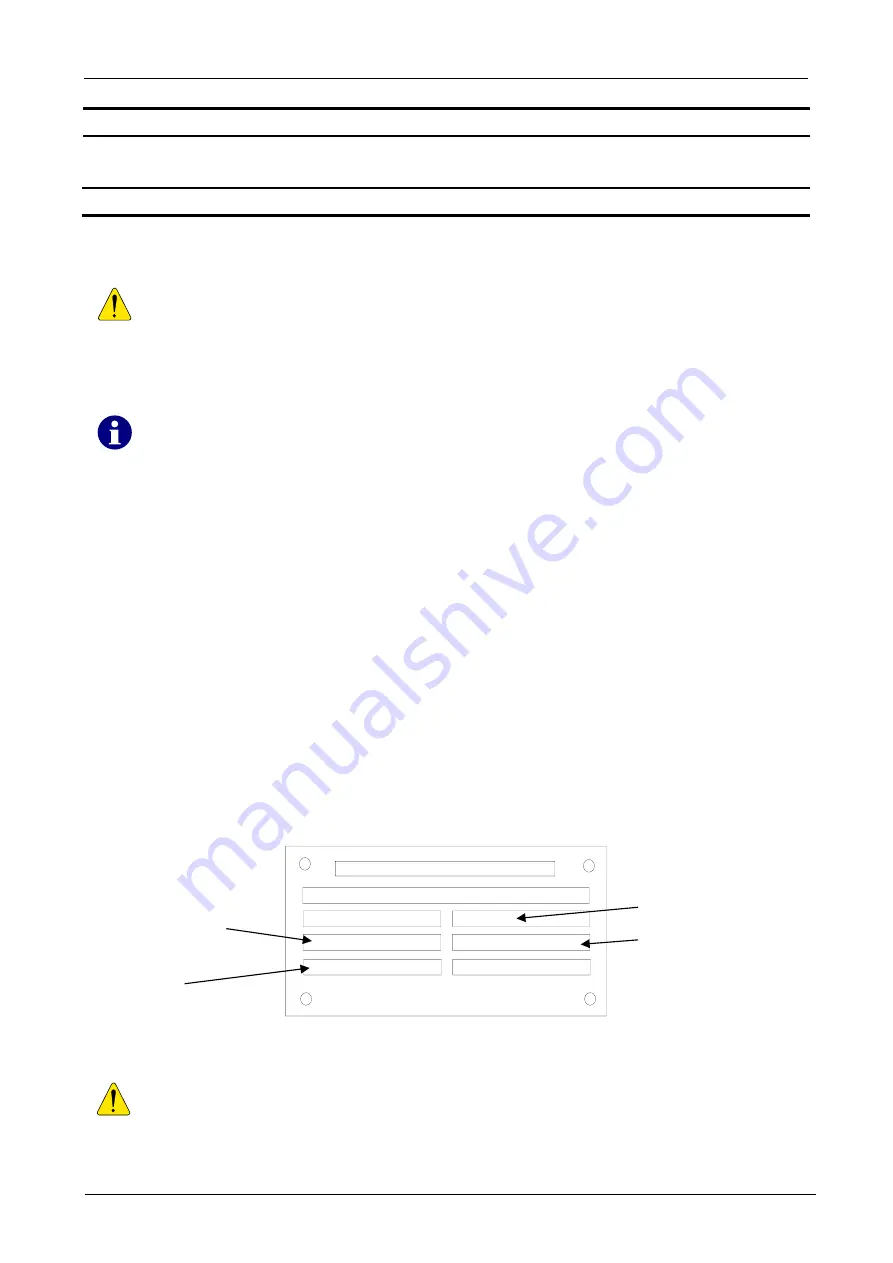
TST
Assembly instructions
FUF2 / FU3F-A/-C/-F
FEIG ELECTRONIC GmbH
Page 70 of 114
TST_FUxF-A-C-F_Montageanleitung_EN_15
8
Basic settings
To put the controller into operation, please follow the steps outlined in these instructions.
8.1 Automatic query of basic data
If the controller is not already preconfigured by the door manufacturer, the following parameters
are queried automatically:
DIP switch S1300 must be switched on so that the controller can automatically
request the parameters (position S1300 see Figure 41: DIP switch position).
If DIP switch is not turned on and the basic parameters not set, error code F.090 is
displayed.
The controller uses indicator "-1" or "-" in the display as a flag that the acquisition of this
parameter must be queried.
The basic data does not require changes when they were previously retrieved and set
automatically. For operating the controller, see chapter
Positioning system P.205
The limit switch system in use must be set using Parameter P.205.
0000 = Mechanical limit switches Version 1 (Figure 28: Connecting cam switches)
0001 = Mechanical limit switches Version 2 (limit switches and pre-limit switches are normally
closed)
0200 = Incremetal encoder
0300 = Absolute encoder DES-A (GfA)
0700 = Absolute encoder DES-B (Kostal)
0800 = Absolute encoder TST PD / TST PE (FEIG)
0900 = Timer limit switches
Motor data P.100
–
P.103
The door controller uses the following parameter setting to learn about the type of motor being
used. Read the data from the nameplate and enter them into the corresponding parameters.
Manufacturer
Type designation
0,5 KW
50 Hz
Iso.Kl.: F
IP 55
Figure 42: Typical motor nameplate (may vary)
Be sure to note the Y/
wiring of the motor. The motor data must be entered in
accordance with the motor wiring. For the TST FUF2 the 400V setting is not
applicable, since the controller can source a maximum motor voltage of 230V.
cos
0.85
P.101: Motor
current
P.102: Cos
P.100: Nominal motor
frequency
P.103: Nominal motor
voltage
/ Y 2.4 / 1.4 A
/ Y 230 / 400 V