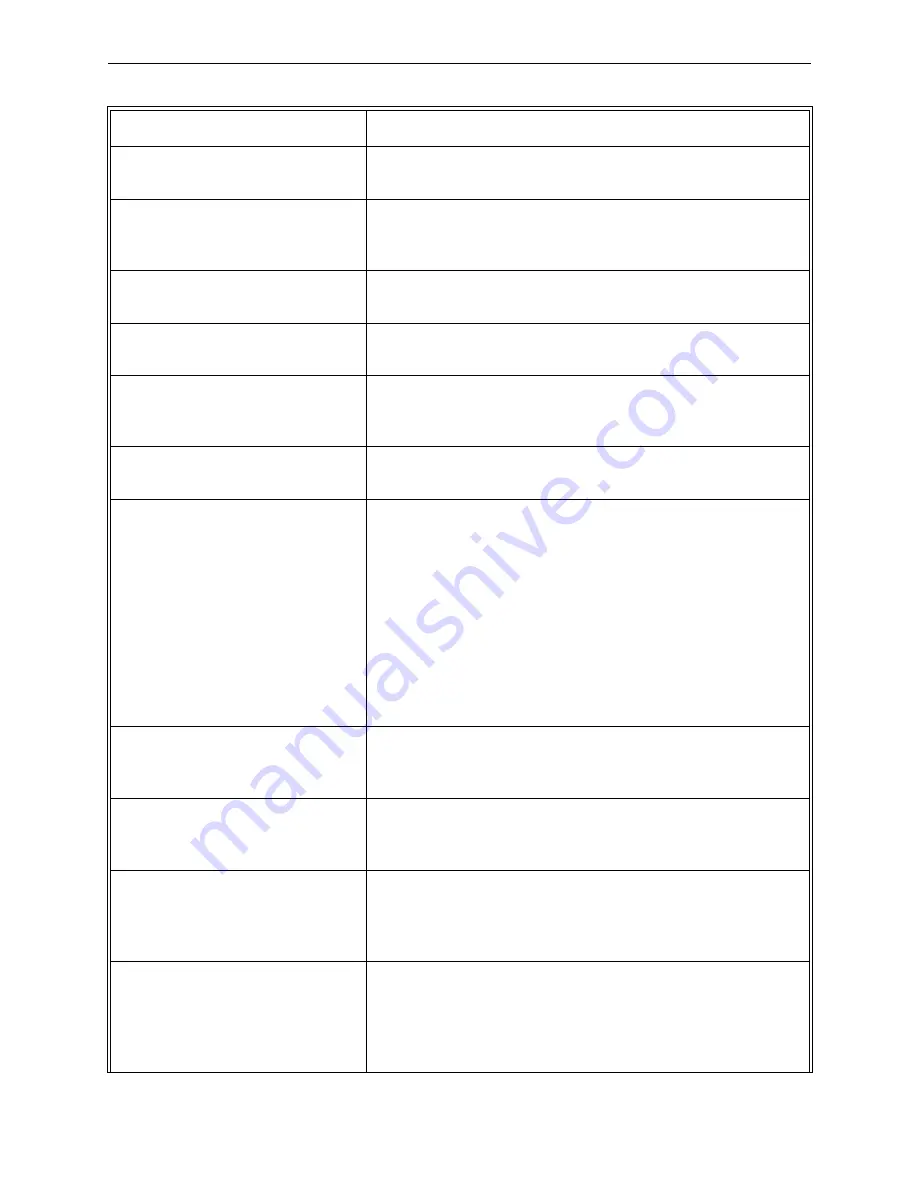
OV-II Maintenance, Troubleshooting and Service Manual
1-2
Industrial Dynamics Company, Ltd. ©
Form 42600 (10/03)
Purge Air (Suction Pipes)
Check for air flow by holding hand in front of suction cups as
starwheel rotates past purge ports.
Upstream Bottle Washer
Check and adjust for proper spray pattern and coverage. If not set
properly, causes "false rejects" due to conveyor soap on bottle
bottom.
Air Blow-off, Diffuser Glass
Check for proper flow. Removes water, pulp and other objects
from glass surface prior to inspection.
Air Blow-off, Bottle Bottom
Check for proper flow and pattern. If not set properly causes
"false rejects" due to conveyor soap on bottle bottom.
Microsonic Bottle Sensors
Check line control operation by blocking and unblocking beams
with bottle. Receiver's red indicator should be ON when there is
no bottle and OFF when bottle is present.
Bottle Guide Belts
Check for proper position and tightness. Change if too loose.
Check brackets for alignment.
Inspection Head Height
Check the Inspection Head height (counts) listed on the
BOTTLE CHANGEOVER REQUIREMENTS
screen. Check
Inspection Head height above starwheel using mechanical
counter. Also verify 13 mm (0.5 inch) clearance between bottom
of Finish Inspection lens and bottle crown. Be sure to “lock” the
raising mechanism after each adjustment. Verify inspection
height by running bottles.
Repeat this procedure for each bottle type.
Make sure the bottle neck guide belt is pulled away and clear
from the starwheel top plate when raising or lowering the
Inspection Head.
Infeed and Outfeed Bottle Guides
Check for proper guides. Check all knobs and if necessary
tighten. Guide should blend smoothly with production conveyor
guide rails.
OSW Inspection Area
Check the inspection area for any debris such as broken glass,
labels, or other foreign debris. Clear may debris out of the
inspection area.
OSW Guide Rails
Check for proper cord tension; tighten if necessary. Check for
labels, glass, debris, etc., stuck to the guide rails and remove as
necessary. Inspect for any damage to the guide rails and wear-
strips.
OSW Diffuser Panels (on the light
source enclosure)
Check for scratches or other damage. Clean with a
NONCAUSTIC
,
NONABRASIVE
commercially available
glass cleaner (such as Windex
).
Replace phenolic diffuser
panels at 6 month intervals to ensure consistent light levels for
inspection
.
ITEM
DAILY MAINTENANCE