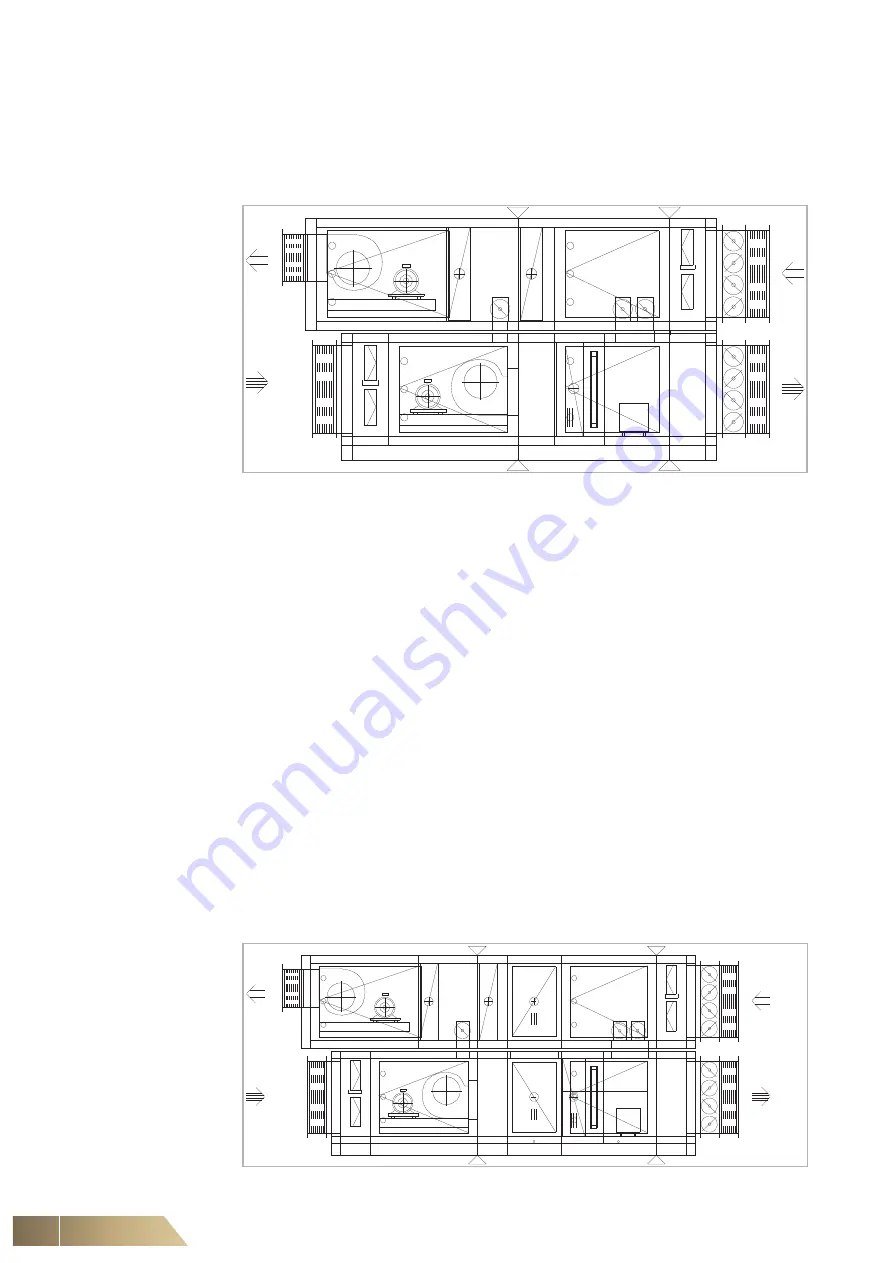
Technical Description
CAIR
fricostar
®
12
FläktGroup DC-2009-0019-GB 2018-01/R9 • Specifications are subject to alteration without notice
3.2.2 CMU units
The FläktGroup CAIR
fricostar
CMU is designed for private and small public swimming
pools. The series is available in 6 sizes. The unit's function is to dehumidify and heat
air in swimming pools in mixed air mode. The unit is delivered with a DDC controls
which regulates all functions of the system on a fully automated basis.
Fig. 3-2:
FläktGroup CAIRfricostar CMU
When in stand-by mode without dehumidification the air is recirculated in the swimming
pool. When the humidity setpoint has been exceeded the unit switches into dehumidi-
fication mode. At this point the supply-air fan is operated at nominal air flow and the
extract-air fan maintains the proper air movement. The refrigeration unit is activated in
order to start dehumidification. Using the bypass damper a certain part of return air is
mixed without further treatment with dehumidified air that has passed through the
refrigeration cycle. The dehumidification stage continues until the actual humidity value
lies below that of the humidity setpoint. Then the refrigeration unit is deactivated.
When in active hours swimming pool mode the fresh and exhaust air dampers are
opened, the bypass damper is closed. To start dehumidification the refrigeration unit is
activated.
Using an optional pool water condenser a certain amount of excess energy produced
by the refrigeration cycle can be fed back into swimming pool water.
3.2.3 CAM units
The FläktGroup CAIR
fricostar
CAM is designed for various kinds of private and public
swimming pools. This unit series can deliver air flow rate from 750 up to 45.000 m³/h.
The unit's function is to dehumidify and heat air in swimming pools in mixed air mode.
Besides a refrigeration unit (heat pump) this unit type is additionally equipped with an
efficient heat recovery system. The unit is delivered with a DDC controls which regu-
lates all functions of the system on a fully automated basis.
Fig. 3-3:
FläktGroup CAIRfricostar CAM
Содержание CAIRfricostar
Страница 1: ...CAIRfricostar OPERATION MANUAL ...