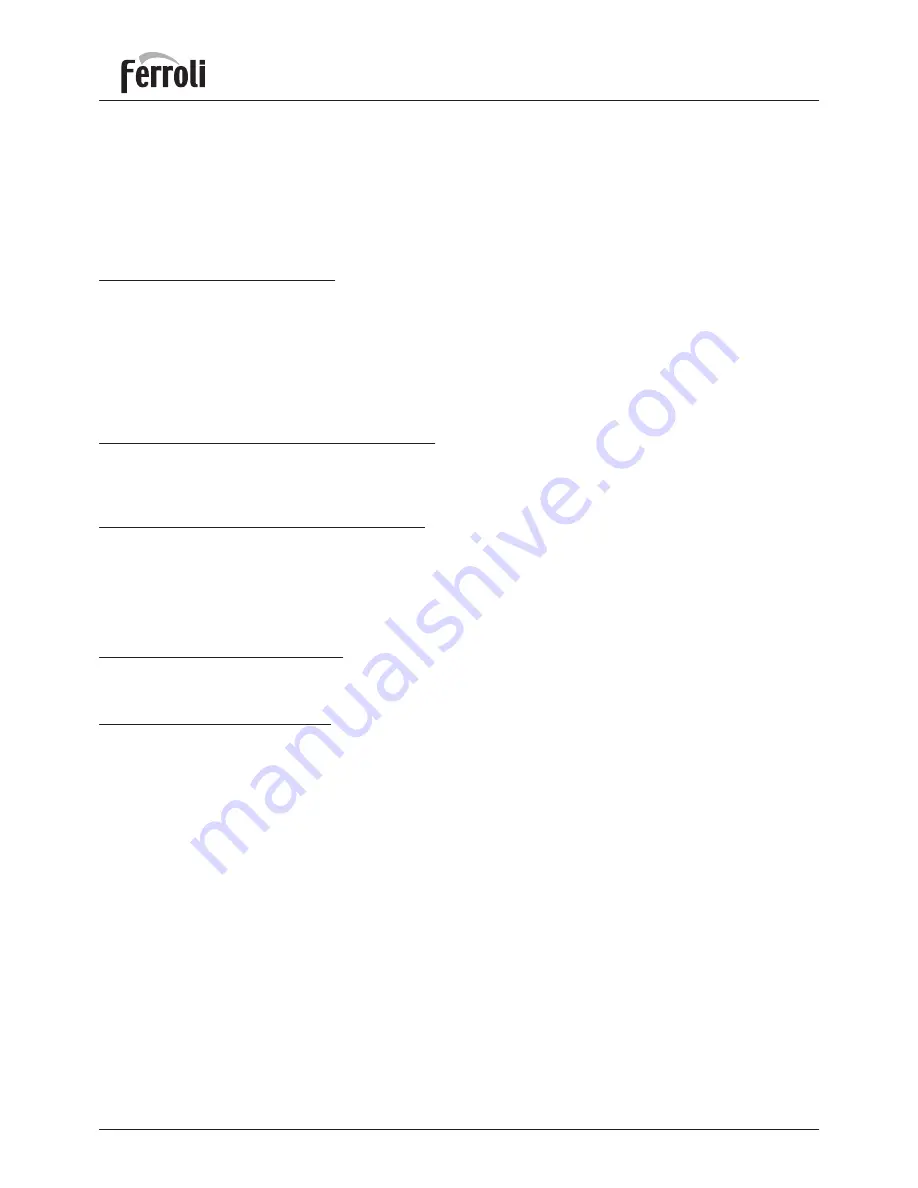
Rendimax N EL
8
4. CHECKS AND MAINTENANCE
Attention
Current technical standards envisage periodic maintenance of the appliance, as well as analysis of the composi-
tion of the flue gas, to check correct combustion in the burner assembly. As a result, it is suggested that the user
stipulate a programmed maintenance contract with a specialised company to periodically carry out the operations
listed below.
4.01 General notes on maintenance
Have the correct operation and integrity of the flue checked periodically.
In the event of work or maintenance on structures located near the flues and/or flue gas discharge devices and
accessories, shut the appliance down and, upon completion of the work, have the condition of such parts checked
by professionally qualified personnel.
Do not clean the appliance and/or its parts with easily inflammable substances (e.g. petrol, alcohol, etc.).
Do not leave containers with inflammable substances in the room where the appliance is installed.
4.02 System checks (to be performed once a year)
The system is generally checked at the end of the winter season. Check that the water in the expansion vessel is
pressurised. Verify serviceability and operation of the pumps.
4.03 Boiler checks (to be performed once a year)
• Check the boiler for correct operation by effecting ignition and shut-down tests using the regulation
thermostat.
• Check on the rear wall of the boiler, at the height of the draught diverter, that there are no flue gas leaks, signs
of any blockages in the flue or insufficient draught.
• Check that the connecting pipe between the boiler and flue is perfectly sealed at the joints.
4.04 Cleaning the boiler and the fl ue
To be performed once every 3 years.
4.05 Cleaning the burner assembly
To be performed once a year.
Содержание RENDIMAX N EL
Страница 2: ......
Страница 28: ...FERROLI S p A Via Ritonda 78 a 37047 San Bonifacio Verona ITALY www ferroli it...