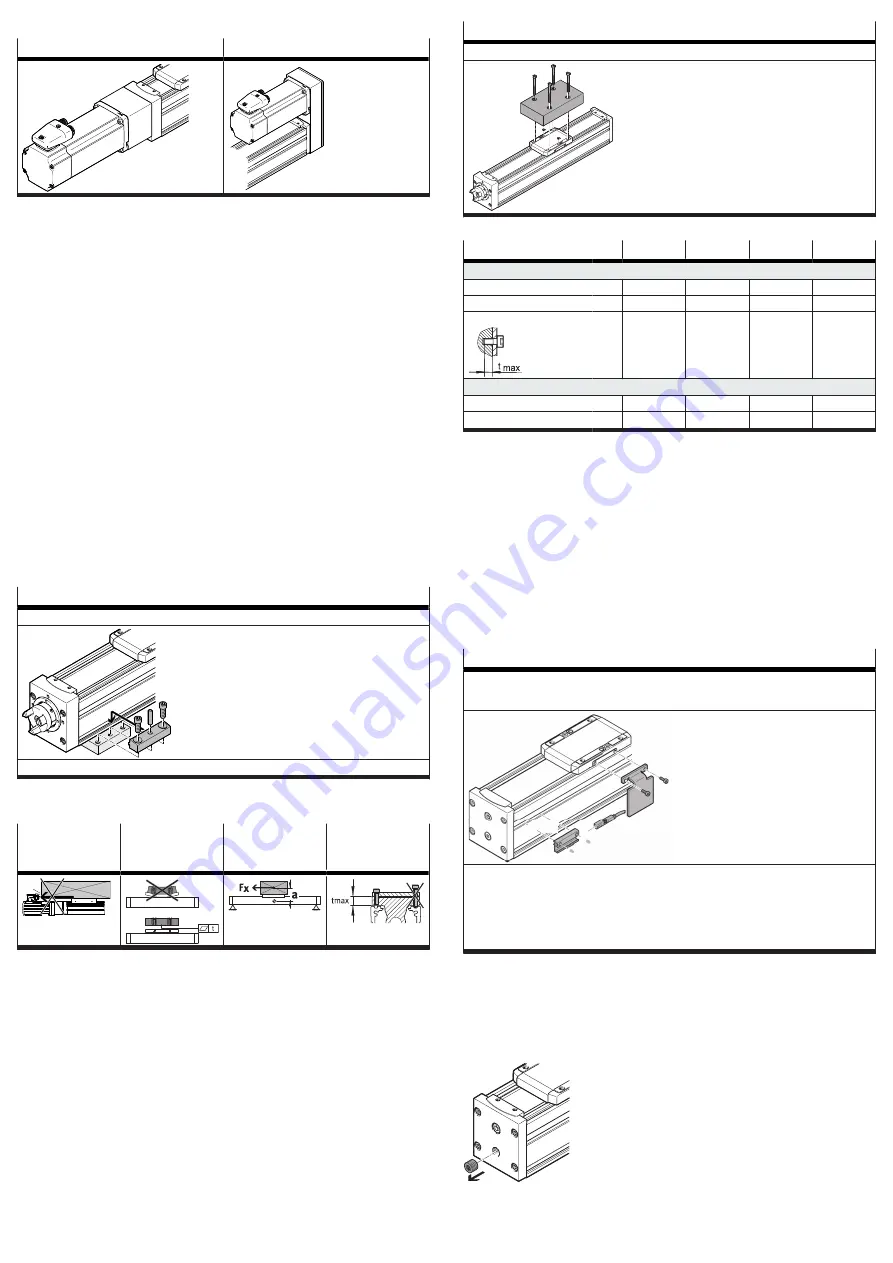
6.3
Mounting the motor
Axial kit EAMM-A
Parallel kit EAMM-U
Tab. 1: Overview of motor mountings
Only loosen screws or threaded pins that are described in the directions in the
instruction manual.
1. Select the motor and motor mounting kit from
Festo
When using other motors: observe the critical limits for forces, torques and
velocities.
2. Fasten motor mounting kit, observe instructions
3. Fasten the motor without tension. Support large and heavy motors.
Connect motor cables only on completion of mounting.
6.4
Mounting axis
Requirement
–
No collision in the movement space of the attachment component with motor,
mounting and sensor components.
–
Sufficient space to reach maintenance interfaces.
–
Sufficient space for reaching and securing the sealing air connection.
–
Flatness of the mounting surface of 0.05 %of the stroke length or maximum
0.5 mm over the stroke length of the bearing surface.
–
No distortion or bending when installing the product.
1. Select mounting attachments
2. Place the mounting attachments on the support points.
3. Tighten retaining screws.
Observe the maximum tightening torque and screw-in depth.
In the case of planar and 3-dimensional gantries, pay attention to parallelism,
product height and alignment of the axes.
For additional information, contact your local Festo Service.
Profile mounting EAHF-L2
Mounting via profile groove
Instruction manual
Tab. 2: Overview of mounting component
6.5
Mounting the attachment component
Collision-free
Flatness
Centre of gravity
and tilting
moment
Max. screw-in
depth
Tab. 3: Requirement for attachment component
Requirement:
–
No collision in the movement space of the attachment component with motor,
mounting and sensor components.
–
Flatness of the mounting surface of the attachment component of 0.01 mm
above the slide surface.
–
Minimise breakdown torque with force Fx. Short lever arm a from the centre of
the guide
to the centre of gravity of the attachment
–
The maximum screw-in depth of the retaining screws is not exceeded.
1. Select accessories
2. Place centring components in centring holes.
3. Position the attachment component on the slide.
4. Tighten retaining screws.
Observe max. tightening torque and max. screw-in depth.
When using an additional guide axis or external guide, ensure that the axes and
guide are aligned exactly parallel.
Recommendation: use guide mountings with tolerance compensation.
Direct fastening
Mounting via thread
Tab. 4: Overview of attachment component
Size
32
45
60
80
Direct fastening
Screw
M3
M4
M5
M6
Max. tightening torque
[Nm]
1.2
2.9
5.9
9.9
Max. screw-in depth t
max
[mm] 5.3
7.8
10.8
14.7
Centring (bore tolerance H7)
Centring pins
[mm]
Æ
2
Æ
4
–
–
Centring sleeve
[mm] –
–
Æ
5
Æ
7
Tab. 5: Information on attachment component
6.6
Mounting accessories
Requirement
–
No collision in the movement space of the attachment component with motor,
mounting and sensor components.
–
Protection against uncontrolled overtravel of the end positions.
–
Referencing to reference switch or end position.
–
Query of end positions or intermediate positions.
1. Select accessories
2. Mount the sensor (reference or query):
–
Mount the sensor bracket and switch lug (depending on the type of
mounting).
–
Mount the sensor.
Sensor bracket
–
Switch lug: mounting on slide
–
Sensor bracket: mounting via profile groove
–
Sensor: mounting on the sensor bracket
–
Protect the sensor from external magnetic or ferritic influences (e.g. min. 10 mm distance to slot
nuts).
–
Preferably use hardware limit switches with normally closed function (protection guaranteed even
in case of sensor failure).
–
Query switching lug only with inductive sensor.
–
Query integrated magnets in the slide only with magneto-resistive sensor.
Tab. 6: Overview of sensor mounting
Connecting sealing air
The use of overpressure or negative pressure in the range of approx. ± 0.02 MPa
(± 2.9 psi; ± 0.2 bar) reduces or prevents the following contamination:
–
The application of negative pressure minimises the release of abraded particles
into the environment.
–
Applying overpressure reduces the penetration of dirt into the drivetrain.
Fig. 3: Connecting sealing air
1. Remove the sealing air plug screw from the threaded hole.
2. Mount the screw fitting and connect the hose.