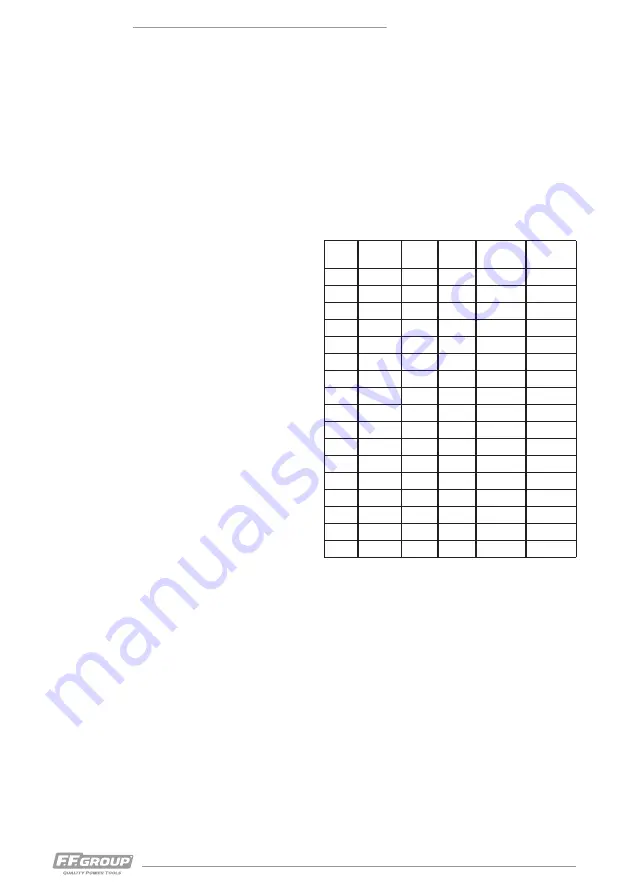
| English
12
Adjusting the spindle return spring (Fig. 16):
It may be necessary to adjust the spindle return
spring because its tension has changed and the
spindle moves back too quickly or too slowly. To
do so:
1.
Lower the table for more work space.
2. Work on the left side of the drill.
3.
Insert a screwdriver into the lower front groove
(1) and hold it.
4.
Remove the outer nut (3) with a wrench.
5.
With the screwdriver still in the nut, loosen the
inner nut (4) until the notch detaches from the
hub (6).
WARNING:
Spring is under tension.
6. Carefully turn the spring cap (2) counterclock-
wise with the screwdriver until you can press
the nut (1) into the hub (6).
7. Lower the spindle to the lowest position
and hold the spring cap (2) in position. When
the spindle moves up and down as you wish,
tighten the inner nut (4) again.
8. If it’s too loose, repeat steps 3-5. If it’s too
tight, reverse the step 6.
9. Secure the outer nut (3) against the inner
nut (4) with an open-ended wrench.
NOTE:
Do not tighten excessively and do not restrict the
movement of the spindle.
The axial operation of the spindle (Fig. 17):
When the spindle is in the lower position, turn it
by hand. If you find that the operation is too big,
proceed as follows:
1. Loosen the lock nut (19).
2. Turn the screw clockwise (20), to balance the
operation, without interfering with the up and
down movement of the spindle (a little opera
-
tion is normal).
3. Tighten the lock nut (19) again.
Positioning the work piece:
As a general rule, use a machine vice or another
suitable clamping device to secure a work piece in
position. Never hold the work piece in place with
your hand. When drilling, the work piece should
be able to travel on the drill table for self-center
-
ing purposes. Ensure that the work piece cannot
rotate. This is best achieved by placing the work
piece /machine vice on a sturdy block.
NOTE:
Sheet metal parts must be clamped in to prevent
them from being torn up. Properly set the height and
angle of the drill table for each work piece. There
must be enough distance between the upper edge
of the work piece and the tip of the drill bit.
NOTE:
Place a piece of backup material (e.g. wood) on the
table underneath the work piece. This will prevent
splitting or making a heavy burr on the underside of
the work pieces as the drill bit breaks through.
WARNING:
To keep the backup material from spinning out of
control it must contact the left side of the column
as illustrated. If the work piece or the backup mate
-
rial is not long enough to reach the column, clamp
them to the table. Failure to do this could result in
personal injury.
NOTE:
For small pieces that cannot be clamped to the ta
-
ble, use a drill press vise (optional accessory). The
vice must be clamped or bolted to the table to avoid
injury from spinning or breakage.
Choosing speed:
Ensure that you drill at the proper speed. Drill
speed is dependent on the diameter of the drill
bit and the material in question.
The table below acts as a guide for selecting the
proper speed for various materials:
Drill
bit ø
Cast
iron
Steel
Iron
Alu
minium
Bronze
3
2.550
1.600 2.230
9.500
8.000
4
1.900
1.200 1.680
7.200
6.000
5
1.530
955
1.340
5.700
4800
6
1.270
800
1.100
4.800
4.000
7
1.090
680
960
4.100
3.400
8
960
600
840
3.600
3.000
9
850
530
740
3.200
2.650
10
765
480
670
2.860
2.400
11
700
435
610
2.600
2.170
12
640
400
560
2.400
2.000
13
590
370
515
2.200
1.840
14
545
340
480
2.000
1.700
16
480
300
420
1.800
1.500
18
425
265
370
1.600
1.300
20
380
240
335
1.400
1.200
22
350
220
305
1.300
1.100
25
305
190
270
1.150
950
NOTE:
The drill speeds specified above are merely suggest
-
ed values.
Countersinking and center-drilling:
With this table drill, you can also countersink and
center-drill. Please observe that countersinking
should be performed at the lowest speed, while a
high speed is required for center-drilling.
MAINTENANCE AND CLEANING
WARNING:
For your own safety, turn the switch off and remove
plug from power source outlet before any operation
of maintenance on the drill press.
Keep your appliance clean. To avoid motor damage,
blow out or vacuum frequently this motor to keep
drill press dust from interfering with normal motor
ventilation.
DPB 16/12 PLUS | DPF 16/12 PLUS
Содержание DPB 16 PLUS
Страница 4: ...4 4 3 12 2 7 8 6 10 9 11 9 10 6 10 9 11 11 12 DPB 16 12 PLUS DPF 16 12 PLUS...
Страница 27: ...27 www ffgroup tools com f f f f f f DPB 16 12 PLUS DPF 16 12 PLUS...
Страница 28: ...28 1 5 mm2 f DPB 16 12 PLUS DPF 16 12 PLUS...
Страница 33: ...33 www ffgroup tools com 1 2 3 4 5 1 2 3 DPB 16 12 PLUS DPF 16 12 PLUS...
Страница 53: ...53 www ffgroup tools com DPB 16 12 PLUS DPF 16 12 PLUS...