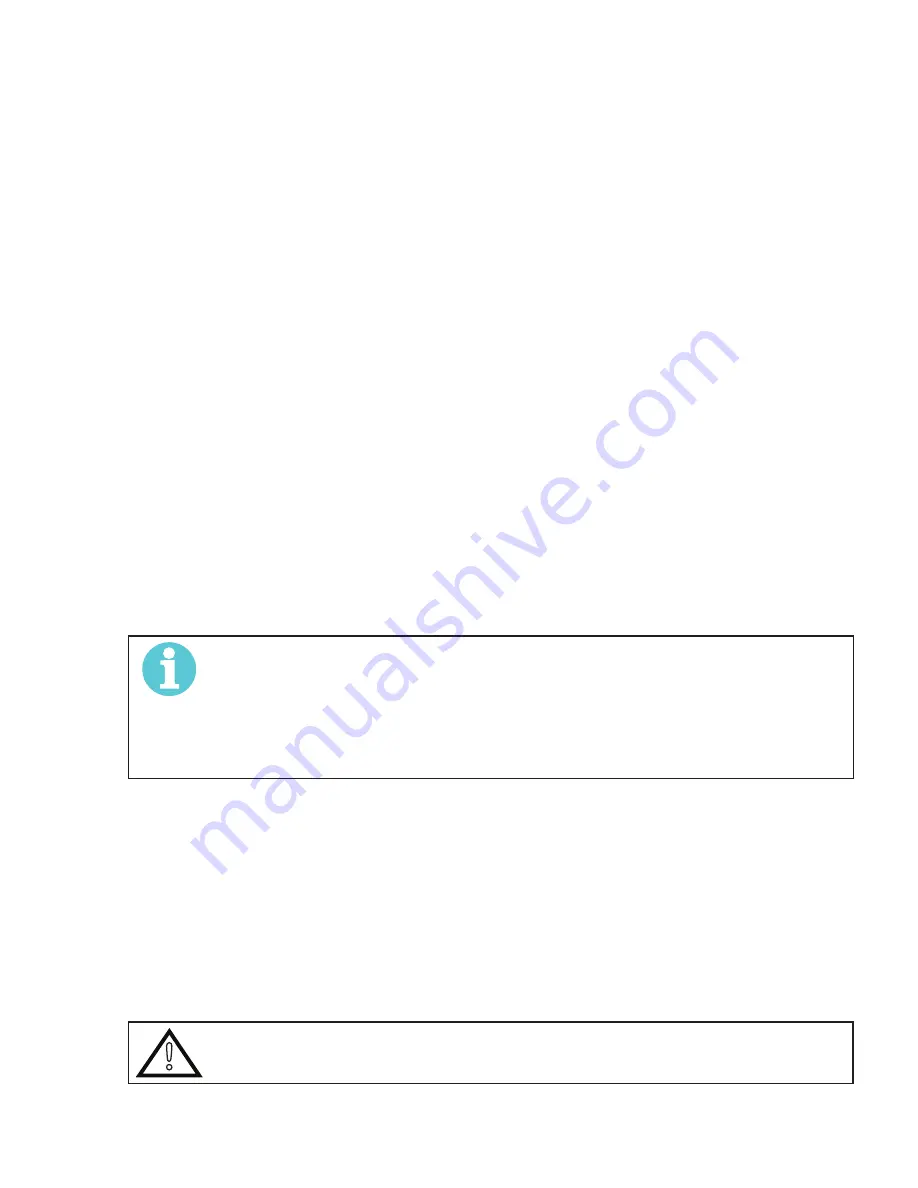
ESAB FABRICATOR 141i
Manual 0-5448
4-5 OPERATION
4T (Latch Mode)
This mode of welding is mainly used for long welding runs to reduce operator fatigue. In this mode the operator can press and
release the MIG or TIG Trigger Switch and the output will remain active. To deactivate the Power Source, the trigger switch must
again be depressed and released, thus eliminating the need for the operator to hold the MIG or TIG Trigger Switch
Note that when operating in LIFT TIG mode, the Power Source will remain activated until the selected Downslope time has
elapsed (refer Control No. 9).
12. Process Selection Control
The process selection control is used to select the desired welding mode. Three modes are available, MIG, LIFT TIG and STICK
modes. Refer to section
4.10 through 4.12 for MIG (GMAW/FCAW) set up details, section 4.13 for LIFT TIG (GTAW) set-up details
or section 4.14 for STICK (SMAW) set-up details.
Note that when the Power Source is powered off the mode selection control will automatically default to MIG mode. This is
necessary so as to prevent inadvertent arcing should an electrode holder be connected to the Power Source and mistakenly be
in contact with the work piece during power up.
13. Digital Voltage Meter (Right Digital Display)
The digital voltage meter is used to display the both the preview voltage (MIG mode only) and actual output voltage (all modes)
of the Power Source.
At times of non-welding, the voltage meter will display a preview value in MIG mode. This value can be adjusted by varying the
multifunction control knob (Control No. 9). Note that in STICK and LIFT TIG modes, the voltage meter will not preview welding
voltage but will display Open Circuit Voltage in STICK mode and 0V in LIFT TIG mode.
When welding, the voltage meter will display actual welding voltage in all modes.
At the completion of welding, the digital voltage meter will hold the last recorded voltage value for a period of approximately 10
seconds in all modes. The voltage meter will hold the value until; (1) any of the front panel controls are adjusted in which case
the Power Source will revert to preview mode, (2) welding is recommenced, in which case actual welding amperage will be
displayed, or (3) a period of 10 seconds elapses following the completion of welding in which case the Power Source will return
to preview mode.
NOTE!
The preview functionality provided on this power source is intended to act as a guide only. Some dif-
ferences may be observed between preview values and actual welding values due to factors including
the mode of welding, differences in consumables/gas mixtures, individual welding techniques and the
transfer mode of the welding arc (ie dip versus spray transfer). Where exact settings are required (in the
case of procedural work), it is recommended that alternate measurement methods be utilized to ensure
output values are accurate.
14. Fault Indicator
This welding Power Source is protected by a self resetting thermostat. The indicator will illuminate if the duty cycle of the Power
Source has been exceeded or if a fault is detected in the Inverter. Should the Fault Indicator illuminate the output of the Power
Source will be disabled. Once the Power Source cools down this light will go OFF and the over temperature condition will auto-
matically reset. Note that the power switch should remain in the on position such that the fan continues to operate thus allowing
the Power Source to cool sufficiently. Do not switch the Power Source off should a thermal overload condition be present. If
the fault condition does not extinguish, then the Power Supply will need to be taken to an authorized repair center for analysis.
15. Gas Inlet (MIG mode only for MIG Gun or Spool Gun operation)
The Gas Inlet connection is used to supply the appropriate MIG welding gas to the Power Source. Refer to section 4.10 to 4.11
for MIG (FCAW/GMAW) set up details.
!
WARNING
Only Welding Shielding Gases specifically designed for arc welding applications should be used.
Содержание fabricator 141i
Страница 19: ...ESAB FABRICATOR 141i Manual 0 5448 3 9 SAFETY AND INSTALLATION Notes...
Страница 20: ...ESAB FABRICATOR 141i SAFETY AND INSTALLATION 3 10 Manual 0 5448 This Page Intentionallly Blank...
Страница 40: ...ESAB FABRICATOR 141i OPERATION 4 20 Manual 0 5448 This Page Intentionally Blank...
Страница 42: ...ESAB FABRICATOR 141i THEORY OF OPERATION 5 2 Manual 0 5448 Notes...
Страница 70: ...ESAB FABRICATOR 141i DISASSEMBLY PROCEDURE 7 4 Manual 0 5448 2 3 4 Art A 12181...
Страница 79: ...ESAB FABRICATOR 141i Manual 0 5448 8 5 ASSEMBLY PROCEDURES Art A 12184 6 5 4 3 2 7 8 9 10 11 12 13 14...
Страница 81: ...ESAB FABRICATOR 141i Manual 0 5448 8 7 ASSEMBLY PROCEDURES Notes...
Страница 82: ...ESAB FABRICATOR 141i ASSEMBLY PROCEDURES 8 8 Manual 0 5448 Notes...
Страница 84: ...ESAB FABRICATOR 141i KEY SPARE PARTS 9 2 Manual 0 5448 9 02 Power Source Art A 11811_AB Figure 9 2 31...
Страница 88: ...ESAB FABRICATOR 141i KEY SPARE PARTS 9 6 Manual 0 5448 Notes...
Страница 91: ......