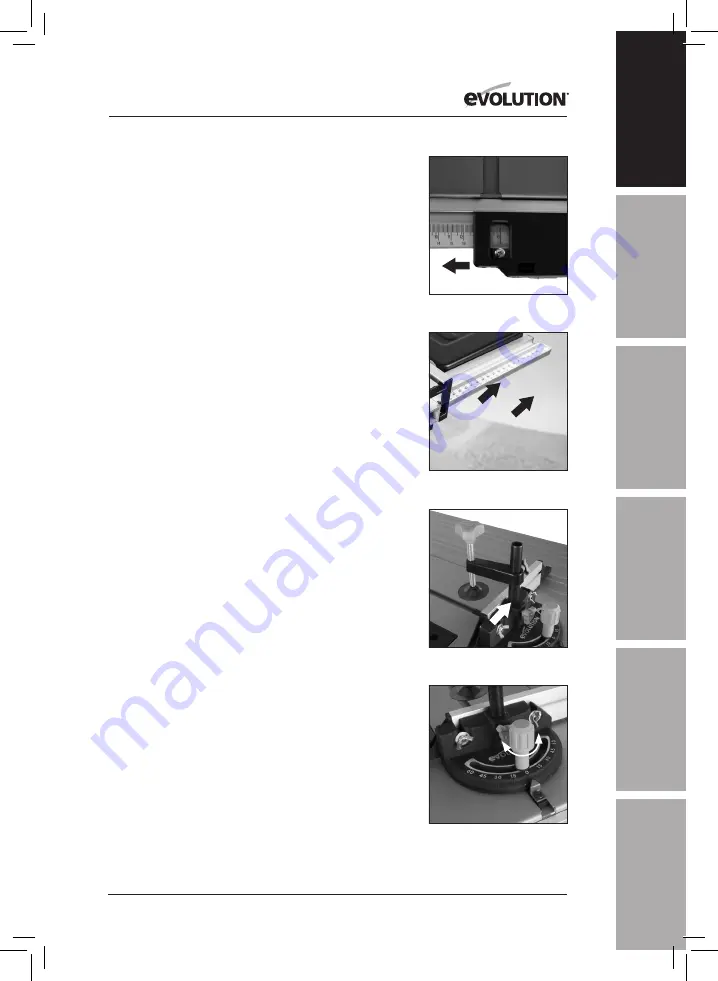
19
www.evolutionpowertools.com
EN
ES
DE
FR
IT
NL
• Loosen slightly the seven coach bolts
(P)
which hold the
fence rail to the machine.
• Gently move the fence rail to the right or left until the ‘0’
position on the scale coincides with the datum line in the
magnifier.
(Fig. 13)
• Check, and when satisfied that calibration has been
achieved, tighten the seven fence rail nuts securely.
• Lower the blade.
Note:
The rip fence simply slots into the fence rail, and can be
locked into position anywhere along the rails length, and at either
side of the machine by pressing the locking lever downwards.
CHECKING/ADJUSTING THE RIP FENCE
When the fence rail and rip fence have been attached to the
machine, the rip fence should be checked to ensure that it lies
parallel to the blade.
• Raise the blade to its full height.
• Rest a straight-edge or similar against the blade.
• Bring the rip fence up to the straight-edge and check
for parallelism.
• If adjustment is needed, gain access to the two socket
headed screws through the two holes in the carrier.
(Fig. 14)
• Loosen these screws using the correct sized hex key,
and adjust the fence as required.
• Tighten and re-check the rip fence when correct alignment
has been achieved.
• Lower the blade.
SLIDING MITRE GAUGE
Note:
The sliding mitre gauge
(K)
fits in either of the inverted
‘T’ slots in the machine table.
The adjustable aluminium faceplate is held in the protractor base
of the mitre gauge by two machine screws and thumb nuts.
The anti-bounce device
(I)
can be fitted into the socket
incorporated into the mitre gauge base.
(Fig. 15)
Turning the
locking handle anti-clockwise
(Fig. 16)
allows the mitre gauge
angle to be adjusted. Use the protractor scale and pointer and
set the gauge to the desired angle. Tighten the vertical handle
when the required angle has been selected.
Note:
It is recommended that the anti-bounce device is fitted
only when needed (e.g. when cutting thin sheet material or
Fig. 13
Fig. 15
Fig. 14
Fig. 16