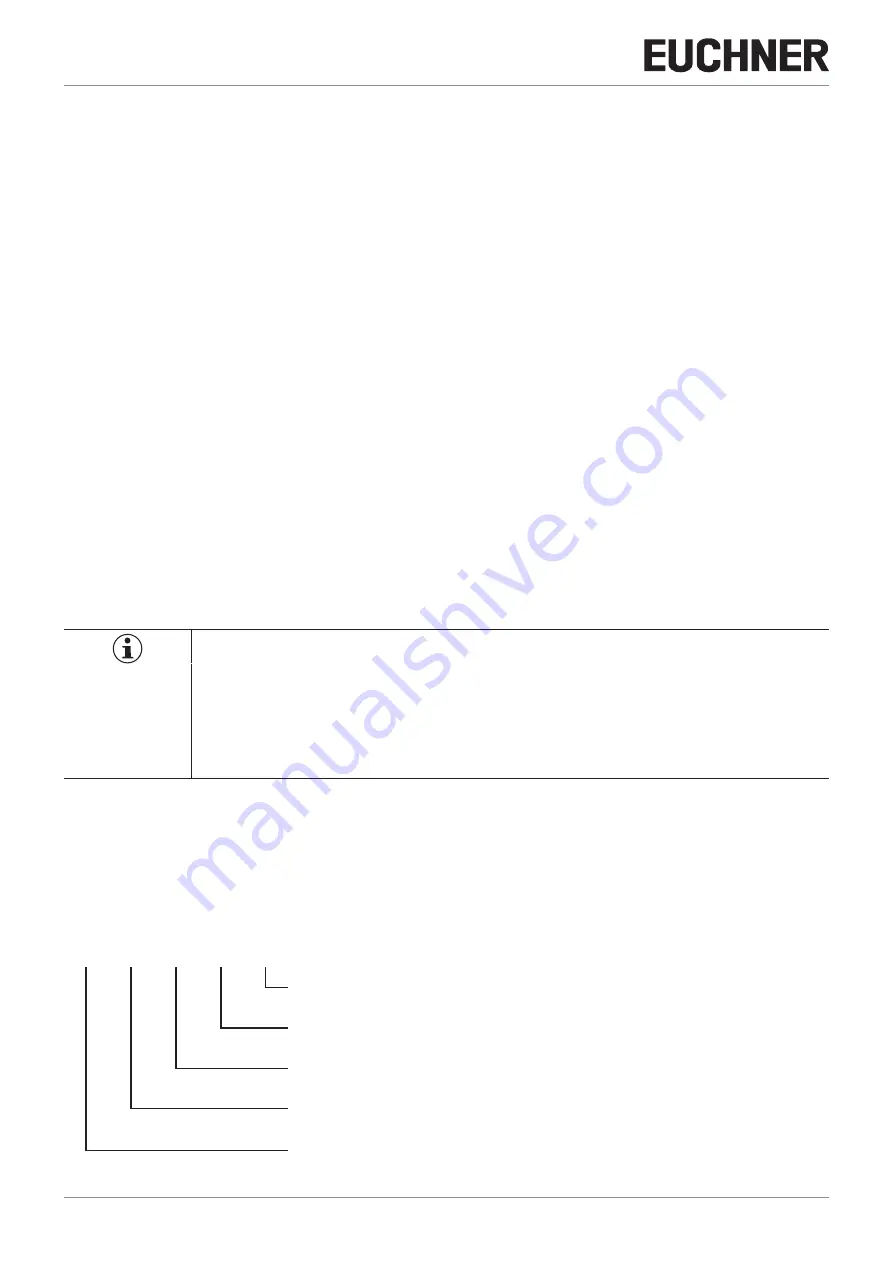
Operating Instructions Bus Module
MBM-EC-..-MLI-… (EtherCAT)
22
(translation of the original operating instructions) 2540772-01-11/21
11. Setup
A typical MLI system usually consists of several modules and submodules. If the topology was not saved yet, the bus module
MBM will determine the modules and submodules concerned on system startup.
To suit this configuration, in the configuration software for your control system you must assemble the related data blocks
for the communication data for the individual modules and submodules and, if necessary, set parameters. The individual
modules and submodules are already included in the ESI file and must be adopted in the planning software (e.g. TwinCAT 3
from Beckhoff) to suit your system layout. You will find an overview of the communication data in chapter
.
You will find an overview of the parameters that can be set for modules/submodules in chapter
parameters for modules and submodules on page 29
Some data blocks are permanently linked to the related module or submodule; you can add others optionally (see chapter
11.4. System layout and layout of the data areas in the control system
You can find which data blocks your modules or submodules contain on the data sheet that is enclosed with every device
(see chapter
11.3. Information on the related data sheets
11.4. System layout and layout of the data areas in the control system on page 24
communication data for a system are assembled.
From chapter
11.7. Integrating in EtherCAT and FSoE on page 27
, it is explained how you configure and set the param-
eters for the individual modules and submodules in the configuration software for your control system.
11.1. Teach-in operation
The modules and submodules must be assigned to each other using a teach-in function before the system forms a functional
unit.
During the teach-in operation, the module is in the safe state (all safe bits are not set).
Important!
Ì
A system that has not yet been taught-in remains in the teach-in standby state until all modules
have been taught-in during a power-up process. Systems that have already been taught-in must be
reset to the factory setting in order to restore the teach-in standby state.
Ì
A faulty module or submodule can be replaced with an identical module or submodule without a
teach-in operation. If several modules or submodules have to be replaced, a power-up must be
performed after each device is replaced.
11.2. Overview of the communication data
A data sheet with the associated input and output bits belongs to each module/submodule (see chapter
). The identifiers for the bits always have the same structure (see below).
The following example shows an error status bit [E] in a submodule [SM] for the switch position S1 [S1].
SM
_
E
_
S1
[1]
[2]
[3]
_
[4]
Designation of the related controls/indicators
Separator
Type of information (input bit, output bit, message, error, etc.)
Placeholder to identify the related module/submodule (first, second, etc., module in
the line or submodule in slot 1 or 2)
Type of related module/submodule (SM= submodule, LM= locking module, etc.)