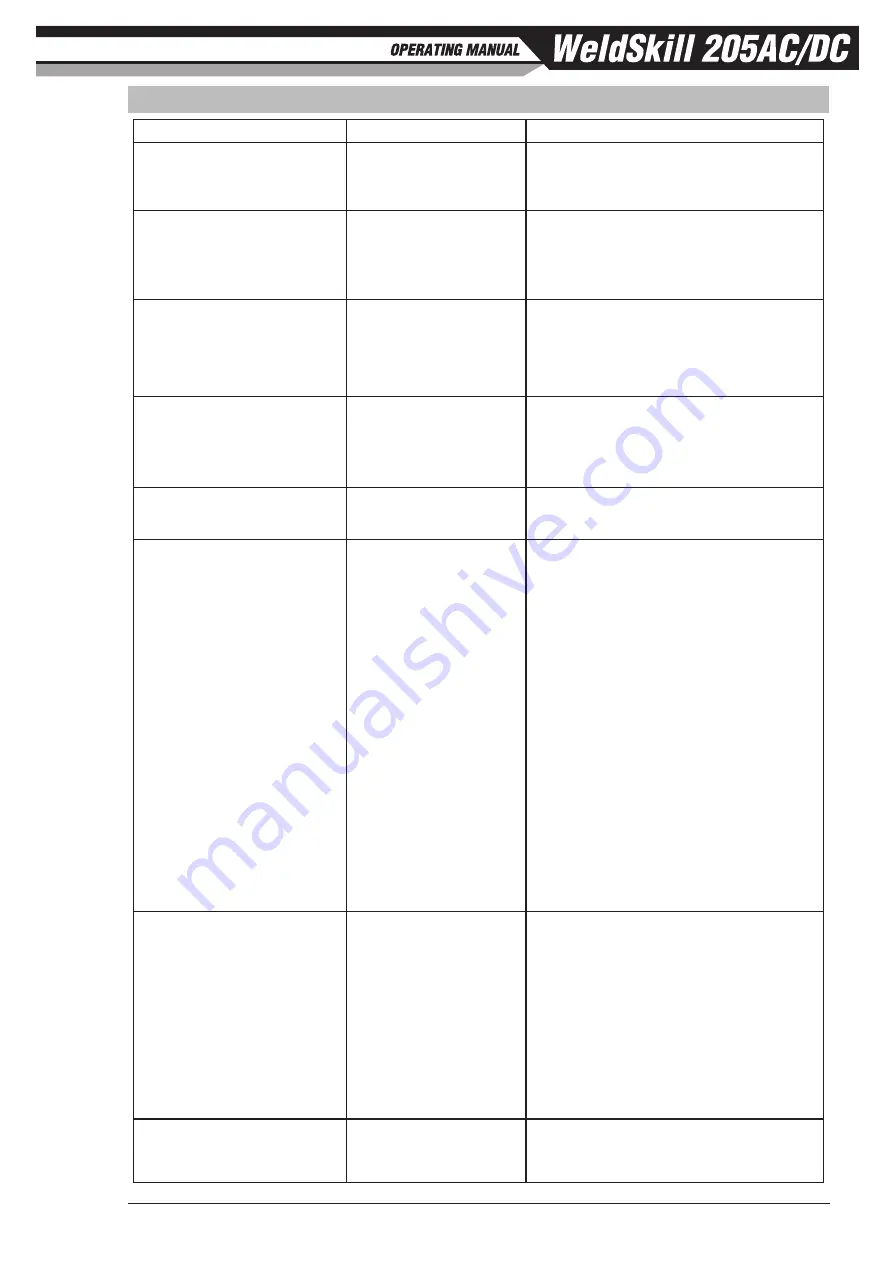
0-5555 5-11
TIG (GTAW) Welding
5.06 TIG (GTAW) Welding Problems
FAULT
CAUSE
REMEDY
1 Excessive bead build up or
poor penetration or poor
fusion at edges of weld.
Welding current is too
low
Increase weld current and/or faulty joint
preparation.
2 Weld bead too wide and
flat or undercut at edges
of weld or excessive burn
through.
Welding current is too
high
Decrease weld current.
3 Weld bead too small or
insufficient penetration or
ripples in bead are widely
spaced apart.
Travel speed too fast
Reduce travel speed.
4 Weld bead too wide or
excessive bead build up or
excessive penetration in
butt joint.
Travel speed too slow
Increase travel speed.
5 Uneven leg length in fillet
joint
Wrong placement of
filler rod
Re-position filler rod.
6 Electrode melts or oxidises
when an arc is struck.
A Torch lead connected
to positive welding
terminal.
A Connect torch lead to negative welding
terminal.
B No shielding gas
flowing to welding
region.
B Check the shielding gas lines for kinks
or breaks and shielding gas cylinder
contents.
C Torch is clogged with
dust or dirt.
C Clean torch.
D Shielding gas hose is
damaged.
D Replace shielding gas hose.
E Shielding gas regulator
turned off.
E Turn On Shielding Gas and adjust
Shielding Gas flow rate for the welding
job. Refer to Table 5-7 on Page 5-10.
F The electrode is too
small for the welding
current.
F Increase electrode diameter or reduce the
welding current.
7 Dirty weld pool
A Electrode contaminated
by contact with work
piece or filler rod
material.
A Clean the electrode by grinding off the
contaminates.
B Work piece surface has
foreign material on it.
B Clean surface.
C Shielding gas
contaminated with air.
C Check shielding gas lines for cuts and
loose fitting or change shielding gas
cylinder.
8 Poor weld finish
Inadequate shielding
gas.
Increase shielding gas flow or check
shielding gas line for shielding gas flow
problems.
Содержание CIGWELD WeldSkill 205AC/DC
Страница 8: ...This Page Intentionally Blank...
Страница 14: ...GENERAL INFORMATION 1 6 0 5555 This Page Intentionally Blank...
Страница 28: ...INSTALLATION 3 6 0 5555 This page is left blank intentionally...
Страница 68: ...APPENDIX A 2 0 5555 This Page Intentionally Blank...
Страница 71: ...This Page Intentionally Blank...