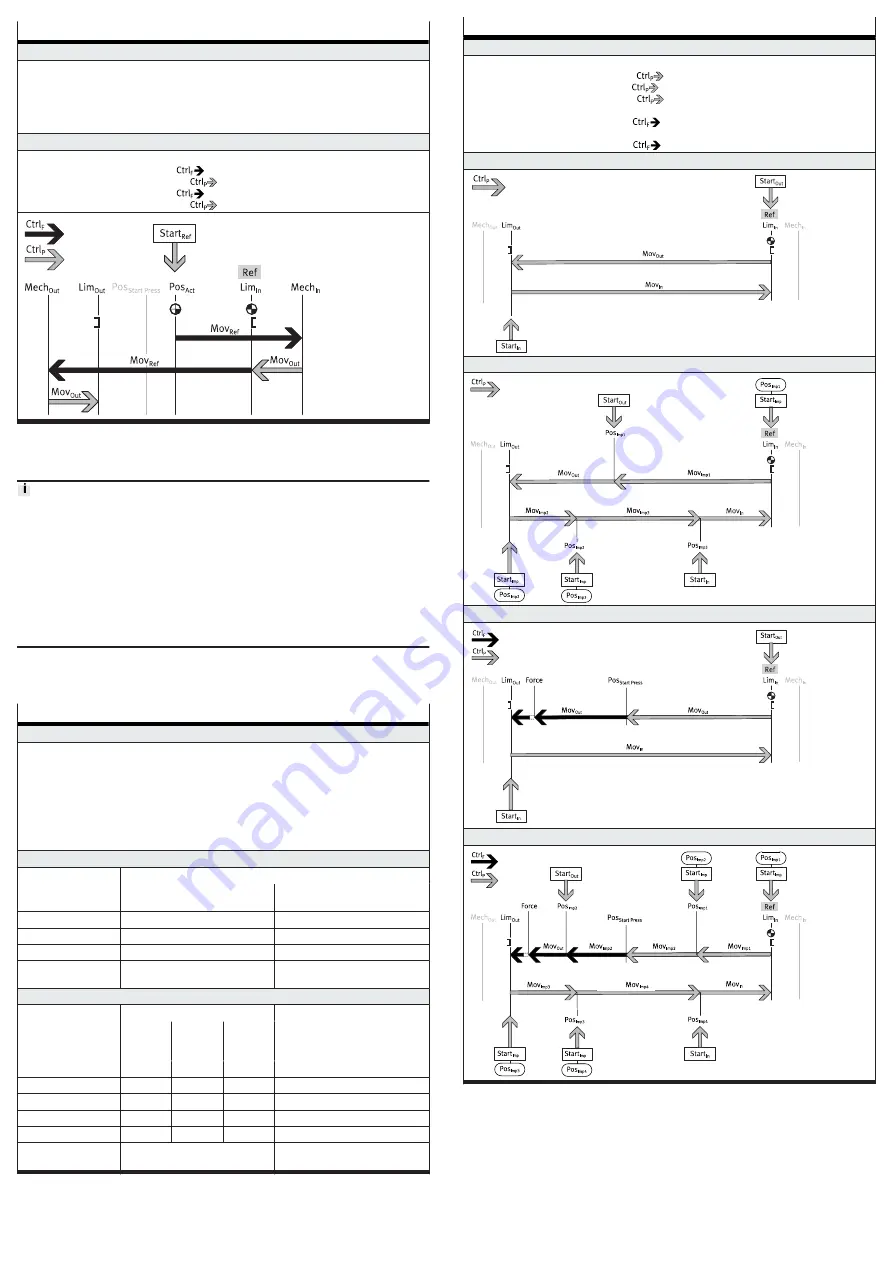
Activate referencing with end position determination Start
Ref
Factory setting: motor-facing reference end position "Ref"
–
HMI: activate "Reference" menu, parameterise reference end position "Ref" and initiate refer-
encing movement
9.4 Display and operating components (HMI)
–
IO-Link, process data: parameterise reference end position "Ref" 0x0103.0, false (factory set-
ting) or true and initiate referencing movement 0x0104.0 = true
–
IO-Link, system parameters: 0x0002, value = 0xCE (Execute "Reference" Movement (False),
factory setting) or value = 0xCF (Execute "Reference" Movement (True))
Sequence
The diagram shows the referencing movements with end position determination
–
Mov
Ref
: force-controlled movement
against mechanical stop "Mech
In
"
–
Mov
Out
: position-controlled movement
to the reference end position "Ref"
–
Mov
Ref
: force-controlled movement
against the mechanical stop "Mech
Out
"
–
Mov
Out
: position-controlled movement
to the end position Lim
Out
Tab. 5: Initialise referencing sequence with reference end position "Ref" and end
position determination
9.6
Point-to-point operating modes
Automatic saving of device data
If automatic storage is activated (0x0109.0 = true, default), parameter changes
in the device data (= data storage parameters
è
"Integrated drive EMCS"
www.festo.com/sp) are made automatically and perma-
nently saved in the flash memory. Exceeding the maximum permissible 100,000
write cycles results in irreparable damage to the flash memory and the device,
e.g. when using the device for positioning tasks via IO-Link.
If automatic saving is deactivated (0x0109.0 = false), parameter changes are
only temporarily stored in the RAM. The RAM permits an unlimited number of
parameter changes, e.g. for positioning tasks via IO-Link.
For single point-to-point operation the drive can be traversed to the target posi-
tions "end positions "Lim
In
/Lim
Out
and intermediate positions Pos
Imp
" (IO-Link
only).
Point-to-point operation
Parameterise point-to-point operation
HMI:
–
Speed Out, Speed In, Force and Start Press
9.4 Display and operating components (HMI)
IO-Link (acyclic device data):
–
Velocity Speed Out: 0x0101.0, Speed Out
1)
–
Velocity Speed In: 0x0100.0, Speed In
1)
–
Force/Torque: 0x0102.0, Force
1)2)
–
Start Press Position Pos
Start Press
: 0x0105.0, Position Start Press [mm]
2)3)4)
–
End position Lim
Out
: 0x0106.0, end position Out [mm]
4)
–
Intermediate position Pos
Imp
: 0x0108.0, Intermediate Position [mm]
3)4)
Control point-to-point operation via digital inputs
Positioning task
Control signals
Mov
In
DI1 [Logic, Pin 5]
Mov
Out
DI2 [Logic, Pin 6]
Start
In
/Mov
In
1
0
Start
Out
/Mov
Out
0
1
Stop
5)
0
0
Switch off power
stage
6)
1
1
Control point-to-point operation via IO-Link
Positioning task
Process parameters
System parameters
Move "In" Move
"Out"
Move
"Inter-
mediate"
System commands
0x0029.1
0x0029.2
0x0029.5
0x0002
Start
In
/Mov
In
true
false
false
= 0xC8, Execute "Move
In
"
Start
Out
/Mov
Out
false
true
false
= = 0xC9, Execute "Move
Out
"
Start
Imp
/Mov
Imp
false
false
true
= 0xD0, Execute "Move
Intermediate
"
Stop
5)
false
false
false
= 0xCA, stop motion
Switch off power
stage
6)
³
2 x true
= 0xCB, disable power stage
Point-to-point operation
Sequence
The diagrams show the movements in point-to-point operation
–
Mov
Out
: position-controlled movement
to the end position "Lim
Out
"
–
Mov
In
: position-controlled movement
to the end position "Lim
In
"
–
Mov
Imp
: position-controlled movement
to the intermediate position "Pos
Imp
"
–
Point-to-point operation with press function, from Start Press Position "Pos
Start Press
"
–
Mov
Out
: force-controlled movement
until the parameterised force or torque setpoint
value "Force" is reached or to the end position "Lim
Out
"
–
Mov
Imp
: force-controlled movement
to the intermediate position "Pos
Imp
" (IO-Link only)
Simple point-to-point operation
Simple point-to-point operation with intermediate position (IO-Link only)
Point-to-point operation with press function
Point-to-point operation with press function and intermediate position (IO-Link only)
1) 10, 20, ..., 100% of maximum value
2) Only required for point-to-point operation with press function
3) Reset at every referencing
4) Reference point: reference end position "Ref"
5) The output stage remains active, the drive decelerates to standstill and remains stationary position-con-
trolled.
6) In error-free status the power stage is switched off after 3 s, the drive coasts to a standstill and remains
stationary unregulated.
Tab. 6: Parameterise and control point-to-point operation