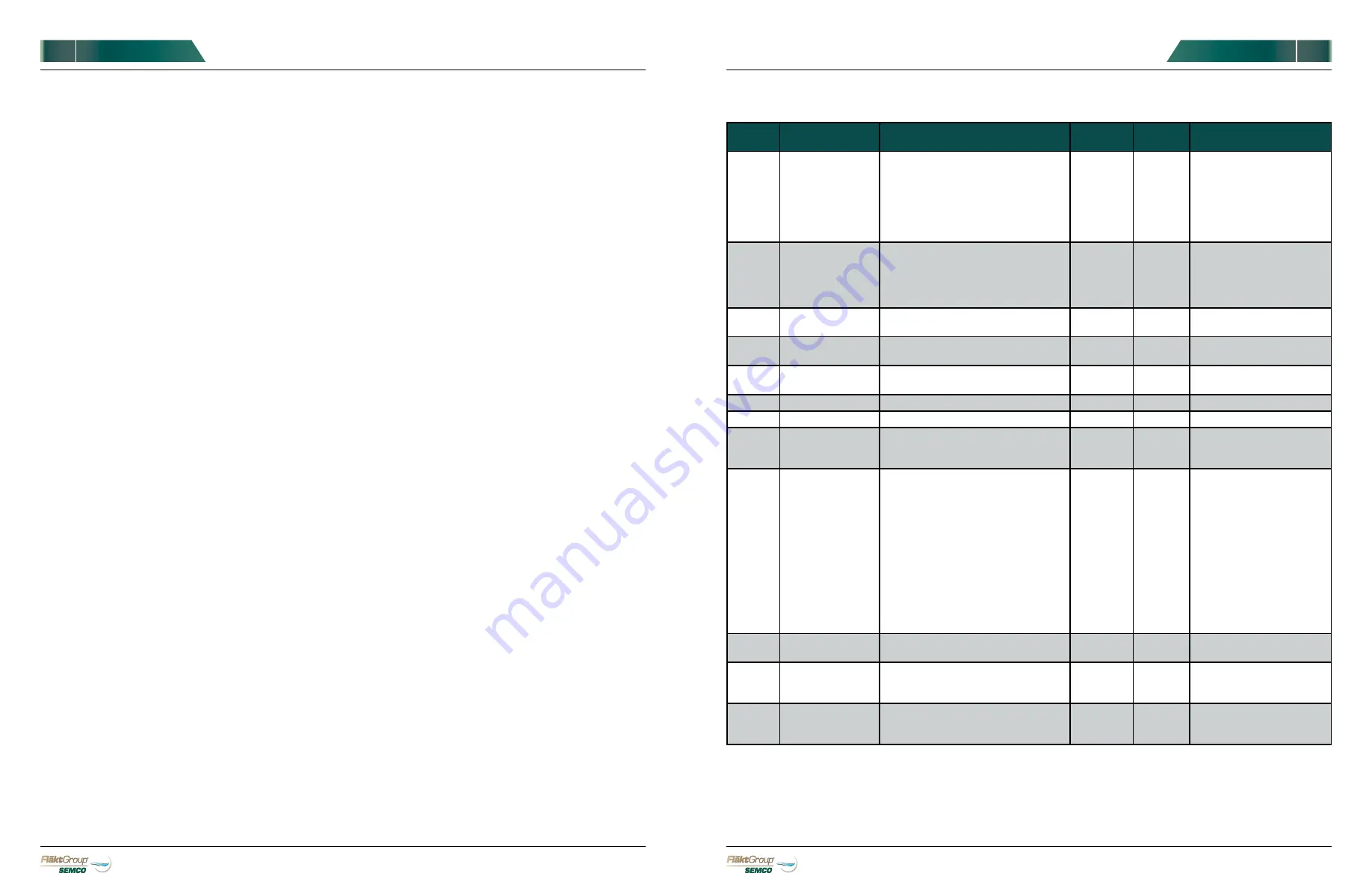
17
16
SPECIALIZED
HEALTHY
AIR SOLUTIONS
SPECIALIZED
HEALTHY
AIR SOLUTIONS
OWNER’S MANUAL
OWNER’S MANUAL
ASCENDANT
™
ASCENDANT
™
SPECIALIZED
HEALTHY
AIR SOLUTIONS
OWNER’S MANUAL
PARAM.
TITLE
FUNCTION
OPTIONS
DEFAULT
SETTING
SEMCO
SETTING
COMMENTS
B1-01
Frequency
Reference
Selection 1
0: Operator - Digital preset speed d1-
01 to d1-17.
1: Terminals - Analog input terminal A1
or A2.
2: MEMOBUS communications
3: Option PCB
4: Pulse Input (Terminal RP)
1
1
Selects the frequency
reference input source.
B1-02
Run Command
Selection 1
0: Operator - RUN and STOP keys on
the digital operator.
1: Digital input terminals
2: MEMOBUS communications
3: Option PCB
1
1
Selects the run command
input source.
B1-04
Reverse Operation
Selection
0: Reverse enabled.
1: Reverse disabled.
0
1
Permits or prohibits reverse
operation.
B1-07
Local / Remote
Run
0: Run command must be cycled
1: Continue running
0
1
Drives run if run command
is active in new controller
B1-17
Run Command at
Power Up
0: Run command must be cycled
1: Run command issued
0
1
Drive runs if run command
is active at power up
C1-01
Acceleration Time
0.0 to 6000.0
10
60
Acceleration time
C1-02
Deceleration Time
0.0 to 6000.0
10
60
Deceleration time
C4-01
Torque
Compensation Gain
0.00 to 2.50
1
0
Compensates for added
load by increasing output
voltage.
C6-02
Carrier Frequency
Selection
1 : 2.0 kHz
2 : 5.0 kHz
3 : 8.0 kHz
4 : 10.0 kHz
5 : 12.5 kHz
6 : 15.0 kHz
7 : Swing PWM1 (Audible sound 1)
8 : Swing PWM2 (Audible sound 2)
9 : Swing PWM3 (Audible sound 3)
A : Swing PWM4 (Audible sound 4)
B to E: No setting possible
F : User defined (determined by C6-03
through C6-05)
3
1
Lower carrier frequencies
increase torque and audible
noise.
E1-03
V/f Pattern
Selection
0 to FF
F
F
Allows custom voltage
frequency curve.
E2-01
Motor Rated
Current
10 to 200% of drive rated current
kVA
dependent
0.57
(208-230)
0.29 (460)
E2-03
Motor No-Load
Current
0 to [E2-01]
kVA
dependent
0.23
(208-230)
.11 (460)
Nameplate amps * 40%
Consult SEMCO
PROGRAMMING PARAMETERS
*FläktGroup SEMCO does not recommend use with motors other than those provided with the unit. Consult Yaskawa for assistance
in programming for use with other motors.
SPECIALIZED
HEALTHY
AIR SOLUTIONS
OWNER’S MANUAL
UNIT CONTROLS
PROGRAMMING PARAMETERS
PROGRAMMING THE WHEEL MOTOR VFD:
NOTE:
For most V1000 parameters, the drive must be in a
STOP
condition while programming.
1)
Press
ESC
key until left-most part of drive’s display
shows
F
.
DRV
LED will also be lit.
2)
Press
DOWN
arrow twice to display
PAr
then press
ENTER
key. (Parameters are now accessible)
3)
Using
UP/DOWN/RIGHT ARROWS
, select
parameters to be read and/or changed starting
with A1-01.
4)
If required, use
RIGHT ARROW
or
ENTER
key to
scroll to right-most digits of parameter name.
Digits will flash.
5)
Press
ENTER
key to read value.
6)
Using
UP/DOWN/RIGHT ARROWS
, set desired
value then press
ENTER
key to store value. Drive
will accept value,
if valid, then re-display parameter number (i.e. B1-
01, C1-02, etc.)).
7)
Repeat
STEPS 3 - 6
to program remaining
parameters per application requirements.
8)
When complete, press
ESC
key until left-most part
of drive’s display shows
F
.
DRV
LED will also be lit.
V1000 DRIVE IS NOW READY TO RUN.
SEQUENCE OF OPERATION
Refer to the Unit Submittal for a detailed sequence of
operation, performance, and wiring schematic.
The typical sequence of operation is that upon a call
for dehumidification, the pre-cooling coil is active and
cools the process air to the temperature shown in the
submittal. The dehumidification wheel bypass damper
modulates partially closed to produce the correct
proportion of process air through the wheel and bypass.
The regeneration heat source modulates to maintain the
humidity setpoint. The process and regen fans modulate
to maintain their supply CFM setpoints.