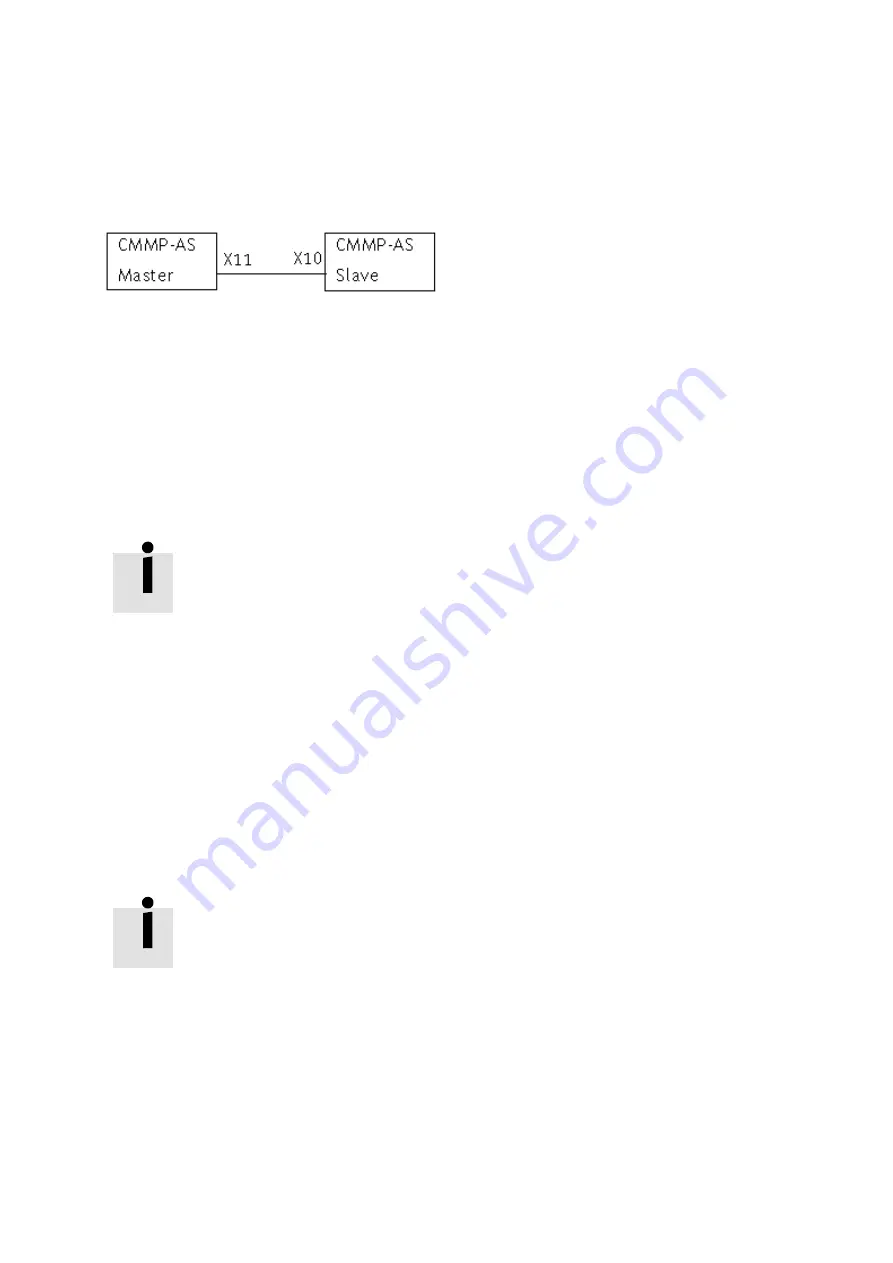
2. Hardware components
13
Festo.P.BE-CMMP-CAM-SW-EN en 1105a
2.4
Connections X10/X11 and connecting cables
In the case of the “physical master” (see section 4.3), the encoder signals are transmitted
over the X10 and X11 inputs or outputs.
2.4.1
Output X11
The
output X11
delivers an increment-generator signal with the following characteristics:
–
TTL (transistor-transistor logic)
–
6 tracks (A, B and zero pulse, each also inverted)
–
RS 422
The precise specification and pin allocation can be found in the
hardware description according to section 1.3, documentation
overview.
2.4.2
Input X10
At the
input X10
, besides another CMMP-AS, many additional, commercially available
encoders can be connected, such as encoders corresponding to the industry standard
ROD426 from Heidenhain or encoders with single-ended TTL outputs as well as “open-
collector” outputs.
Alternatively, the A and B track signals from the device are interpreted as pulse direction
signals, allowing the controller to be controlled from stepper motor control cards.
The precise specification and pin allocation can be found in the
hardware description according to section 1.3, documentation
overview.