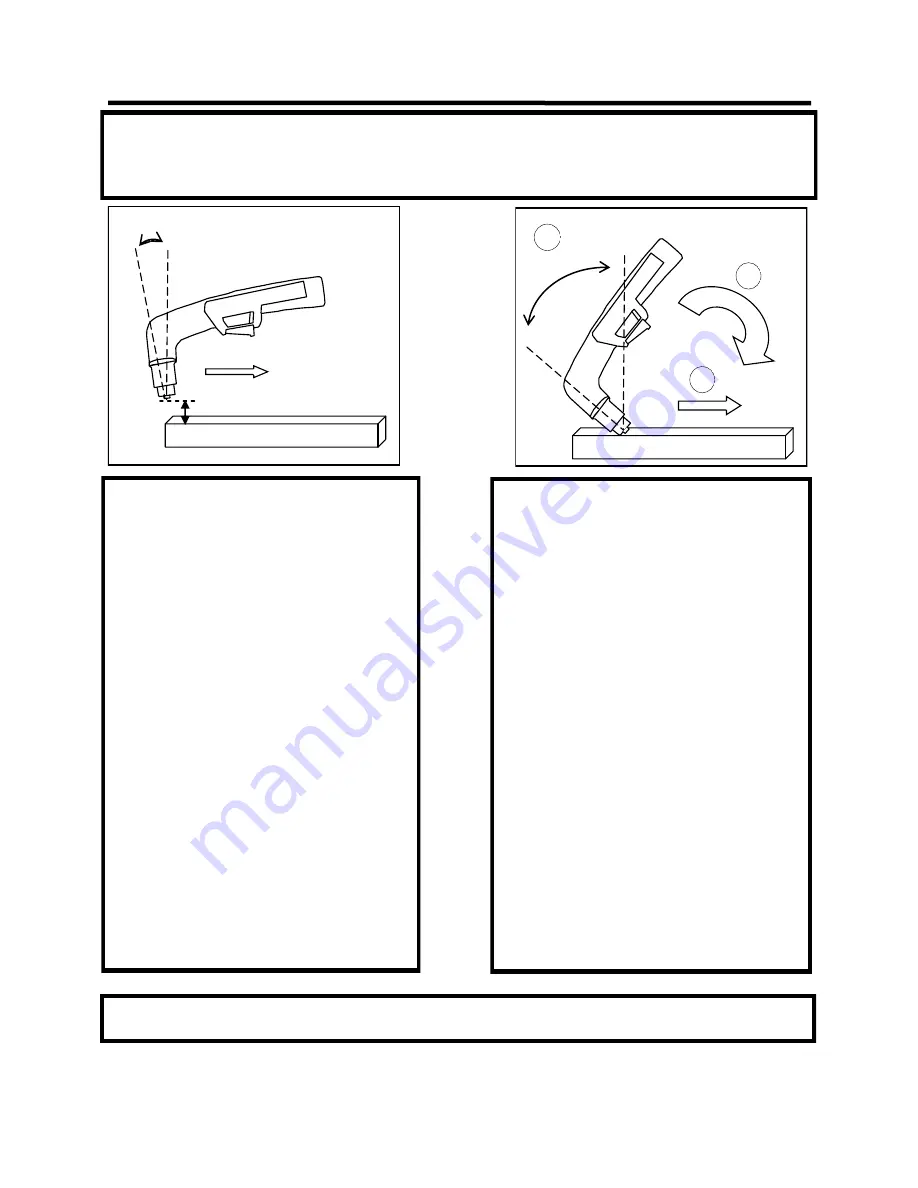
19
Edge Starts are the best type of start if possible
to promote consumable and torch life. This re-
duces blow back of molten material and allows a
smooth gradual start of the cut.
1. Line up the hole on the tip of the electrode
on the edge of the cut. Hold torch perpen-
dicular to the cut initially, about 1/16” off
the metal. Slide the yellow safety lock and
squeeze the trigger. Wait for arc to start.
2. Once the arc starts, wait for the arc to pene-
trate all the way through the metal.
3. As the torch penetrates its flame all the way
through the metal, tilt the torch so there is a
slight lead in the flame if metal is thin. If it is
thick, keep holding torch in a nearly vertical
position.
4. Begin moving the torch in the direction of
the cut. Maintain 1/16” standoff height.
5. Move the torch fast enough so the sparks
and flame trail from the bottom edge at an
angle of no more than 30° and no less than
10° from perpendicular to the metal. Excess
angle of sparks/flameindicate too fast of
travel speed or practical cut capacity has
been reached. Little or no angle indicates
too slow of travel speed.
IMPORTANT: If you use a standoff guide with the torch, it must be adjusted or bent to provide no more than 1/8” standoff, less if possible.
Long standoff heights reduce cut capacity and quality. It also promotes rapid consumable wear and can prevent the pilot arc from transferring.
Basic theory and function
Section 3
0°-15°
TRAVEL
1/16”
EDGE START
40°-60°
TRAVEL
1
PIERCE START
2
3
Piercing starts often result in rapid consumable
wear and excess blow back of molten metal de-
posited onto torch and consumables. This
should be done only as necessary.
1. Tilt the torch in the direction of travel or
toward the side of the metal to be discarded
or wasted at a 40° to 60° angle. Slide the yel-
low safety lock and squeeze the trigger. Wait
for arc to start.
2. Once the arc starts, wait for the arc to trans-
fer from pilot arc to the cutting arc.
3. As the torch penetrates it flame at an angle
rotate the torch slowly to the vertical posi-
tion, as the arc penetrates the metal. Tilt the
torch from 0°-15° for thin metal cuts, or hold
it nearly perpendicular for thicker metal cuts.
4. Begin moving the torch in the direction of the
cut. Maintain 1/16” standoff height.
5. Move the torch fast enough so the sparks
and flame trail from the bottom edge at an
angle of no more than 30° and no less than
10° from perpendicular to the metal. Excess
angle of sparks/flame indicate too fast of
travel speed or practical cut capaicity has
been reached. Little or no angle indicates
too slow of travel speed.
The design of the blow back start
may
cause a slight delay in the arc as the air pressure must built inside the torch
tubing and head to create the pressure needed to force the electrode off the nozzle seat. This may take up to two
seconds. Restarting the arc with the post flow going may not cause a delay. If the torch does not light after 3 sec-
onds, let go of the trigger and press it again. If start/arc is erratic check nozzle and electrode for tightness and wear.