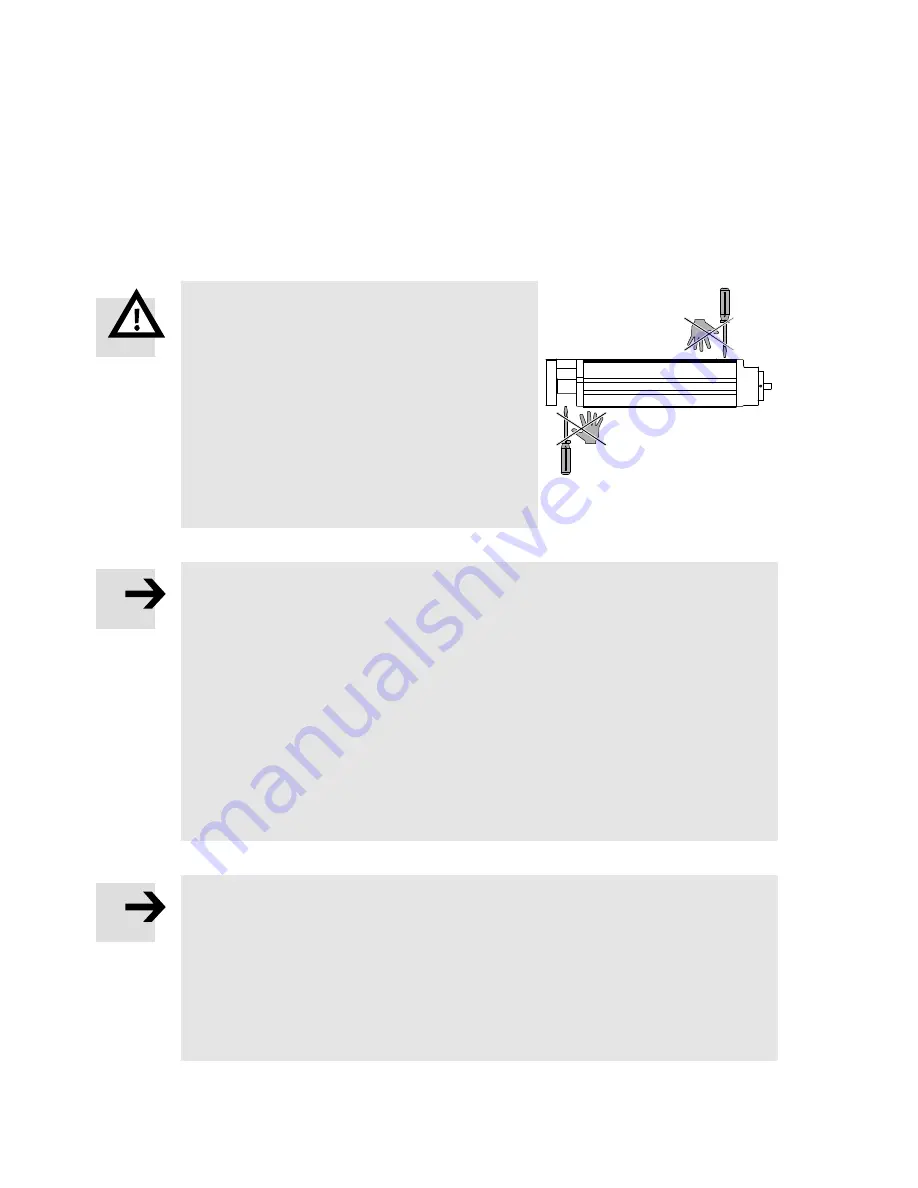
EGSL
Festo EGSL 2017-11c English
12
6
Commissioning
Warning
Moving masses can cause personal injury and
material damage (crushing).
Make sure that, in the travel range,
– nobody can place his/her hand in the
path of the moving load
(e.g.by use of a protective crate),
– there are no foreign objects.
It should not be possible to touch the EGSL
until the mass has come to a complete
standstill.
Fig. 11
Note
Incorrect default values of the braking ramp in STOP conditions
(e.g. EMERGENCY STOP and quick stop) result in overloading of the linear
axis and can damage it or drastically reduce its service life.
Check the settings for all braking ramps on your controller or the higher-order
controller (deceleration values and jerking).
Taking the travel speed, moveable load and mounting position into account,
make sure that the delay values (brake delay and delay times) are set in such
a way that the maximum drive torque or feed force of the linear axis used is
not exceeded.
Use the Festo “PositioningDrives” sizing software to design the mini slide
è
www.festo.com.
Note
Block-step acceleration profiles (without smoothing) cause high peaks in the
motive force that can lead to drive overload. In addition, positions outside the
permissible range may occur as a result of overswing effects. A jolt-limited
acceleration specification reduces vibrations in the entire system and has a
positive effect on stress in the mechanical system.
Check which controller settings may be adapted (e.g. jolt limitation and
smoothing the acceleration profile).