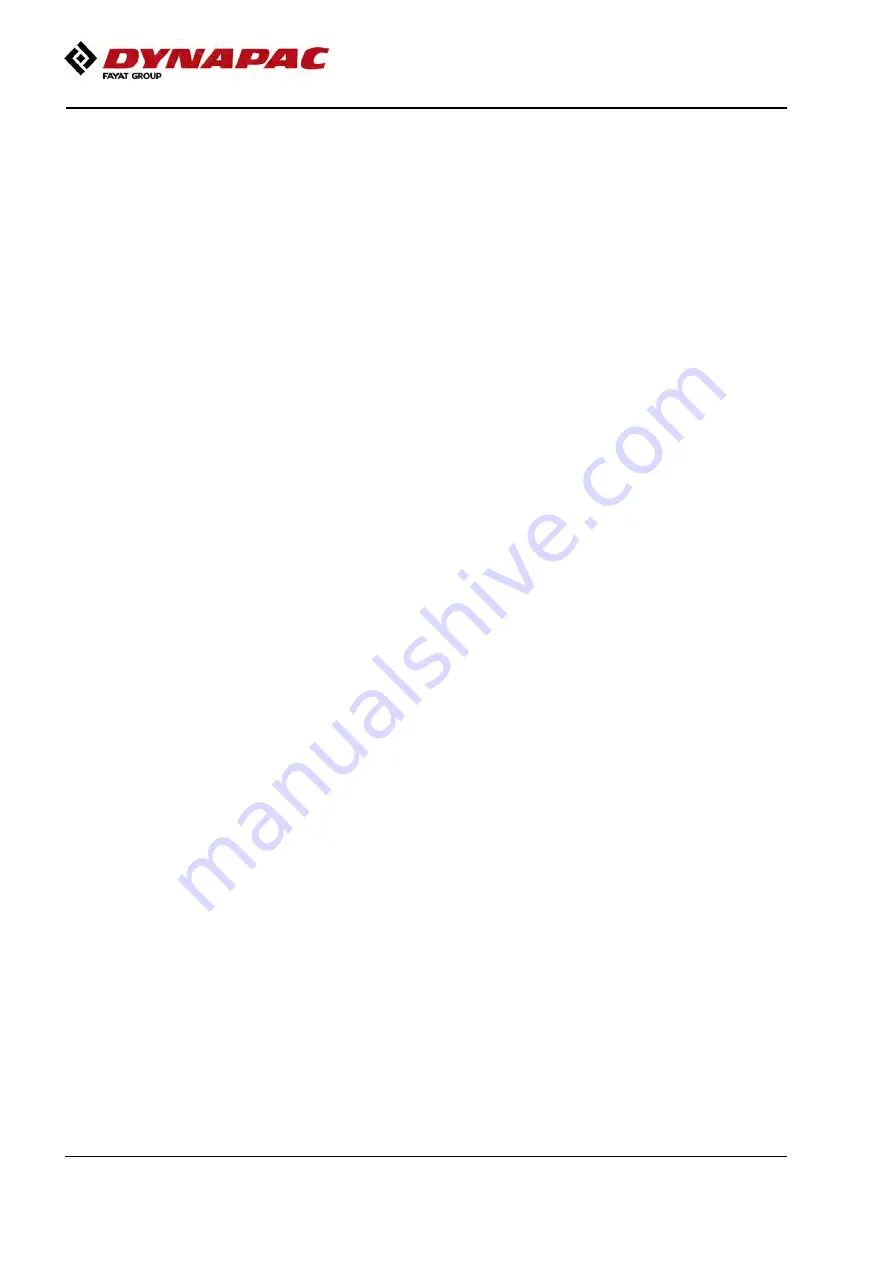
year)
other
(Every
month
24th
every
Maintenance,
4812163101_A.pdf
2018-12-14
D1803 ......................................................................................... 61
Interlock/Emergency stop/Parking brake - Check ..................................... 62
Edge cutting (Optional) ............................................................................. 63
Vibration .................................................................................................................. 64
Manual/Automatic vibration....................................................................... 64
Braking .................................................................................................................... 65
Normal braking.......................................................................................... 65
Emergency braking ................................................................................... 65
Switching off.............................................................................................. 66
D1703 ......................................................................................... 66
D1803 ......................................................................................... 66
Parking .................................................................................................................... 67
Chocking the wheels/drum........................................................................ 67
Battery disconnector ................................................................................. 67
Long-term parking.................................................................................................................. 69
Engine ....................................................................................................... 69
Battery....................................................................................................... 69
Air cleaner, exhaust pipe........................................................................... 69
Fuel tank ................................................................................................... 69
Hydraulic reservoir .................................................................................... 69
Steering cylinder, hinges, etc. ................................................................... 70
Watering system ....................................................................................... 70
Hoods, tarpaulin ........................................................................................ 70
Miscellaneous ........................................................................................................................ 71
Lifting ....................................................................................................................... 71
Locking the articulation ............................................................................. 71
Lifting the roller.......................................................................................... 72
Lifting the roller with a single -point lift (Optional) ..................................... 73
Unlocking the articulation .......................................................................... 74
Towing/Recovering.................................................................................................. 74
Содержание Dynapac CC1100C VI
Страница 2: ......
Страница 14: ...r h 4812163101_A pdf 2018 12 14 ...
Страница 18: ...Introduction 4812163101_A pdf 2018 12 14 4 ...
Страница 28: ...Special instructions 4812163101_A pdf 2018 12 14 14 ...
Страница 36: ...Technical specifications 4812163101_A pdf 2018 12 14 22 ...
Страница 41: ...Machine description 4812163101_A pdf 2018 12 14 27 ...
Страница 43: ...Machine description 4812163101_A pdf 2018 12 14 29 ...
Страница 47: ...Machine description 4812163101_A pdf 2018 12 14 4812129673 Warning CALIFORNIA Proposition 65 33 ...
Страница 82: ...Operation 4812163101_A pdf 2018 12 14 68 ...
Страница 102: ...Operating instructions Summary 4812163101_A pdf 2018 12 14 88 ...
Страница 104: ...Preventive maintenance 4812163101_A pdf 2018 12 14 90 ...
Страница 108: ...Maintenance Lubricants and symbols 4812163101_A pdf 2018 12 14 94 ...
Страница 117: ...Maintenance Maintenance schedule 4812163101_A pdf 2018 12 14 Service Checklist 103 ...
Страница 118: ...Maintenance Maintenance schedule 4812163101_A pdf 2018 12 14 104 ...
Страница 128: ...Maintenance 10h 4812163101_A pdf 2018 12 14 114 ...
Страница 184: ...Maintenance 2000h 4812163101_A pdf 2018 12 14 170 ...
Страница 202: ...Maintenance 3000h 4812163101_A pdf 2018 12 14 188 ...
Страница 207: ...Dynapac Compaction Equipment AB Box 504 SE 371 23 Karlskrona Sweden www dynapac com ...