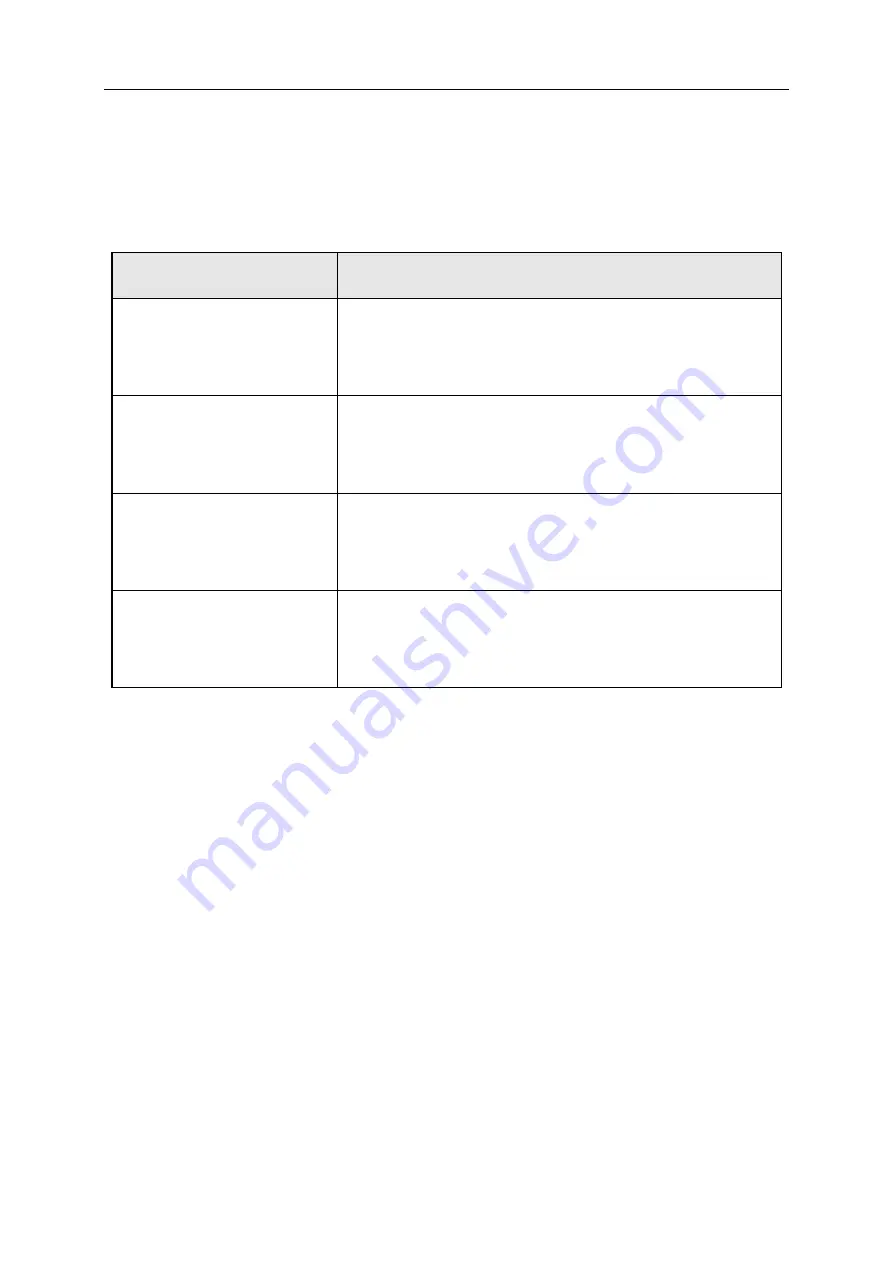
www.euroboor.com
27
6. Troubleshooting
Problem
Possible cause
Motor does not work
- Damaged or defective wiring
- Motor internals worn-out or damaged
- Defective switch
- Defective control unit
Frame under voltage
- Damaged / defective wiring
- Machine highly contaminated / dirty
Overheating
- Blocked motor housing vents
Tool does not grind or brush
effectively
- Accessory may be damaged, worn or wrong type for the
material.