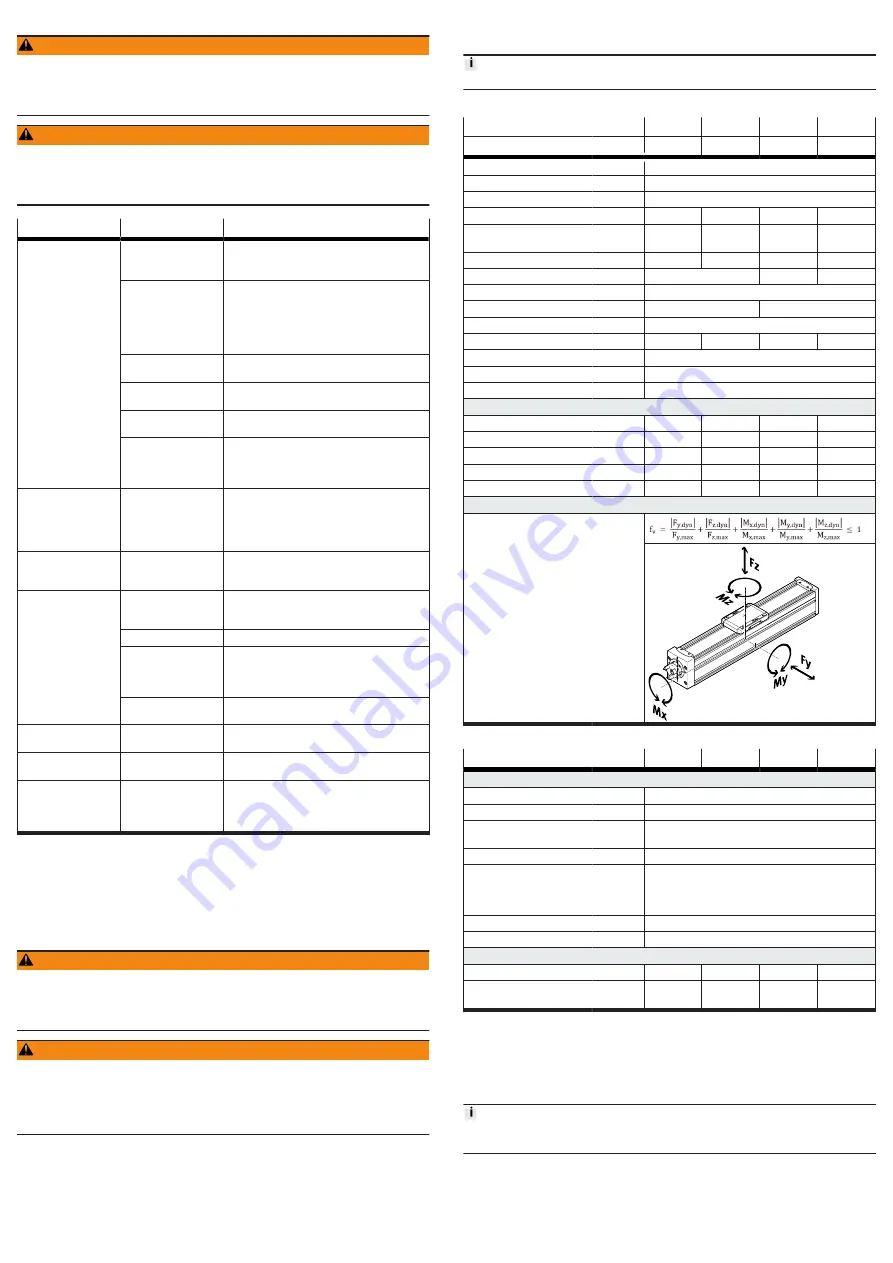
10.1
Fault clearance
WARNING
Unexpected movement of components.
Injury due to impacts or crushing.
• Before working on the product, switch off the control and secure it to prevent it
from being switched back on accidentally.
WARNING
Risk of injury due to unexpected movement of components.
• Protect the positioning range from unwanted intervention.
• Keep foreign objects out of the positioning range.
• Perform commissioning with low dynamic response.
Malfunction
Possible cause
Remedy
Loud running noises,
vibrations or rough
running of the axis.
Coupling distance too
short.
Observe permissible coupling spacings
è
Instruction manual for motor mounting kit,
Torsional stresses
–
Install axis without tension. Make sure that
the contact surface is flat
–
Change the layout of the attachment compo-
nent (e.g. payload).
–
Align axes parallel to each another.
Current controller set-
tings.
Optimise controller data (e.g. velocity, accelera-
tion, ...).
Resonance oscillation
of the axis.
Change the travel velocity.
Wear on bearing or
guide.
–
Contact local Festo Service.
–
Wear of the ball screw
drive.
–
Check reversing backlash
permissible reversing backlash.
–
Contact local Festo Service.
–
Vibrations on the slide. Operation at the reso-
nant frequency of the
axis.
–
Change the travel velocity.
–
Change the acceleration.
–
Increase axis stiffness (e.g. shorter support
distances).
–
Change the payload geometry.
Long oscillations of the
profile.
Resonant frequency of
profile and payload too
low.
–
Increase axis stiffness (e.g. shorter support
distances).
–
Change the payload geometry.
Slide does not move.
Coupling slips.
Check the mounting of the shaft-hub connection
è
Instruction manual for the motor mounting
kit,
Loads too high.
Reduce forces and torques. Consider dynamics.
Screws for mounting
the attachment com-
ponent are too long
(e.g. payload).
Observe the screw-in depth
Ball screw drive
blocked.
–
Contact local Festo Service.
–
Overruns the end posi-
tion.
Sensor does not
switch.
Check sensor, installation and parameterisation.
Idling torque too high.
Wear in the drivetrain.
s
–
Wave formation on the
cover strip or alumi-
nium abrasion on the
axis.
Wear on belt reversals.
–
Retension cover strip
–
Replace belt reversal and cover strip
Tab. 10: Overview of fault clearance
10.2
Repair
The product can be repaired or maintained.
–
Spare parts and accessories
–
Replace with an identical product
11
Disassembly
WARNING
Unexpected movement of components.
Injury due to impacts or crushing.
• Before working on the product, switch off the control and secure it to prevent it
from being switched back on accidentally.
WARNING
Risk of Injury due to Unexpected Movement of Components
For vertical or slanted mounting position: when power is off, moving parts can
travel or fall uncontrolled into the lower end position.
• Bring moving parts of the product into a safe end position or secure them
against falling.
1. Disconnect electrical installations.
2. Remove the mounted attachment component.
3. Remove the attached accessories.
4. Remove motor and mounting kit.
5. Remove the mounting attachments.
6. Observe transport information
12
Technical data
12.1
Technical data, mechanical
Use the Festo sizing software for sizing the drive
Size
32
45
60
80
Spindle pitch
8P
10P
12P
16P
Design
Electromechanical axis with ball screw drive
Guide
Recirculating ball bearing guide
Mounting position
any
Max. feed force Fx
[N]
40
100
200
350
Max. no-load drive torque at
vmax
[Nm]
0.04
0.12
0.25
0.4
Max. rotational speed
[rpm]
4500
3600
4000
3750
Max. velocity
[m/s]
0.6
0.8
1
Max. acceleration
[m/s
2
]
15
Repetition accuracy
[mm]
± 0.015
± 0.01
Reversing backlash
[mm]
Tab. 9 Maximum permissible reversing backlash
Feed constant
[mm/rev]
8
10
12
16
Ambient temperature
[°C]
0 … +50
Storage temperature
[°C]
–20 … +60
Degree of protection
IP40
Max. permissible forces and torques on the slide
Fy
[N]
150
300
600
900
Fz
[N]
300
600
1800
2700
Mx
[Nm]
1.3
5.5
29.1
59.8
My
[Nm]
1.1
4.7
31.8
56.2
Mz
[Nm]
1.1
4.7
31.8
56.2
Calculating the load comparison factor
fv
Tab. 11: General data; ELGC-BS
Size
32
45
60
80
Materials
Note on materials
Contains PWIS
Profile
Anodised aluminium
Drive cover
End cap
Die-cast aluminium, painted
Slide
Die-cast aluminium
Guide
Ball bearing
Ball screw
Screws
Steel
Cover strip
High-alloy steel
Belt reversal
Polyoxymethylene
Weight
Basic weight at 0 mm stroke
[kg]
0.3
0.73
1.70
2.95
Added weight per 1000 mm
stroke
[kg]
1.8
3.6
5.1
8.8
Tab. 12: Materials and weight
12.2
Characteristic curves
Velocity – rotational speed ELGC-BS-32/45/60/80
Velocity v as a function of the rotational speed n.
Rotational speed n and velocity v are stroke-dependent. Observe the maximum
permissible velocity v as a function of the working stroke l.