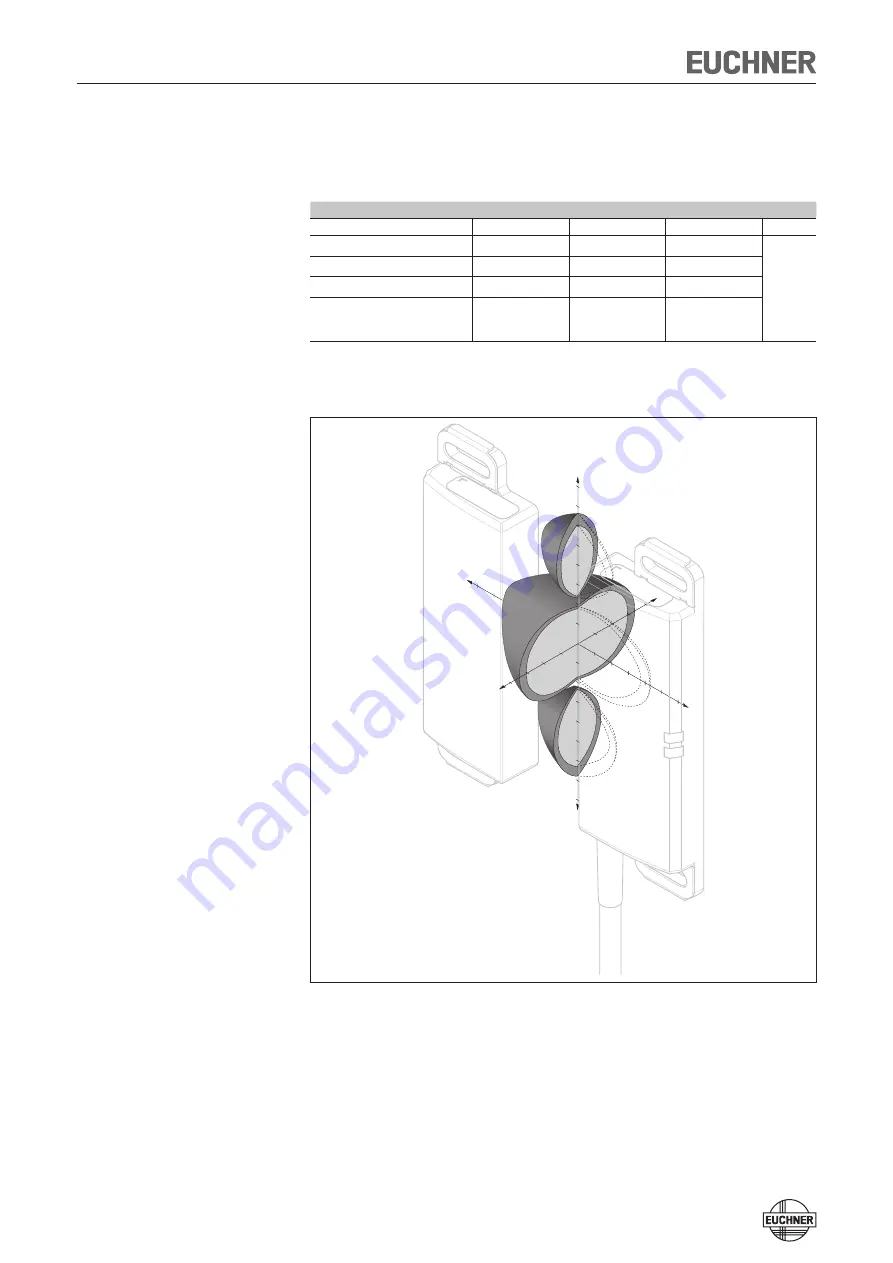
System Manual Safety Switch CES-AP-C.2-CH
19
Switching distances
Operating distance for center offset m = 0
(only in combination with actuator CES-A-BLN-...)
Parameter
Value
Unit
min.
typ.
max.
Switch-on distance
-
15
-
mm
Assured switch-on distance s
ao
1)
10
-
-
Switching hysteresis
1)
1
-
Assured switch-off distance s
ar
- in x/z direction
- in y direction
-
-
-
-
40
60
Typical operating distance
(only in combination with actuator CES-A-BLN-...)
Figure 5: Typical operating distance
For a side approach direction for the actuator and safety switch, a minimum distance of s = 6 mm
must be maintained so that the operating distance of the side lobes is not entered.
Z
-25
-30
X
10
5
15
20
-20
-25
-30
-40
-35
-15
-10
-5
-10
20
25
30
15
10
40
35
5
Y
15
20
25
5
-5
-15
30
10
-20