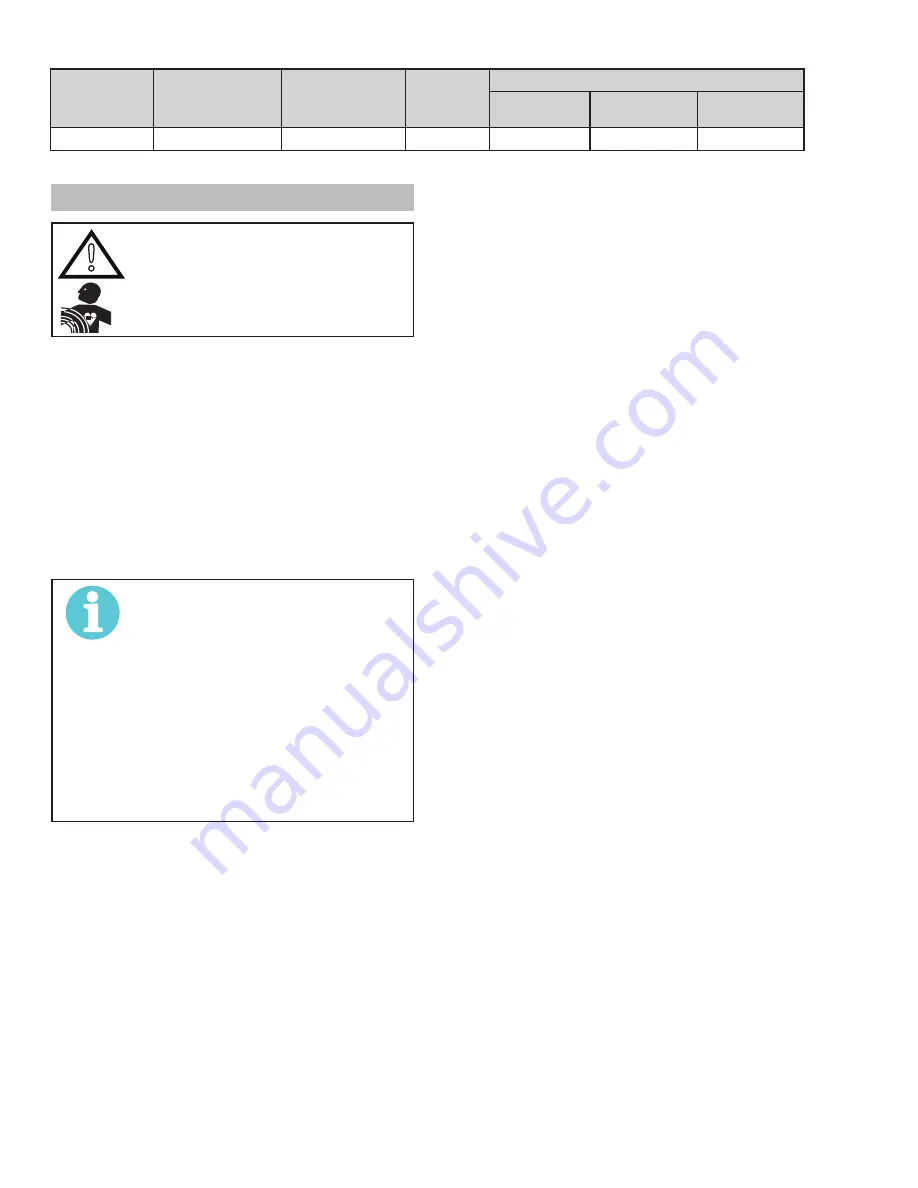
ESAB FABRICATOR 252i
INSTALLATION/SETUP 3-2 Manual 0-5423
50/60 Hz
Single Phase
Primary Supply
Lead Size
Minimum Primary
Current Circuit
Size (Vin/Iin)
Minimum
Plug Size
Current & Duty Cycle
MIG
LIFT TIG
STICK
Yes
10 AWG
208-230/50A
50A
40% @ 250A
40% @ 250A
40% @ 230A
Table 3-1: Input Power Source Leads for Fabricator 252i
3.05 Electromagnetic Compatibility
!
WARNING
Extra precautions for Electromagnetic
Compatibility may be required when this
Welding Power Source is used in a domes-
tic situation.
A. Installation and Use - Users Responsibility
The user is responsible for installing and using the welding
equipment according to the manufacturer’s instructions. If
electromagnetic disturbances are detected then it shall be the
responsibility of the user of the welding equipment to resolve the
situation with the technical assistance of the manufacturer. In
some cases this remedial action may be as simple as earthing
the welding circuit, see NOTE below. In other cases it could
involve constructing an electromagnetic screen enclosing the
Welding Power Source and the work, complete with associated
input filters. In all cases, electromagnetic disturbances shall be
reduced to the point where they are no longer Troublesome.
NOTE!
The welding circuit may or may not be
earthed for safety reasons. Changing the
earthing arrangements should only be
authorized by a person who is competent to
assess whether the changes will increase
the risk of injury, e.g. by allowing parallel
welding current return paths which may
damage the earth circuits of other equip-
ment. Further guidance is given in IEC
60974-13 Arc Welding Equipment - Instal-
lation and use (under preparation).
B. Assessment of Area
Before installing welding equipment, the user shall make
an assessment of potential electromagnetic problems in the
surrounding area. The following shall be taken into account.
1. Other supply cables, control cables, signaling and telephone
cables; above, below and adjacent to the welding equipment.
2. Radio and television transmitters and receivers.
3. Computer and other control equipment.
4. Safety critical equipment, e.g. guarding of industrial
equipment.
5. The health of people around, e.g. the use of pace-makers
and hearing aids.
6. Equipment used for calibration and measurement.
7. The time of day that welding or other activities are to be
carried out.
8. The immunity of other equipment in the environment: the
user shall ensure that other equipment being used in the
environment is compatible: this may require additional
protection measures.
The size of the surrounding area to be considered will depend on
the structure of the building and other activities that are taking
place. The surrounding area may extend beyond the boundaries
of the premises.
C. Methods of Reducing Electromagnetic Emissions
1. Mains Supply
Welding equipment should be connected to the mains
supply according to the manufacturer’s recommendations.
If interference occurs, it may be necessary to take
additional precautions such as filtering of the mains supply.
Consideration should be given to shielding the supply cable
of permanently installed welding equipment in metallic
conduit or equivalent. Shielding should be electrically
continuous throughout its length. The shielding should
be connected to the Welding Power Source so that good
electrical contact is maintained between the conduit and
the Welding Power Source enclosure.
2. Maintenance of Welding Equipment
The welding equipment should be routinely maintained
according to the manufacturer’s recommendations. All
access and service doors and covers should be closed
and properly fastened when the welding equipment is in
operation. The welding equipment should not be modified in
any way except for those changes and adjustments covered
in the manufacturer’s instructions.
3. Welding Cables
The welding cables should be kept as short as possible and
should be positioned close together but never coiled and
running at or close to the floor level.
4. Equipotential Bonding
Bonding of all metallic components in the welding instal-
lation and adjacent to it should be considered. However,
metallic components bonded to the work piece will increase
the risk that the operator could receive a shock by touch-
ing the metallic components and the electrode at the same
time. The operator should be insulated from all such bonded
metallic components.
Содержание Fabricator 252i
Страница 70: ...ESAB FABRICATOR 252i REPLACEMENT PARTS 6 6 Manual 0 5423 This Page Intentionally Blank...
Страница 75: ......