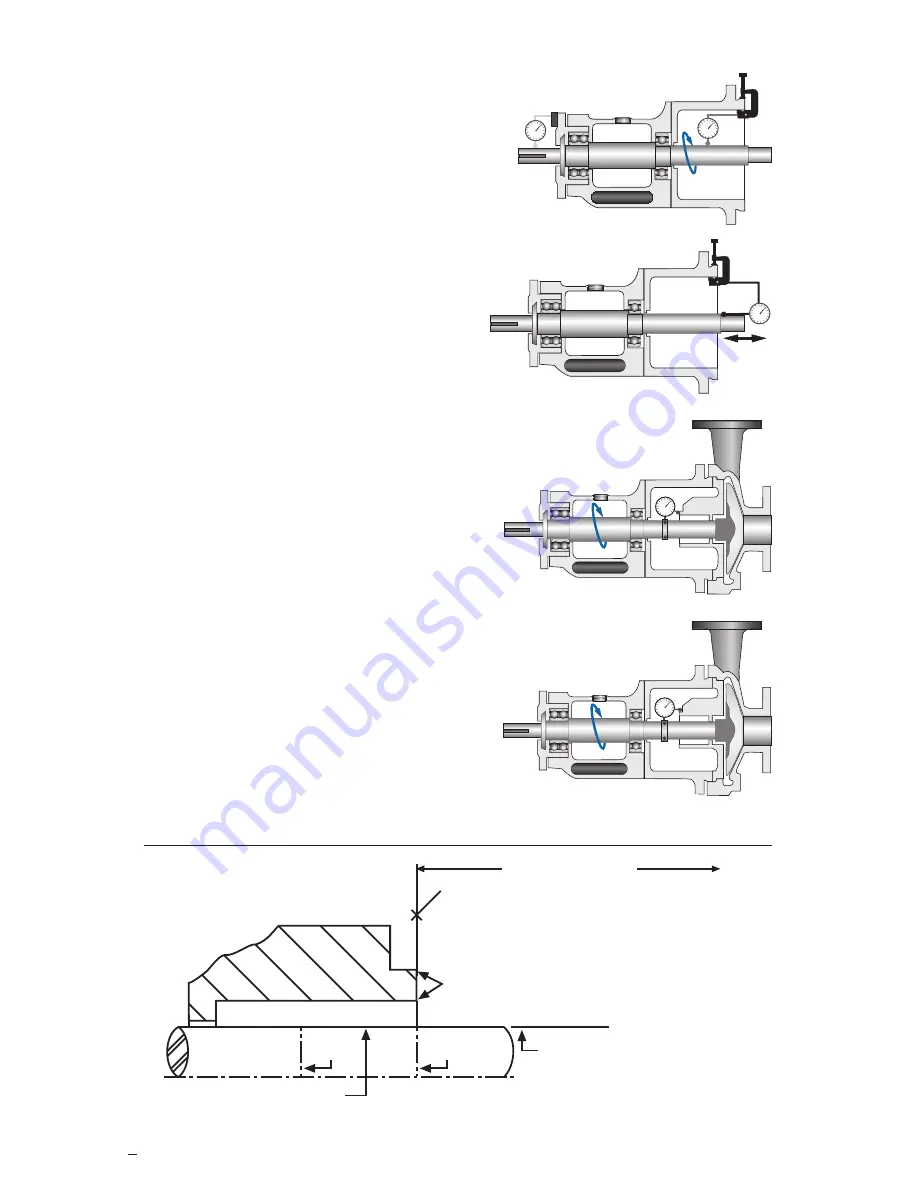
2
Shaft runout
should be checked against the equipment manufacturer‘s specifications.
Generally, should not exceed 0.05 mm (0.002 inch) TIR (Total Indicator Reading)
at any point along the shaft for ball or roller type bearings.
For sleeve type bearings, refer to manufacturer instructions.
If the equipment is not completely dismantled, verify runout
near seal location.
The above values apply to shaft speeds in the range from
1000 to 3600 RPM. For values above and below, consult your
Flowserve representative. See Figure 1.
Shaft endplay
should not exceed 0.25 mm (0.010 inch) TIR,
regardless of thrust bearing type. See Figure 2.
Radial bearing play
at seal chamber face should be checked
against the equipment manufacturer’s specifications. Generally
0.05 - 0.10 mm (0.002 - 0.004 inch) will be applicable for ball or
roller type bearings. For sleeve or journal type bearings, values
will generally be in the order of 0.10 - 0.15 mm (0.004 - 0.006 inch).
If equipment is found outside the general range, contact the
equipment manufacturer and your Flowserve representative
to verify the equipment’s suitability for the seal.
Seal chamber squareness
to the shaft centerline should
be within 0.0005 mm/mm (0.0005 inch/inch) of seal
chamber bore TIR.
Note:
make sure that shaft endplay does not affect
the reading. Verify the smoothness of the seal
chamber face for a good gasket joint. See Figure 3.
Concentricity of the shaft
to the seal chamber bore or gland
pilot register should be within 0.025 mm per 25 mm shaft
diameter (0.001 inch per 1 inch shaft diameter)
to a maximum of 0.125 mm (0.005 inch) TIR.
See Figure 4.
Figure 4
Figure 3
Figure 1
Figure 2
Surface finish requirements
Figure 5
To first obstruction
Seal housing face to have a surface finish
of 1.6 μm (63 μinch) R
a
finish or better
Scribe
Mark A
Shaft or sleeve OD
+0.000 mm (+0.000 inch)
-0.050 mm (-0.002 inch)
+0.000 mm (+0.000 inch) API 610/682
-0.025 mm (-0.001 inch) DIN/ISO
Scribe
Mark B
Seal housing bore to have 3.2 μm
(125 μinch) R
a
finish or better
ANSI
Sleeve or shaft finish to be
0.8 μm (32 μinch) R
a
or better.
Gland pilot can be at either
of these register locations.