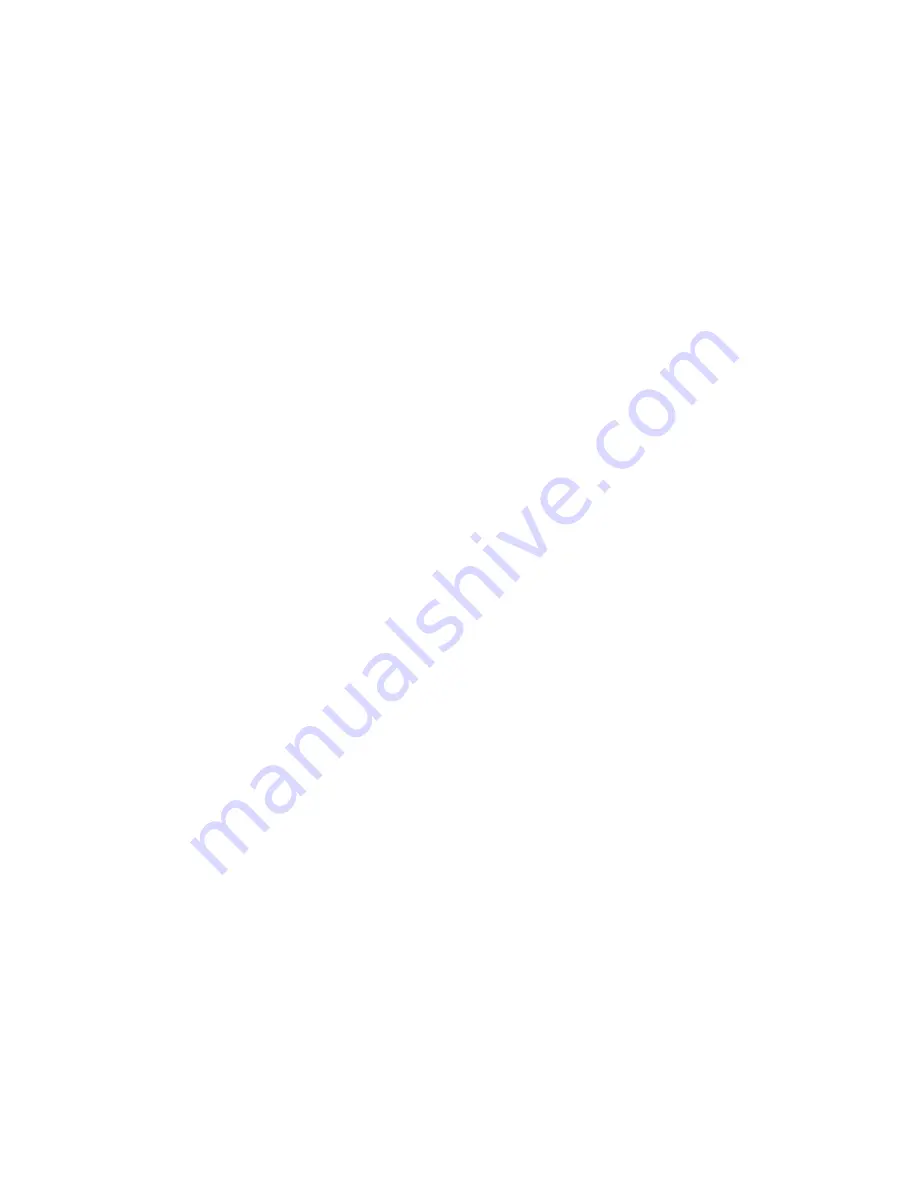
Rotor Replacement
Remove two each fan grids. Remove receptacle panel Remove brush holder
held with one screw. Remove four plastic stop nuts holding front shield (fan
housing)
With gear puller push out rotor from slip ring side. Remove rotor assembly
from stator. Remove snap ring from shaft end which had the Pulley on it. Push
rotor out of front shield. Examine bearing and front shield to be sure it does not
need to be replaced. Push new rotor into front shield. Re-install small snap
ring. Be sure snap ring is in grove. Carefully re-install rotor into stator. Use
rubber mallet to tap into place. Re-install four elastic stop nuts. Tighten elastic
stop nuts in a criss/cross manner. Turn rotor by hand to make sure it turns
freely. If rotor seems not to run freely, tap the casting with a small metal
hammer on the slip ring end casting. This will seat the bearing. Apply 12Volts
to the slip ring for about 20 seconds. This will make sure that the residual
magnetism is energized. Re-install the brush holder. Be sure to have the
insulator behind the brush holder. Check for brush alignment to slip ring. Re-
install the two fan grids. re-install receptacle panel or louvered panel on slip
ring end.
20