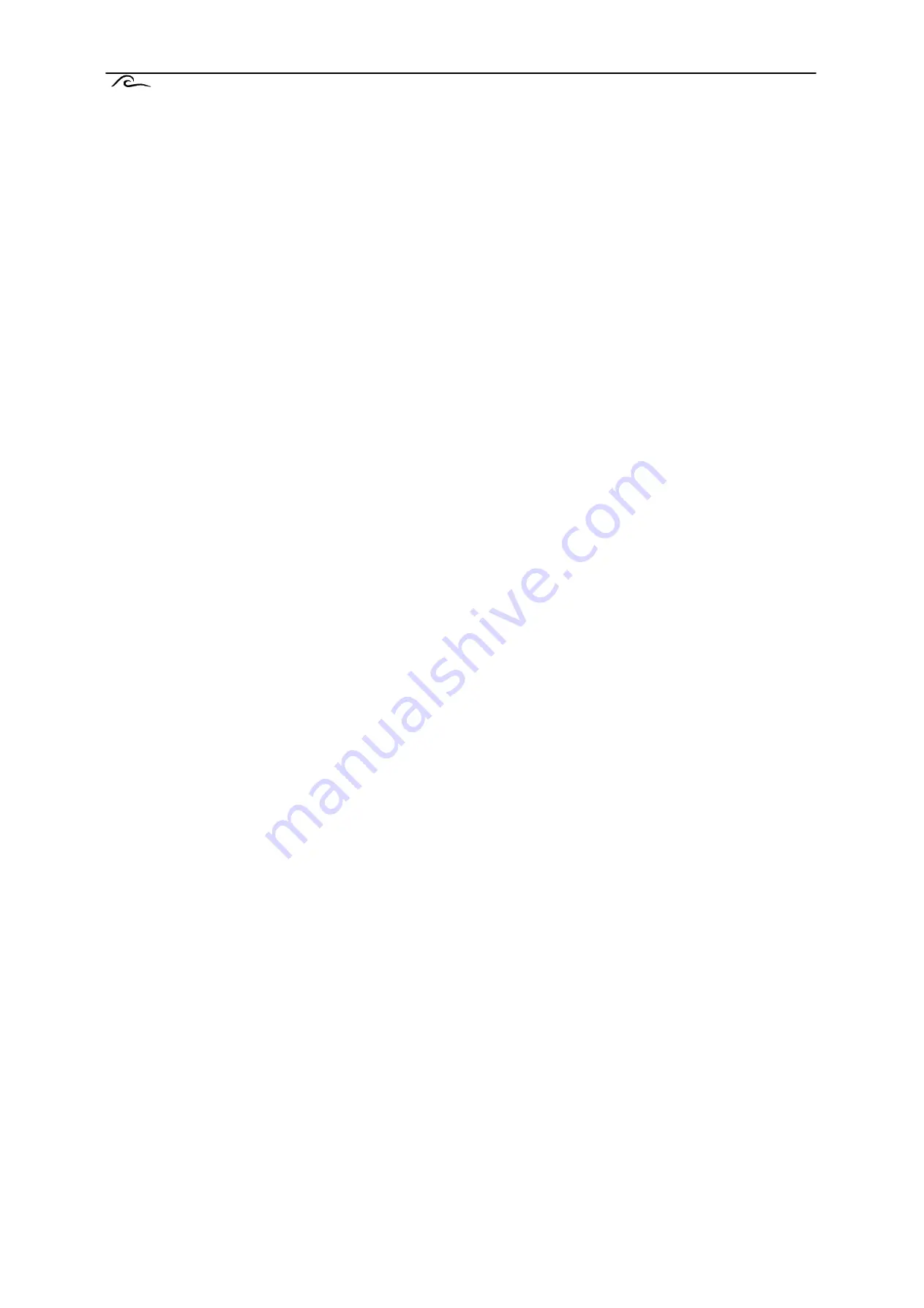
OS3030
Input functions
16
Input functions
The "FULL" and "EMPTY" inputs are standard features. Define whether the inputs are activated are
activated when the contact is open or closed. This is defined in programming step 4.4.
Optionally, the controller can be equipped with a motor circuit-breaker for 1-phase high-pressure
pumps. The break contact and a motor circuit-breaker alarm contact, if included, are connected inter-
nally on the PCB.
The "external switch" function must be used for the alarm contact for an external motor circuit-breaker.
FULL and EMPTY
The level switch connections for automatically
refilling a reservoir are marked "FU" (FULL)
and "EM" (EMPTY).
If both alarm signals are activated, "FULL" has
greater priority.
A reservoir can only be refilled via the (FULL)
level switch. The (EMPTY) level switch is then
used to signal that the reservoir has run dry.
Alternatively, the reservoir can be refilled via
both level switches, ("FULL", "EMPTY") or
manually. (See programming step 5.1)
The response time for the inputs is 4 seconds.
The "FULL" and "EMPTY" alarm signals can
be connected to the alarm relay or to the
buzzer.
The "FULL" and "EMPTY" alarm signals are
shown in the LCD whenever the alarm relay or
horn are activated, or if the inputs have only
been programmed to act as full and empty
alarm signals.
Motor circuit-breaker
The alarm contact for the motor circuit-breaker
is active when the contact is made.
The response time is 2 second.
The motor circuit-breaker alarm signal can be
connected to the alarm relay or to the buzzer.
The motor circuit-breaker alarm signal is dis-
played in the LCD.
WARNING! The motor circuit-breaker has to
be released following a fault alarm. The system
is switched
back on manually by pressing
"ON".
There are another two inputs (or three with the IF plug-in card) (IN1, IN2 and IN3) available for the
system controller. These can be assigned the following functions, in accordance with the programming
sequences in programming steps 4.1 - 4.3. In programming step 4.4, specify whether the functions are
to be activated when the contact is made or broken.
STOP input
In programming step 5.13, specify the phases
in which the ATOP input is scanned.
If the input is active, the outputs are connected
to the positions programmed in the relevant
programming steps, i.e. 10.1,10.2 and 17.1.
Furthermore, in programming step 5.14, you
can specify whether the system should resume
operation once the stop signal has been dis-
abled or has to be restarted manually.
The stop function is used, for example, to
switch off the osmosis plant during the regen-
eration of an upstream softening plant.
The system can be switched back on by press-
ing "ON", even while the stop signal is active.
The stop signal is ignored until the next deacti-
vation sequence.
The response time for the input is 6 seconds.
The "STOP" alarm signal can be connected to
the alarm relay or to the buzzer.
The "STOP" phase is displayed in the LCD.