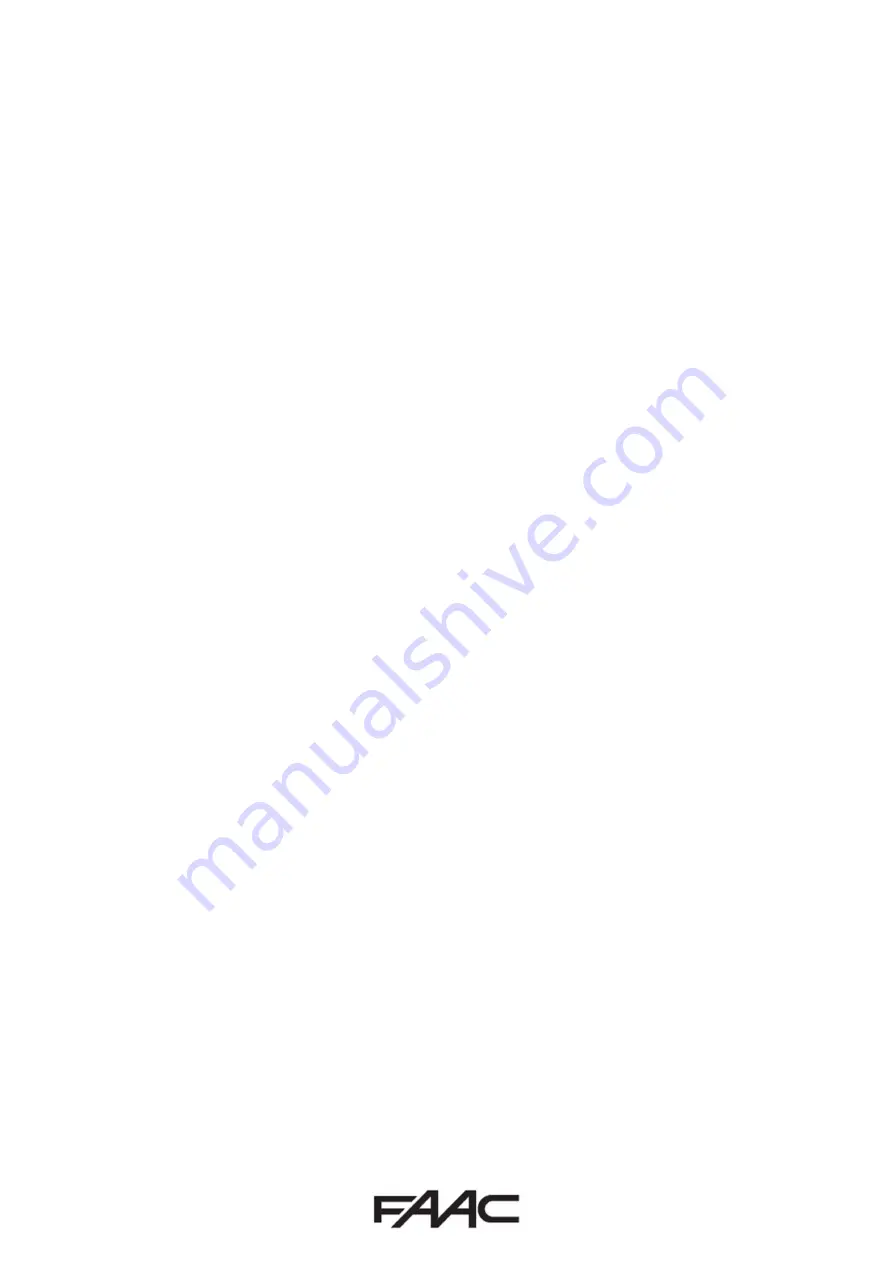
Page | 2
Installation Sequence
1.
Perform a Risk Assessment for the system and resolve by design as many risks as possible
2.
Secure the housing
3.
Mount the motors as detailed in their relevant instructions
4.
Use suitable cabling for the motors (motors should be 2.5mm2 per core minimum) and
accessories (BUS devices must be wired using a minimum 2 core, 0.5mm multi-stranded
screened cable (the screen MUST be attached to the Earth Terminal)
5.
Wire the electronic control board as per Page 3 for the motors and wire the mains into the
switching power supply located under the main board, following the L/N/E polarity on the
plug
6.
Power up the E124 Board (please note that the board will take 5-10 seconds to boot-up)
7.
Verify the status of the LED’s and Display are as per Page 3
8.
Depending on the installation, verify that the LED’s on the encoders correspond to those
described on Page 4
9.
Wire in an OP-A trigger as per Page 3, alternatively program a remote control as shown on
Page 11.
10.
Familiarise yourself with how to program the E124 control board as per Page 5
11.
Begin Basic Programming of the E124 on Page 5
a.
Check Rotation of the motors by using Function “n1” and “n2” for motor 1 and 2
respectively as shown on Page 7
b.
If using encoders, “EN” must be set to “y” and “bu” function should be followed as
shown on Page 7
c.
Verify that the Gates are in the closed position as detailed on Page 8
d.
Run Time Learning – “tL” function and follow procedure as detailed on Page 8
12.
Provide an opening command to verify that the system works correctly
13.
Adjust Operating Logic according to the customer requirement
14.
Connect Safety Devices to the system as deemed required by the Risk Assessment carried
out previously
a.
Wireless Safety Edges can be connected via the BUS 2easy connection if using the
FAAC XTR and XTS Wireless Receiver system, the “bu” function must also be re-
addressed as shown on Page 7
b.
If not using the FAAC XTR and XTS System, we would recommend that the
EasyBoard software be used and that IN4 and IN5 should be set to Safety Edge Input
as desired, this will ensure that the board responds as fast as possible
c.
Traditional Photocells can be wired and configured as per Page 3
d.
FAAC BUS 2easy Photocells can be wired and configured as per Page 4, the “bu”
function must also be re-addressed as shown on Page 7
e.
XGuard Laser Curtains would be configured as Traditional Photocells in 14.c
15.
Connect any additional activation commands as per Page 3
16.
If using either Safety Edges or Inherent Obstacle Detection as part of the Risk Assessment,
there are useful Functions that can be modified to assist in attaining compliance on Page 9
17.
If using XGuard Laser Curtains please test these in accordance with BS EN 12445/12453
18.
Hand over all relevant documentation to the end customer as required by the Technical File
and the Supply of Machinery (Safety) Regulations 2008
Содержание E124
Страница 1: ...E124 Quick Start Guide...
Страница 11: ...Page 10 Signalling Errors and Alarms...