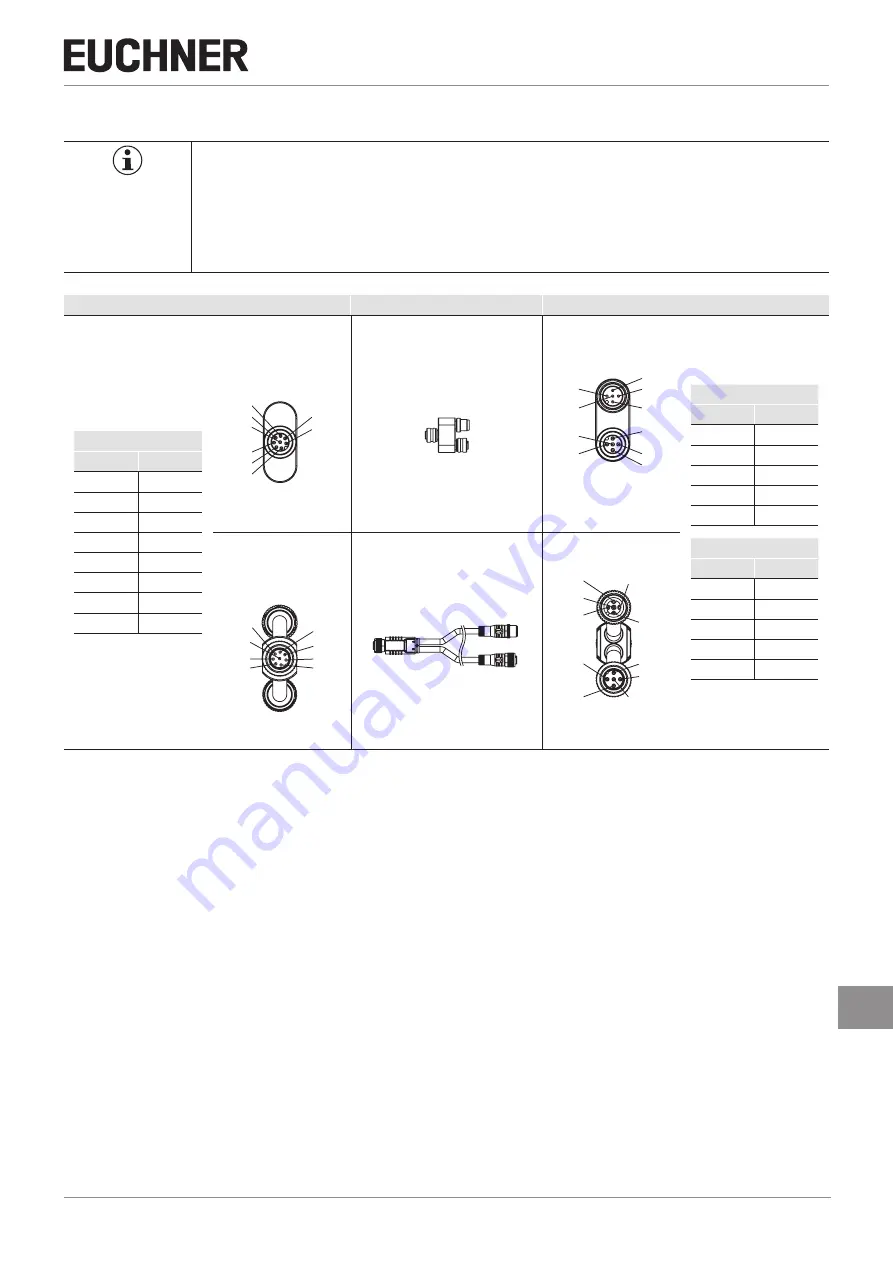
21
MAN20001574-01-09/22 (translation of the original operating instructions)
Operating Instructions
Transponder-Coded Safety Switch CTM-C2-BP/BR-FLX
EN
11.2.3. Connector assignment of Y-distributor for series connection without IO-Link communication
Important!
Ì
The switch chain must always be terminated with strapping plug 097645.
Ì
All guard locking solenoids are always controlled simultaneously on the use of these Y-distributors
in a series connection.
Ì
A higher-level control system cannot detect which safety door is open or on which switch a fault has
occurred with this connection technology.
Plug connector X1
Y-distributor
Plug connector X2 / X3
X1
Pin
Function
X1.1
FI1B
X1.2
UB
X1.3
FO1A
X1.4
FO1B
X1.5
n.c.
X1.6
FI1A
X1.7
0VUB
X1.8
*
X1
Socket
6
5
8
4
3
2
7
1
097627
X1
X2
X3
X2
Plug
1
1
5
5
4
4
3
3
2
2
X3
Socket
X2
Pin
Function
X2.1
UB
X2.2
FO1A
X2.3
0 V
X2.4
FO1B
X2.5
*
X3
Pin
Function
X3.1
UB
X3.2
FI1A
X3.3
0 V
X3.4
FI1B
X3.5
*
X1
Socket
5
8
4
3
6
7
1
2
111696
112395
X1
X2
X3
With connecting cable
X2
Plug
5
1
4
3
2
5
1
4
3
2
X3
Socket
* Function and compatibility are dependent on the pin assignment of the device connected.