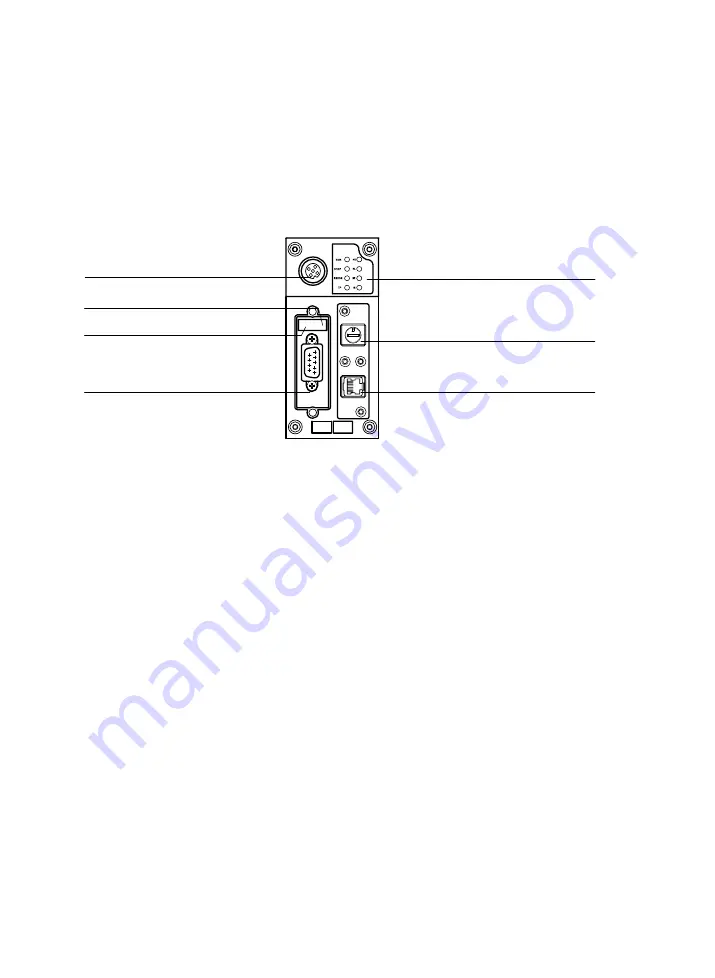
2. Installation
2−6
Festo P.BE−CPX−CEC−EN en 1004a
2.3
Connection and display elements
2
3
4
6
7
5
1
1
Status LEDs
2
RUN/STOP rotary switch
3
Ethernet interface
(10/100BaseT, RJ45)
4
CPX−CEC−C1/−M1:
CANopen interface
(plug, 9−pin, Sub−D )
CPX−CEC:
RS232 interface
(socket, 9−pin, Sub−D)
5
DIL switch 1
6
DIL switch 2
7
Connection for a handheld of type
CPX−MMI
Fig.2/2:
Connection and display elements (here for CPX−CEC−C1/−M1 as an example)
Содержание CPX-CEC
Страница 2: ......
Страница 17: ...System summary 1 1 Festo P BE CPX CEC EN en 1004a Chapter 1 ...
Страница 33: ...Installation 2 1 Festo P BE CPX CEC EN en 1004a Chapter 2 ...
Страница 53: ...Commissioning 3 1 Festo P BE CPX CEC EN en 1004a Chapter 3 ...
Страница 68: ...3 Commissioning 3 16 Festo P BE CPX CEC EN en 1004a ...
Страница 69: ...Diagnosis 4 1 Festo P BE CPX CEC EN en 1004a Chapter 4 ...
Страница 76: ...4 Diagnosis 4 8 Festo P BE CPX CEC EN en 1004a ...
Страница 77: ...Technical appendix A 1 Festo P BE CPX CEC EN en 1004a Appendix A ...
Страница 82: ...A Technical appendix A 6 Festo P BE CPX CEC EN en 1004a ...
Страница 83: ...Index B 1 Festo P BE CPX CEC EN en 1004a Appendix B ...
Страница 84: ...B Index B 2 Festo P BE CPX CEC EN en 1004a ...