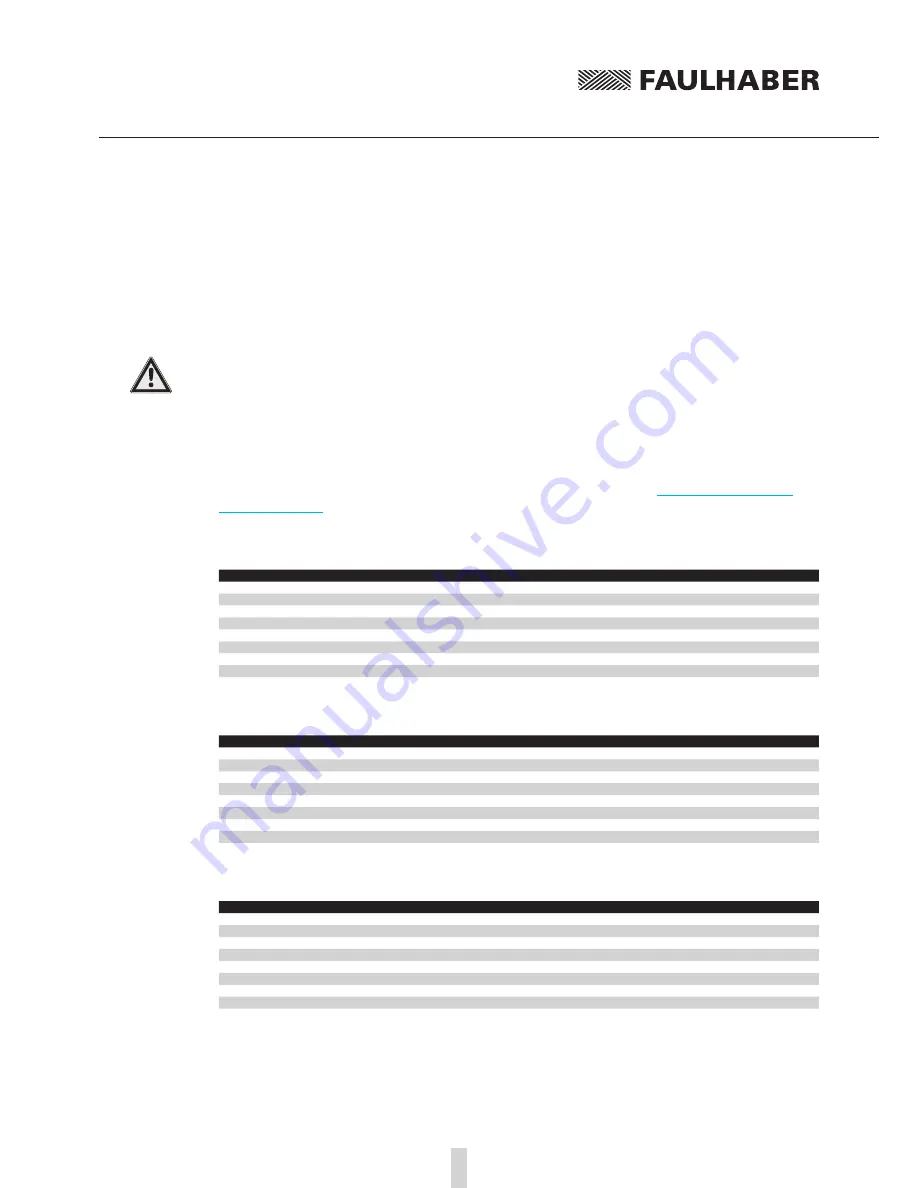
16
3 Installation
3.3 Connections
Depending on their type, Motion Controllers are equipped with either screw-type terminal strips,
flexboard plug-in connectors or pin headers as connection options.
CAUTION!
ESD protection / electronic damage!
Electrostatic discharges at the connections of the Motion Control systems can cause irreparable dam-
age to the electronics.
f
Note and follow the ESD protective measures.
Incorrect connection of the cores can cause damage to or destruction of the electronics.
f
Connect the connections in accordance with the connector pin assignment, see table.
Please also note and follow the supplementary installation instructions in
Chapter 5 “EC Product
Safety Directives”
.
3.3.1 Supply end connection (MCxx 3002 / 3003 / 3006)
Pin
Designation
Meaning
1
TxD / CAN_H
RS232 / CAN interface
2
RxD / CAN_L
RS232 / CAN interface
3
AGND
Analog Ground
4
Fault
Error output
5
AnIn
Analog input
6
U
B
Controller supply voltage
7
GND
Controller ground connection
8
3. In
3. Input / opt. separated power supply
3.3.2 Motor end connection MCDC 3002
Pin
Designation
Meaning
9
4. In
4th input
10
Ch A
Encoder channel A
11
Ch B
Encoder channel B
12
U
CC
Supply voltage for external loads
13
SGND
Signal ground connection
14
Mot +
Supply voltage, motor +
15
Mot –
Supply voltage, motor -
16
5. In
5th input
3.3.3 Motor end connection MCBL / MCLM 3002
Pin
Designation
Meaning
9
Sensor A
Hall sensor A / DATA for absolute encoder
10
Sensor B
Hall sensor B / CS for absolute encoder
11
Sensor C
Hall sensor C / CLK for absolute encoder
12
U
CC
Supply voltage for external loads
13
SGND
Signal ground connection
14
Motor A
Motor Phase A
15
Motor B
Motor Phase B
16
Motor C
Motor Phase C