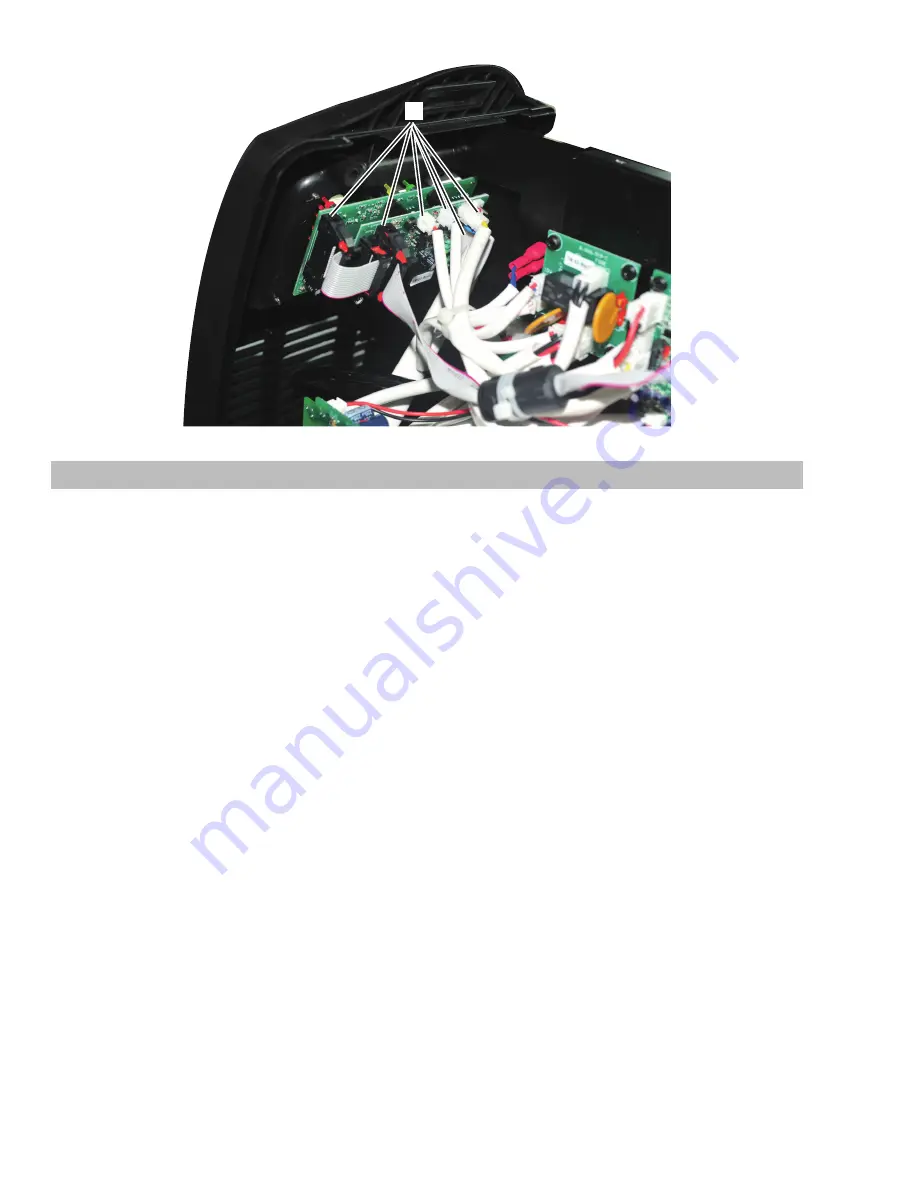
ESAB FABRICATOR 141i
ASSEMBLY PROCEDURES 8-4 Manual 0-5448
6
Art # A-12183
8.04 Installing Control PCB2 and Clear Protective Sheet
1. Install 4 screws.
2 Plug harness into DRIVE connector.
3. Plug harness into SOURCE connector.
4. Plug harness into CR connector.
5. Plug harness into FUNs connector
6. Plug harness into NTCs connector.
7. Plug harness into IGBT OT connector .
8. Plug harness into GUN connector.
9. Plug harness into QF/DY connector.
10. Plug harness into WVIN connector.
11 Plug harness into MB connector.
12. Plug harness into PWM connector.
13. Plug harness into IFB connector.
Verify harness connections with the system schematic to ensure all connections are correct.
14. Install clear protective sheet.
Содержание fabricator 141i
Страница 19: ...ESAB FABRICATOR 141i Manual 0 5448 3 9 SAFETY AND INSTALLATION Notes...
Страница 20: ...ESAB FABRICATOR 141i SAFETY AND INSTALLATION 3 10 Manual 0 5448 This Page Intentionallly Blank...
Страница 40: ...ESAB FABRICATOR 141i OPERATION 4 20 Manual 0 5448 This Page Intentionally Blank...
Страница 42: ...ESAB FABRICATOR 141i THEORY OF OPERATION 5 2 Manual 0 5448 Notes...
Страница 70: ...ESAB FABRICATOR 141i DISASSEMBLY PROCEDURE 7 4 Manual 0 5448 2 3 4 Art A 12181...
Страница 79: ...ESAB FABRICATOR 141i Manual 0 5448 8 5 ASSEMBLY PROCEDURES Art A 12184 6 5 4 3 2 7 8 9 10 11 12 13 14...
Страница 81: ...ESAB FABRICATOR 141i Manual 0 5448 8 7 ASSEMBLY PROCEDURES Notes...
Страница 82: ...ESAB FABRICATOR 141i ASSEMBLY PROCEDURES 8 8 Manual 0 5448 Notes...
Страница 84: ...ESAB FABRICATOR 141i KEY SPARE PARTS 9 2 Manual 0 5448 9 02 Power Source Art A 11811_AB Figure 9 2 31...
Страница 88: ...ESAB FABRICATOR 141i KEY SPARE PARTS 9 6 Manual 0 5448 Notes...
Страница 91: ......