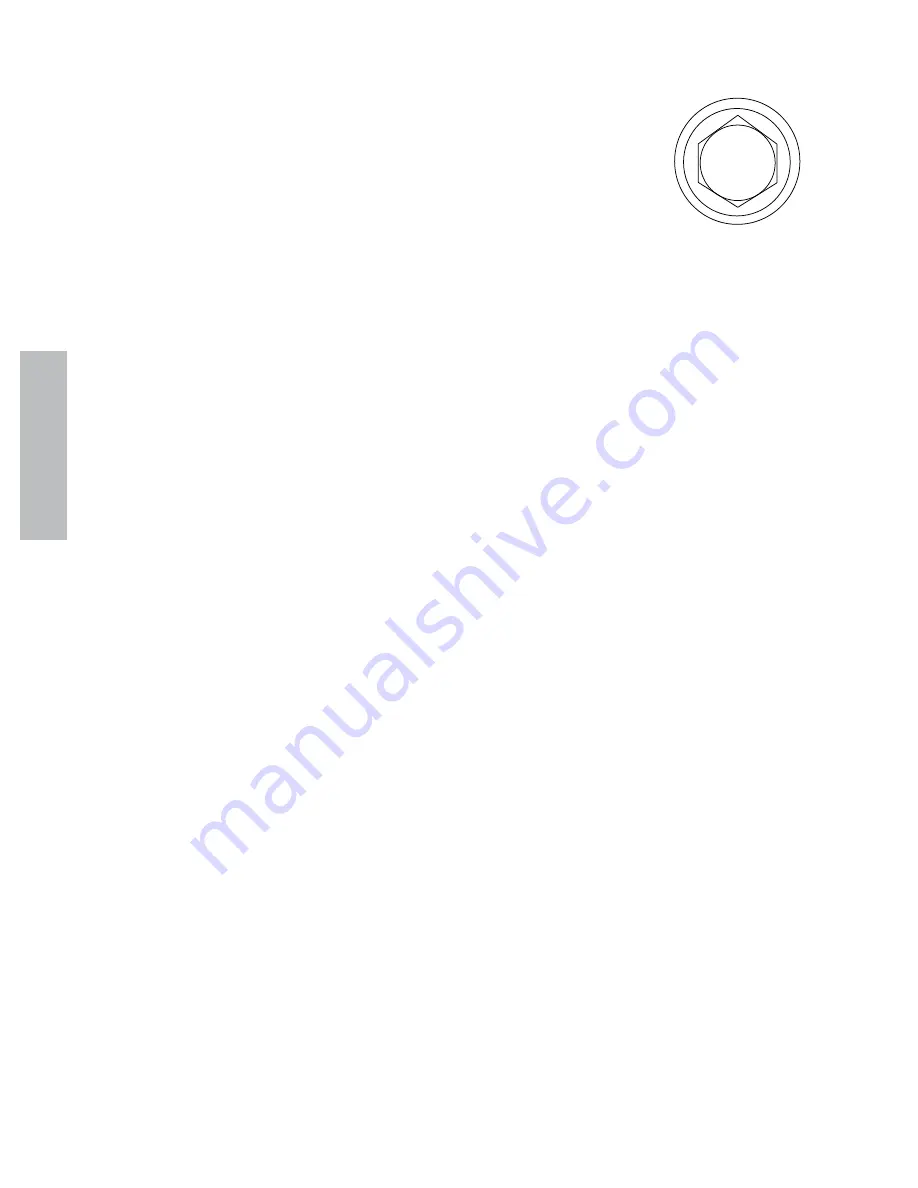
22
MAINTENANCE
Air Pressure & Brake Protection Valve
This air-ride suspension is dependent on air pres-
sure from the trailer supply system. Air pressure must
be maintained above 65 P.S.I. before operation. A Brake
Protection Valve must be installed in the air system to
prevent air loss below 65 P.S.I. and to insure safe air
brake pressure in the event of air loss in the suspension
system.
Operational Inspection
1. Inspect all welds at hanger-to-frame connections.
2. Inspect for proper installation of cross member
between hangers. Hangers should be adequately sup-
ported to prevent side movement.
3. Inspect axle to lower beam weld. Axle should
be snug in contoured axle seat and welded according to
guidelines shown in Figures 16, 17 and 18.
4. Inspect axle alignment to kingpin. Forward axle
should be + 1/16" left to right relative to kingpin. Rear
axle, if equipped, should be in line with forward axle +
1/16" axle center to axle center. Refer to axle align-
ment procedure shown in Figure 19.
5. Inspect automatic air control valve for proper
installation. Valve should be mounted so linkage is free
to operate without interference. Check all linkage con-
nections and air fittings on valve for tightness. Refer to
Figure 20.
6. Inspect air spring. With unloaded trailer on level
surface and supply air pressure in excess of 65 P.S.I.,
all air springs should be of equal pressure. Check for
proper clearance around air spring: minimum 1-3/4".
7. Inspect for proper mounting height. If measure-
ment is incorrect, adjust height control valve until proper
mounting height is achieved.
8. Check all air connections for leaks and tighten
if needed.
9. Inspect air lines. They should be free from sharp
objects and secured to prevent premature failure.
10. Eccentric bolt inspection: (See Figure 15)
Figure 15. Eccentric Bolt Inspection
Preventive Maintenance
Daily
Visually inspect trailer to be sure it is level and that
suspension ride height is correct.
Check for loose or broken parts on or around sus-
pension to prevent any serious problems from occur-
ring.
Every 30 Days
Check clearances around all moving suspension
parts, air springs, tires and shock absorbers. Any signs
of interference should be immediately corrected.
Visually inspect axle connection weld and bolt con-
nections to make sure they are secure. Review and cor-
rect any signs of wear.
Every 90 Days & With Annual Inspection
Check items mentioned above in Daily & 30 Day
inspections.
Also inspect weld integrity at the following connec-
tions: suspension-to-axle, anti-turn washer, locking
plate and hanger-to-frame.
All pivot and clamping connections such as the sus-
pension pivot and the shock mounting must be in-
spected. All pivot and clamping connections such as
the suspension pivot and the shock mounting must be
inspected.
NOTICE!! RIDEWELL CORP. BEARS NO RE-
SPONSIBILITY FOR SUSPENSIONS DAMAGED
BY ABUSE OR NEGLECT. IN ADDITION, ANY
SUSPENSIONS DRIVEN TO COMPLETE DE-
STRUCTION WILL NOT BE COVERED BY WAR-
RANTY.
Inspect for
installation of anti-turn
washer for proper
welding as shown
at right.
1/4" Fillet Welds,
1" Long, After Axle
Is Aligned.
xxx
x
x
xx
x
x
x