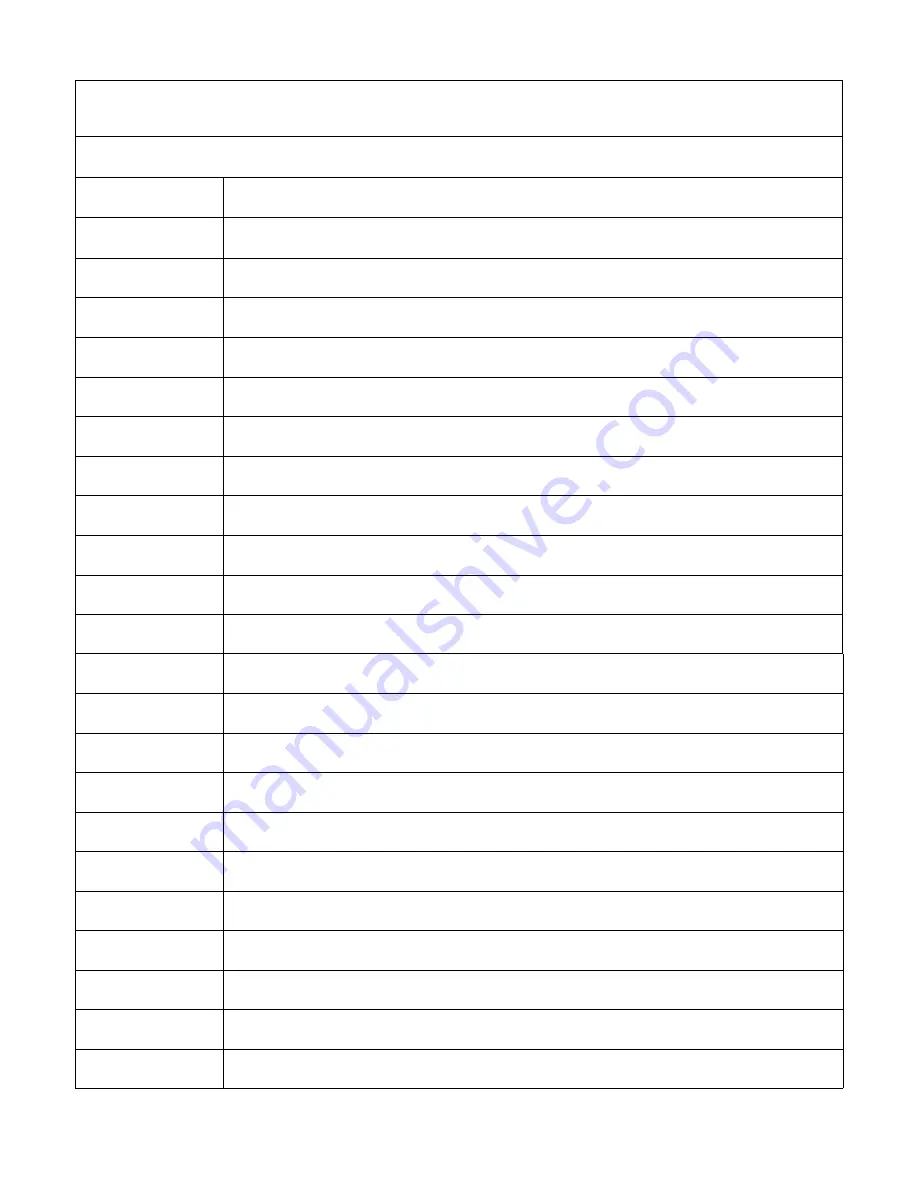
HYDRAULIC SCHEME
A
Hydraulic pump
P/N 680427
B
Tank
P/N 130458
C
Oil filter- complete
P/N 490641
D
Hydraulic control valves
P/N 680018
E
Hopper gate cylinder
P/N 680017
F
Hopper lift cylinder
P/N 680016
G
Max pressure valve (60 bar)
P/N 110996
H
Flow control valve
P/N 680324
L
Power steering pump
P/N 680421
M1
M2
Hydraulic pressure check point
P/N 680132
N
Return oil collector
P/N 210694
O
Max pressure valve (15 bar)
P/N 680019
S
Capacity control nipple
P/n 210381
1
Hose TH1SN06 3/8" 180 bar
P/N 680010
2
Hose EVERGREEN / 1SN 3/8" 180 BAR
P/N 680426
3
Hose TT2TE06 3/8" 63 BAR
P/N 680423
4
Hose TT2TE06 3/8" 63 BAR
P/N 680007
5
Hose TT2TE06 3/8" 63 BAR
P/N 680424
6
Hose TT2TE06 3/8" 63 BAR
P/N 680110
7
Hose TH2SC04 1/4" 400 BAR
P/N 680003
8
Hose TH2SC06 3/8" 330 BAR
P/N 680004
9
Hose TH2SC04 1/4" 400 BAR
P/N 680009
10
Hose TT2TE06 3/8" 63 BAR
P/N 680238
11
Hose TT2TE06 3/8" 63 BAR
P/N 680425
41
Содержание MAGNUM 901 EB EVOLUTION
Страница 2: ......
Страница 13: ...13 ...
Страница 14: ...MACHINE DESCRIPTION 1 3 2 4 8 9 10 16 15 14 13 12 11 7 25 20 19 21 22 23 17 18 24 26 5 6 ...
Страница 35: ...TECHNICAL DIMENSION DRAWINGS 35 ...
Страница 38: ...HYDRAULIC SCHEME ...
Страница 40: ...HYDRAULIC SCHEME ...
Страница 58: ...58 ...
Страница 62: ......