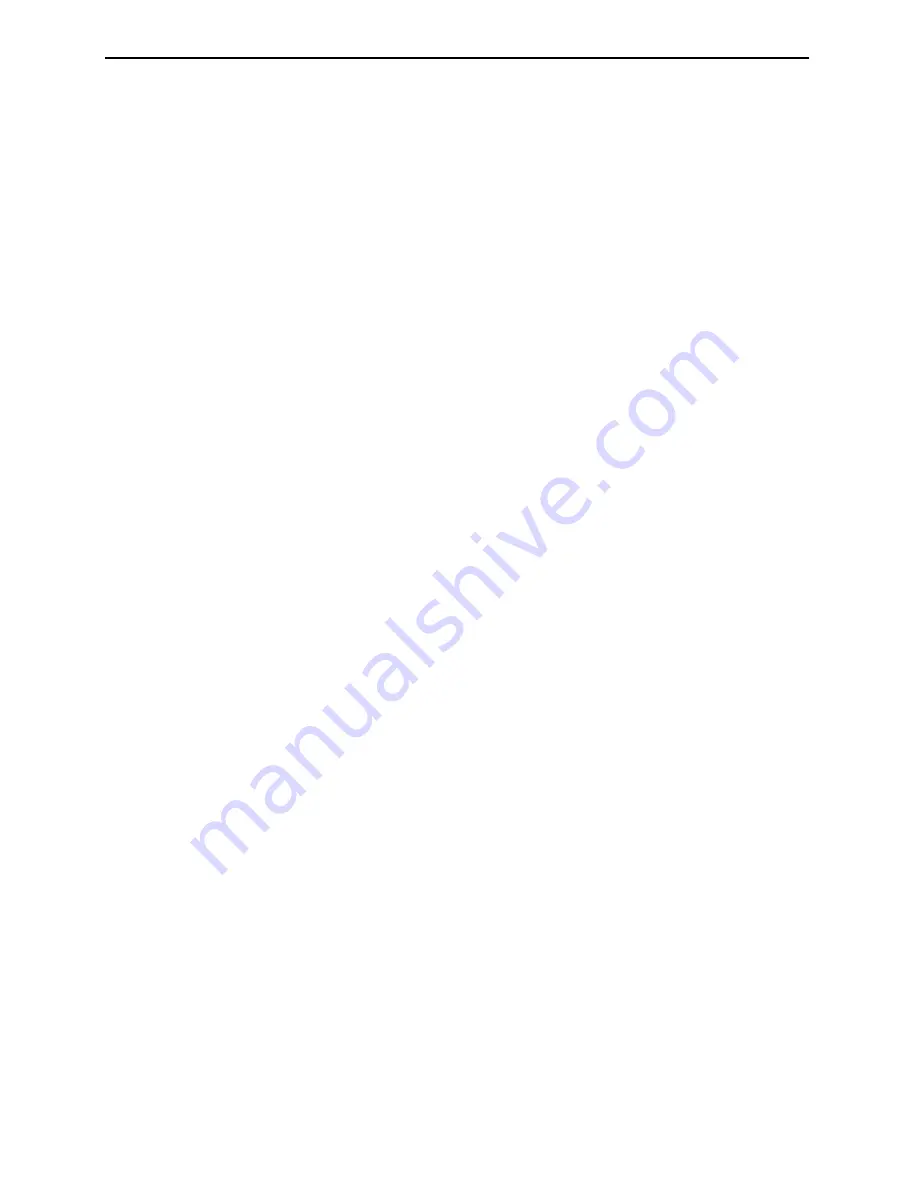
FT-70/75 Fill Level Inspectors Operator’s Guide
4-10
Error Number 58
An abnormally large container was detected. The reject delay
encoder count exceeded the current encoder count. This condition
is generally caused by line jams. If this error occurs continuously,
the rejector may be installed to near the trigger. Report this error to
your Service Department.
Error Number 61
The reject delay position at the rejection queue output exceeded
the current encoder count. If this error occurs repeatedly, call IDC
technical support.
Error Numbers 64
These error pertains to label inspection. Report this error to your
Service Department.
Error Number 66
A fill level reject was detected while the Fill Level Status was
turned off. Turn the Fill Level Status on to correct this condition.
Error Number 67
The number of containers in the Consecutive Diameter Missing
Cap Reject Alarm was exceeded. This is a high priority error
condition and will cause the Warning Beacon to flash if Beacon
Status is set to HIGH PRIORITY ONLY. If this error persists, report
this error to your Service Department.
Error Number 68
No encoder pulses were received for the Diameter Missing Cap
Width function. This error condition is low priority and will not
cause the Warning Beacon to flash during HIGH PRIORITY ONLY
operation. If this error persists, report this error to your Service
Department.
Error Number 72
This error condition indicates the Line Speed is to high. The
encoder may need to be calibrated or the X-ray Sample cutoff limit
may be set too high. This error can also be caused by noise on the
encoder cable which connects to TB4-2. If this error persists, report
this error to your Service Department.
Industrial Dynamics Company, Ltd. Document 40274-0600
Содержание ft-70
Страница 1: ...FT 70 and FT 75 Operation Guide 40274 0600...
Страница 2: ...FT 70 and FT 75 Operation Guide Document 40274 0600 Fill Level Inspectors...
Страница 13: ...FT 70 75 Fill Level Inspectors Operator s Guide XII Industrial Dynamics Company Ltd Document 40274 0600...
Страница 15: ...FT 70 75 Fill Level Inspectors Operator s Guide 1 2 Industrial Dynamics Company Ltd Document 40274 0600...
Страница 21: ...FT 70 75 Fill Level Inspectors Operator s Guide 1 8 Industrial Dynamics Company Ltd Document 40274 0600...
Страница 23: ...FT 70 75 Fill Level Inspectors Operator s Guide 2 2 Industrial Dynamics Company Ltd Document 40274 0600...
Страница 45: ...FT 70 75 Fill Level Inspectors Operator s Guide 2 24 Industrial Dynamics Company Ltd Document 40274 0600...
Страница 47: ...FT 70 75 Fill Level Inspectors Operator s Guide 3 2 Industrial Dynamics Company Ltd Document 40274 0600...
Страница 61: ...FT 70 75 Fill Level Inspectors Operator s Guide 3 16 Industrial Dynamics Company Ltd Document 40274 0600...
Страница 79: ...FT 70 75 Fill Level Inspectors Operator s Guide 5 2 Industrial Dynamics Company Ltd Document 40274 0600...
Страница 85: ...FT 70 75 Fill Level Inspectors Operator s Guide 5 8 Industrial Dynamics Company Ltd Document 40274 0600...