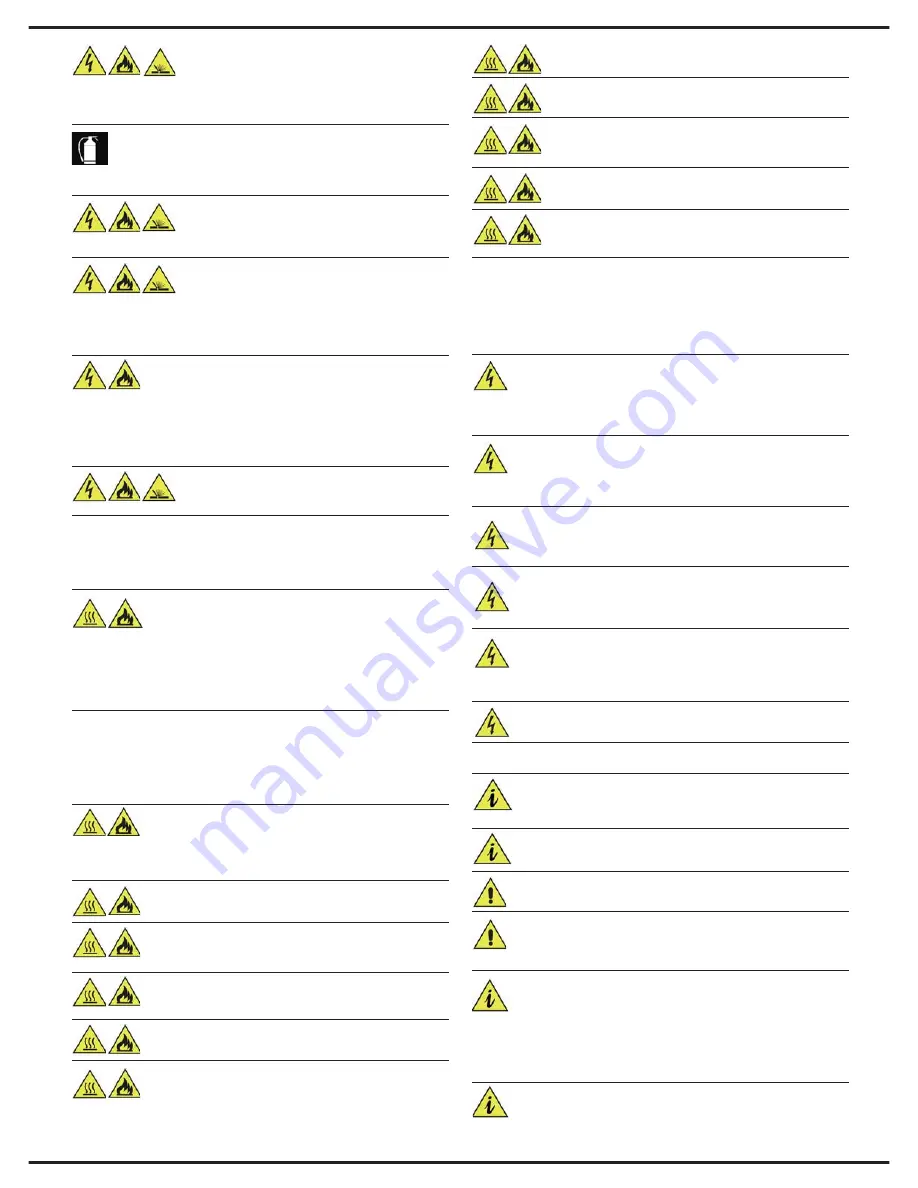
4
CLEAN ENVIRONMENT
Remove all flammable materials away from
the work environment.
SERIOUS DANGER ! 1
NEVER weld in confined spaces (e.g. in a con-
tainer vehicle, a cistern or a storeroom etc.) where toxic, inflamma-
ble or explosive materials are, or have been, located or stored.
Cisterns, in particular, may still contain toxic, flammable or explosi-
ve gases and vapours years after they have been emptied.
SERIOUS DANGER! 3
NEVER use the Welder to melt frozen water
pipes.
SERIOUS DANGER ! 2
NEVER weld a cistern that contains (or has stored)
toxic, inflammable or explosive materials. They could
still contain toxic, flammable or explosive gases and vapours years
after they have been emptied. If you are obliged to weld a cistern,
ALWAYS passivate it by filling it with sand or a similar inert sub-
stance before starting any work.
WELDING ENVIRONMENT VENTILATION
Ventilate the welding environment carefully. Maintain
sufficient air-flow to avoid toxic or explosive gas accumulation.
Welding processes on certain kinds or combinations of metals can
generate toxic fumes. In the event of this happening, use air-sup-
ply respirators. BEFORE welding, read and understand the wel-
ding alloy safety provisions.
GAS TYPES
These welders use only inert (non-flammable) gases for welding
arc protection. It is important that the appropriate type of gas is
chosen for the type of welding being performed.
UNIDENTIFIED GAS CYLINDERS
NEVER use unidentified gas cylinders.
PRESSURE REGULATOR 1
NEVER connect the cylinder directly to the Welder.
Always use a pressure regulator.
PRESSURE REGULATOR 2
Check the regulator is performing its function properly.
Read the regulator instructions carefully.
PRESSURE REGULATOR 3
Never lubricate any part of the regulator.
PRESSURE REGULATOR 4
All regulators are designed for a specific type of gas.
Check the regulator is appropriate for the protective
gas to be used.
VENTILATION
VENTILATION
Together with the previous instructions, the following pre-
cautions should be strictly observed
PROTECTIVE WELDING GASES
PROTECTIVE WELDING GASES
Together with the previous instructions, the following
precautions should be strictly observed when welding
with protective gases
WALL AND FLOOR PROTECTION
The walls and flooring surrounding the welding
environment must be shielded using non-flammable materials. This
not only reduces the risk of fire but also avoids damage to the wal-
ls and floors during welding processes.
EXTINGUISHER
Place an approved and appropriately-sized fire extinguisher in
the work environment.
Check its working order regularly (carry out scheduled inspections)
and ensure that all parties involved know how to use one.
DAMAGED GAS CYLINDERS
NEVER use damaged or faulty cylinders.
CYLINDER RELOCATION
NEVER lift a gas cylinder by holding the regulator.
GAS CYLINDERS
Do not expose gas cylinders to excessive heat sour-
ces, sparks, hot slag or flames.
GAS HOSE 1
Check the gas hose is not damaged.
GAS HOSE 2
Always keep the gas hose well away from the work
area.
ELECTRIC SHOCK
Together with the previous instructions, the following pre-
cautions should be strictly observed to reduce the risk of
electric shock
ELECTRIC SHOCK INJURY
DO NOT touch a person suffering from electric shock if
he/she is still in contact with the cables. Switch the mains power
source off immediately THEN provide assistance.
CABLE CONTACT
Do not tamper with power cables if the mains power is still
switched on. Do not touch the welding circuitry. Welding cir-
cuitry is usually low voltage, however, as a precaution, do not tou-
ch the welder electrodes.
CABLE AND PLUG PRECAUTIONS
Check the power supply cable, plug and wall-socket regularly.
This is particularly important if the equipment is relocated often.
REPAIRS
Never attempt to repair the Welder yourself. The result would
not only cause warranty cancellation but also high danger risks.
MAINTENANCE PRECAUTIONS
Always check that the electric power supply has been discon-
nected before performing any of the maintenance opera-
tions listed in this manual ( e.g. before replacing any of the fol-
lowing: worn electrodes, welding wires, the wire feeder etc.)
Never point the welding gun or the electrode towards yourself
or others.
Check no power supply cables, telephone cables or other
electrical items (e.g. computer cables, control lines etc.) are
in the vicinity of the Welder.
Check there are no telephones, televisions, computers or other
transmission devices close to the Welder.
ELECTROMAGNETIC COMPATIBILITY
Make sure that people with pace-makers are not in the imme-
diate vicinity of the Welder.
Do not use the Welder in hospitals or medical environments
(including veterinary surgeries). Make especially sure there
is no electrical medical equipment being used close to whe-
re welding is being done.
Should the Welder interfere with other apparatus, take the fol-
lowing precautionary measures:
1.
Check the Welder’s side panels are securely fastened.
2.
Shorten the power supply cables.
Place EMC filters between the Welder and the power source. (Con-
tact Fimer Technical Dept. in this respect )
EMC compatibility : CISPR 11, Group 1, Class A.
2
Содержание TM 215
Страница 1: ...Instructionsmanual TM215 ...
Страница 3: ......
Страница 4: ...1 6 5 A 2 2 2 5 V 1 4 0 A 2 5 6 V 1 2 0 A 2 4 9 V 3 1 1 V 1 7 2 V 2 0 5 V 1 3 0 A ...
Страница 6: ......
Страница 11: ......
Страница 12: ......
Страница 13: ......
Страница 14: ......
Страница 15: ......
Страница 16: ......
Страница 19: ......
Страница 24: ... NOTE ...
Страница 25: ... NOTE ...
Страница 26: ... NOTE ...
Страница 28: ......