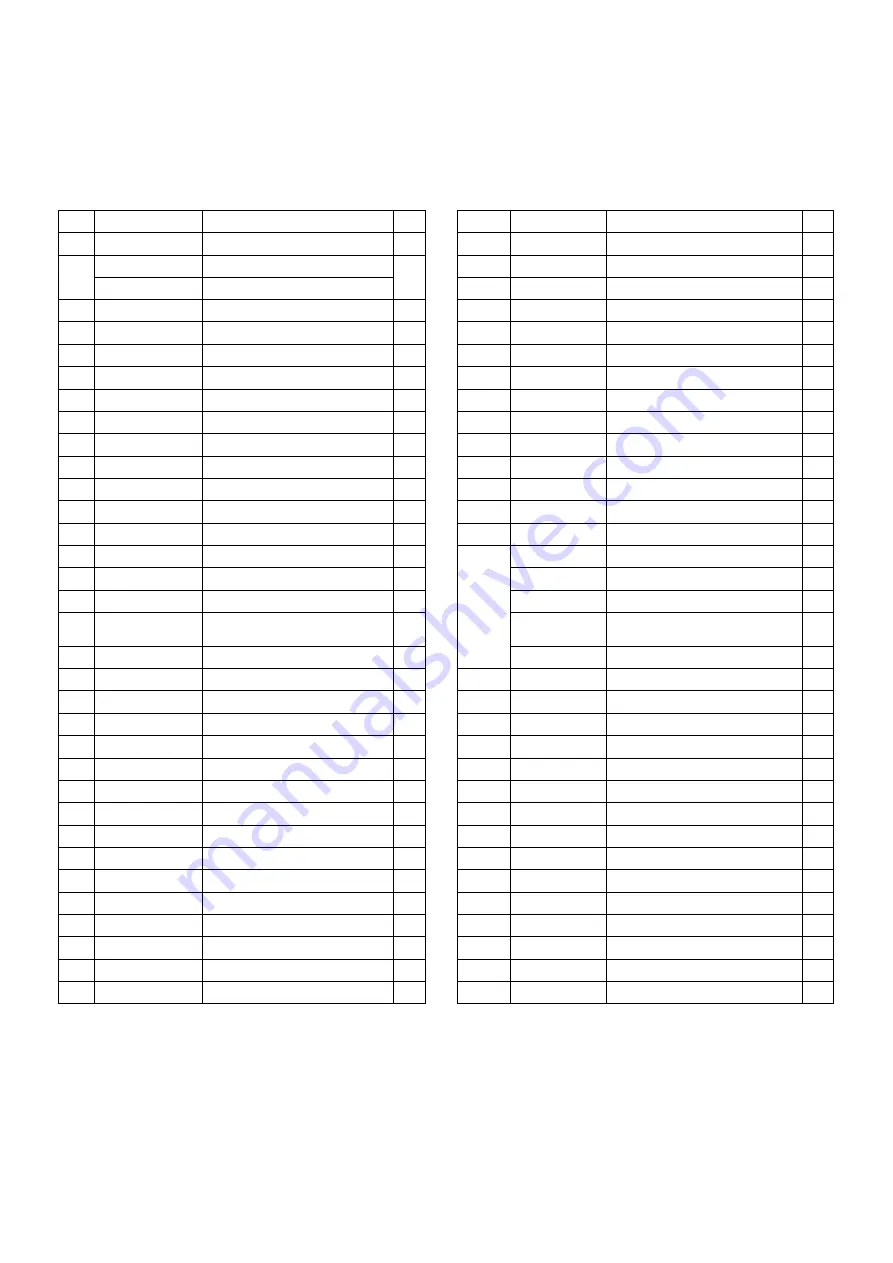
43
8.2 Spare part lists
B60
No. Part number
Description
Qty
No.
Part number
Description
Qty
1
B60.0022
Protective handle
2
34
B60.1006
Guide plate assembly:
1
2
030E.0091/Y2
On / off switch 220V
1
34A
B60.0037
Left semicircle slider
1
030E.0092/Y2
On / off switch 110V
34B
B60.0038
Right semicircle slider
1
3
B60.0018A
Green signal light
1
34C
B60.0039
Lower plate
1
4
B60.0016
Inner six angle bolt
4
34D
B60.0040
Upper plate
1
5
020.0217
Spring washer
4
34E
020.0223
Screw
8
6
B60.1008B
Electrical box assembly
1
35
B60.0041
Screw M10
2
7
020.0101
Panel screw BKVZ M4 x 8
4
36
B60.0030
Elastic washer
2
8
B60.0035
Cylindrical pin φ5
2
37
B60.0042
Flat washer M10
4
9
B60.0066
Capacitance
1
38
B60.0044
Steel sleeve
2
10
B60.0067
Capacitor holder
1
39
B60.0043
Contact roller
4
11
B60.0068
Screw M5 x 8
2
40
B60.0045
T-Nut
2
12
B60.0007B
Cooling plate
1
41-43
020.0037
Cable clamp complete
1
13
B60.0004
Rubber isolator
4
44
020.0031
Coupling nut PG11 (main cable)
1
14
020.0329
Screw M4 x 16
4
45
020.0036
Main cable complete 220-240V
1
15
B60.0008
Rubber cord protector
1
020.0036/AU
Main cable Australia
16
B60.0054
Motor cable end cover
1
020.0036/UK
Main cable UK 220V
17
B60.1001B
Motor assembly
1
020.0036/UK
110-16A
Main cable UK 110V 16A
18
B60.0002
Key
1
020.0036/USA
Main Cable USA
19
B60.0026
Cutter head connecting sleeve
1
46
B60.0062
Inner hex bolt
2
20
B60.0027
Cutter body
1
47
B60.1003
Frame
1
21
LKS.15
Cutting plate
10
48
B60.1004
Handle bar U-shaped
1
22
B60.0029
Screw
10
49
B60.0063
Inner hex bolt
2
23
B60.0030
Elastic washer
1
50
B60.0014
Duckbill gasket
4
24
B60.0031
Screw
1
100
CAS.B60
Metal case
1
25
B60.0032
Adjusting knob
1
101
SAF.100
Safety goggles
1
26
B60.1009
Cutter head cover with Logo tag
1
102
SAF.300
Protective gloves
1
27
B60.0034
Pointer plate
1
103
SAF.200
Ear plugs
1
28
020.0305
Washer M8
5
104
B60.0049
Spanner Torx T20
1
29
100.0031
Spring washer
5
105
IMB.US4
Allen key 4.0 mm
1
30
B60.0036
Adjustable handle
1
106
IMB.US6
Allen key 6.0 mm
1
31
B60.0046
Screw
2
107
IMB.US8
Allen key 8.0 mm
1
32
B60.0056
Spring washer
2
109
B60.0050
Open spanner 18mm
1
33
B60.0055
Leveling pad
2
110
B60.0051
Open spanner 32mm
1
Содержание B60
Страница 2: ...2 ...
Страница 4: ...4 ...
Страница 11: ...11 B60 B60S B60S shown image 1 1 image 1 2 ...
Страница 12: ...12 B60 image 1 3 B60S image 1 4 ...
Страница 20: ...20 image 2 3 ...
Страница 39: ...39 8 Exploded view spare part list 8 1 Exploded views B60 ...
Страница 40: ...40 B60 CONTINUED ...
Страница 41: ...41 B60S ...
Страница 42: ...42 B60S continued ...
Страница 45: ...45 8 3 Wiring diagrams B60 ...
Страница 46: ...46 B60S ...
Страница 48: ...48 ...