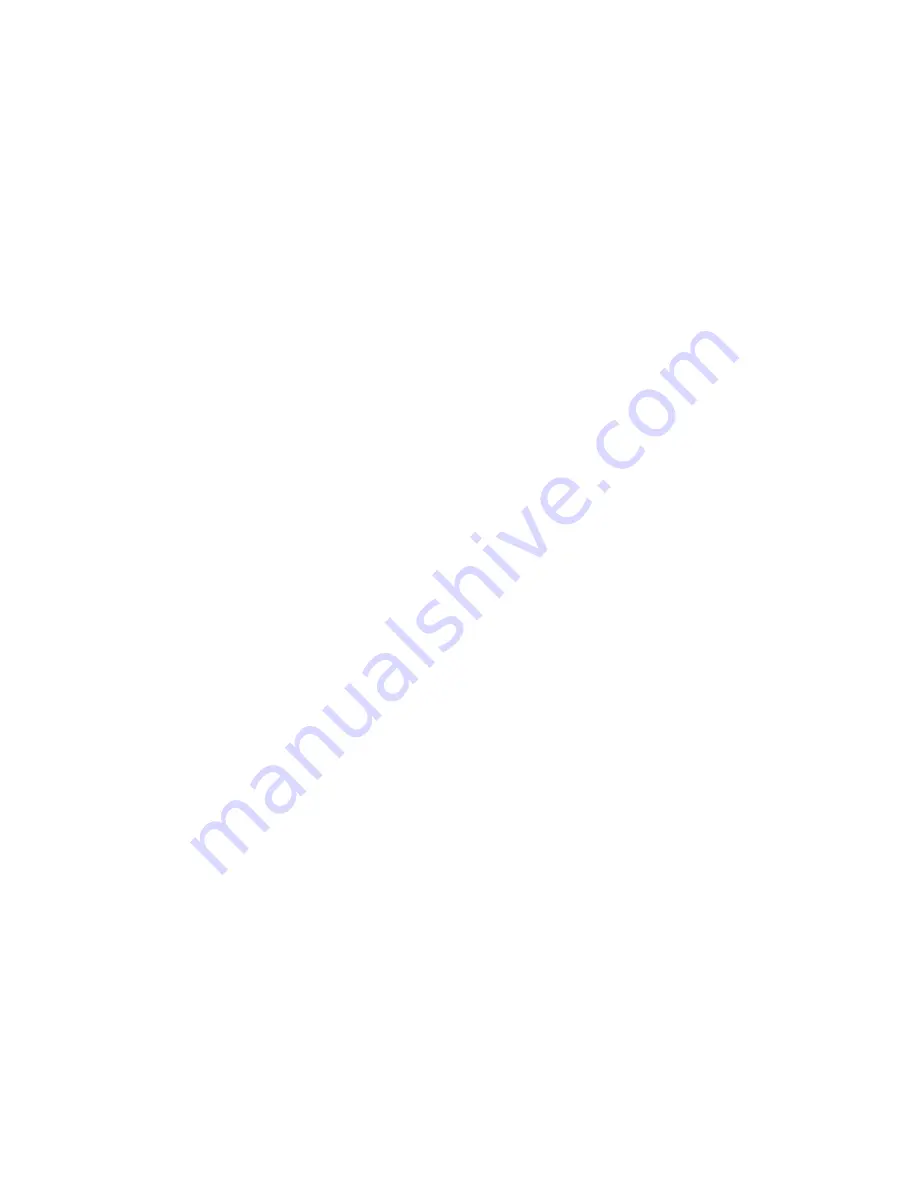
III. Adjustment of fuel injector
Testing and adjustment for fuel injector should be performed on a tester. The purpose is to
adjust the fuel-injecting pressure and eliminate faults.
If fuel-injecting pressure inside the oil injector is too high or too low, fuel-injection is
abnormal, and part(s) is damaged, when the engine runs, faults will occur, such as the occurrence
of black smoke, decrease of power and speed, increase of exhaust temperature or knock of
cylinder etc. For fuel injector judged to be faulted, in-turn cylinder-stoppage method can be used.
That is, loosen the oil injector and high-pressure oil pipe one by one, and stop injecting oil. At the
same time, watch the color of exhaust gas. If faulted injector stops injecting oil, exhaust gas will
stop producing black smoke. Now, speed of engine has little or no change. It is also possible to
turn the flywheel (by hands) to listen to fuel-injection sound of each cylinder. If the sound is not
clear and melodious, the oil injector is this cylinder may have a fault.
1. Adjusting procedure
(1) Use hand-pump, to pump to a gauge pressure of 12.7MPa. Continue to slowly press the
hand-pump, to raise the gauge pressure to 13.7MPa, at which the fuel is injected. Watch if
fuel-dripping or leakage, at fuel-injection hole at fuel nozzle. If fuel dripping is found in tests by
several times, it is necessary to remove the fuel nozzle couple, for a cleaning. After inspection or
grind, perform test again.
(2) Adjust the pressure of fuel injection. Remove the pressure-adjusting screw cap(s) on the
fuel injector, and loosen or tighten the pressure-adjusting screw(s), make the pressure of fuel
injection to be 13.7MPa. Then, tighten the pressure-adjusting screw cap(s), and perform re-test.
(3) Watch the quality of atomization. Perform atomization test, with a fuel-injecting rate of 1
time/sec. Atomized fuel should be thin, uniform and mist-like, without abnormal phenomena such
as visible splashed tiny foam, local un-uniform density and one-side fuel injection. When the fuel
oil is cut off, an obvious and clear sound should be heard. Abnormal fuel injection is usually
caused by free-less and smooth-less nozzle needle-valve motion. Fuel dripping at fuel-injecting
hole is caused by a damaged sealing surface. Branched fuel beam is caused by a head which is
accumulated with soot or deformed due to heat.
2. Dismantle and repair of fuel injector
(1) When dismantle the oil injector, at first, clean the outer part. With the nozzle facing
upwards, clamp tightly the injector onto a bench clamp padded with copper. Unscrew the screw
cap and take out the needle-valve couple, and pull out the needle-valve and immerse it in clean
kerosene. Turn the fuel injector by 180° and then clamp tightly it. Unscrew the pressure-adjusting
screw cap and pressure-adjusting screw, then the pressure-adjusting spring and push-rod can be
taken out.
40
Содержание 485
Страница 1: ......
Страница 3: ...Written by Zhai Yonghui Huang Qiwei Yang Xueming Reviewed by Wang Xinze Li Peiran Yao Zugen ...
Страница 5: ......
Страница 8: ... I Right view of 4DW81 46 diesel engine 1 ...
Страница 9: ... II Left view of 4DW81 46 diesel engine 2 ...
Страница 10: ... III Front view of 4DW81 46 diesel engine 3 ...
Страница 11: ... IV Vertical view of 4DW81 46 diesel engine 4 ...
Страница 12: ... V Power output end of 4DW81 46 diesel engine 5 ...
Страница 16: ...III External characteristic curve of 4DW engines 1 External characteristic curve of 4DW81 46 B01 9 ...
Страница 17: ...2 External characteristic curve of 4DW81 50 B05 37kW 3200 r min 10 ...
Страница 55: ...Annex Fit Clearance Table 48 ...
Страница 56: ...49 ...
Страница 57: ...50 ...