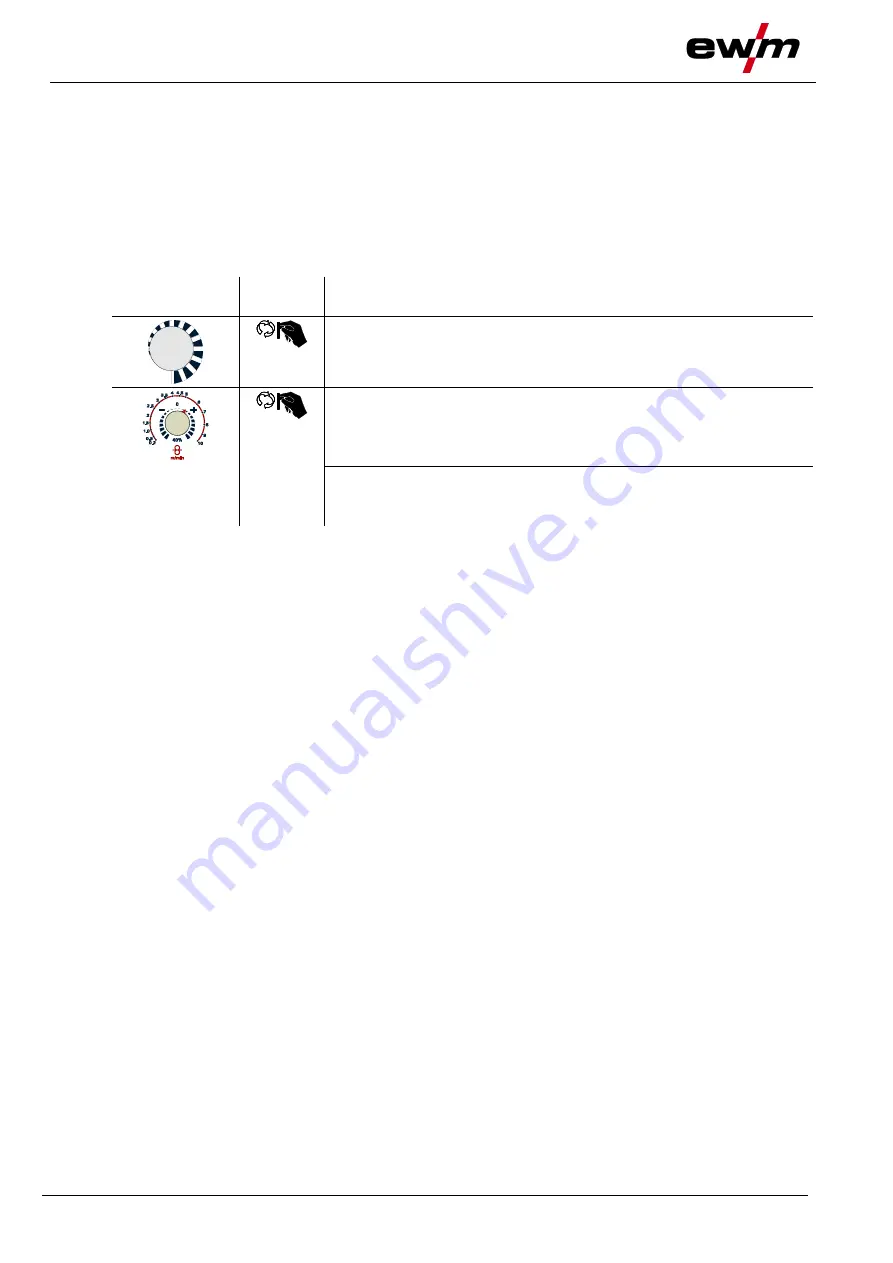
Functional characteristics
Filler wire welding
54
099-00T401-EW501
01.02.2022
5.3.3 Select wire speed operating mode (KORREKTUR / MANUELL)
The wire speed can be set in two different operating modes:
MANUAL:
The wire speed can be selected on the wire feed unit as an absolute value across the
entire setting range.
CORRETION: The wire speed is approximately specified by the welding machine control and can be
corrected as a percentage on the wire feed unit
In the wire feed unit underneath the cap is a switch for selecting the operating mode.
5.3.4 Setting the welding current and wire speed
Operating ele-
ment
Action
Result
Set welding current on the welding machine
Set wire speed
MANUAL operating mode (outer scale):
The wire speed can be selected on the wire feed unit as an absolute
value across the entire setting range.
CORRECTION operating mode (inner scale):
The wire speed is specified largely by the welding machine control and
can be corrected as a percentage on the wire feed unit