
from base line reading. A variation of 5.5 - 11°C (10-20°F) from base line indicates
loss of heat transfer. Case side fouling could be a cause and cooler cleaning should
be considered.