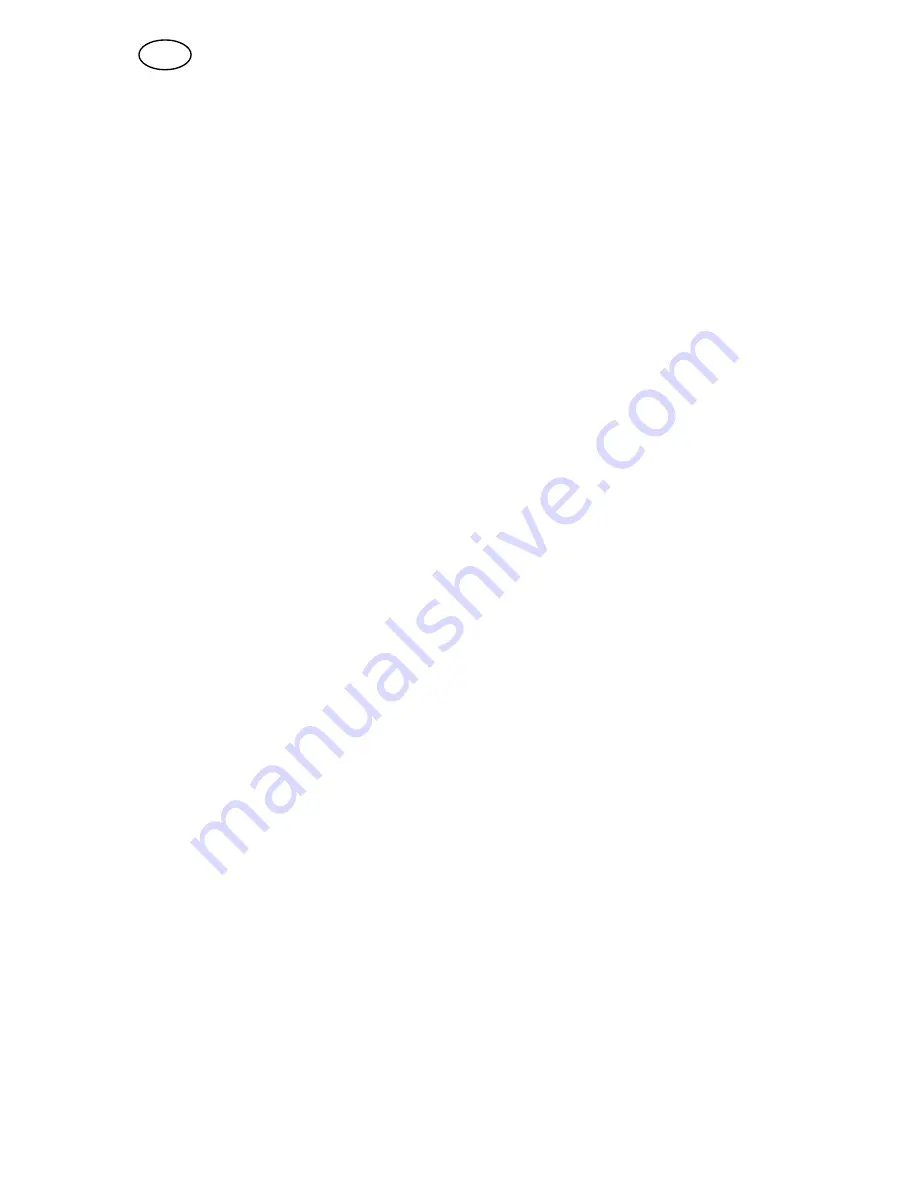
© ESAB AB 2003
- 12 -
bu20d1ea
5.2
Turning on the power source
Turn on the mains power by turning switch (7) to the ”START” position. Release the
switch, and it will return to the ”1” position.
If the mains power supply should be interrupted while welding is in progress, and
then be restored, the power source will remain de-energised until the switch is again
turned manually to the ”START” position.
Turn the unit off by turning the switch to the ”0” position.
Whether in the event of a loss of power supply or of turning the power source off in
the normal manner, welding data will be stored so that it is available next time the
unit is started.
5.3
Fan control
The power source fans continue to run for 6,5 minutes after welding has stopped,
and the unit switches to energy-saving mode. They start again when welding
restarts.
The fans run at reduced speed for welding currents up to 144 A, and at full speed for
higher currents.
5.4
Overheating protection
The power source has two thermal overload trips which operate if the internal
temperature becomes too high, interrupting the welding current and lighting the
orange indicating lamp on the front of the unit. They reset automatically when the
temperature has fallen.
5.5
Cooling unit
To ensure problem-free operation, the installation height from the cooling unit to the
welding gun must be max. 7 m. Heights in excess of this can cause problems, such
as long starting times, air bubbles, vacuums, etc.
If an installation height in excess of 7 m is required, we recommend an installation kit
comprising a non-return valve and a solenoid valve, refer to accessories on page 21.
Once these valves have been installed, the hose package must be horizontal during
the initial startup so that everything fills with water. Then raise the wire feed unit and
hose package to the high height. Continued safe operation at installation heights of
up to 12 m can now commence.
Water connection (TIG welding)
The cooling unit is equipped with a detection system
ELP
(
E
SAB
L
ogic
P
ump)
which checks that the water hoses are connected.
The power source On/Off switch must be in the “0” position (Off) when connecting a
water-cooled TIG torch.
If a water-cooled TIG torch is connected, the water pump starts automatically when
the main On/Off switch is turned to ”START” and/or when welding starts. After
welding, the pump continues to run for 6,5 minutes, and then switches to the
energy-saving mode.
GB
Содержание Aristo Mig U4000i
Страница 2: ... 2 ...
Страница 16: ... ESAB AB 2003 Diagram 16 bu20e11a ...
Страница 17: ... ESAB AB 2003 17 bu20e11a ...
Страница 18: ... ESAB AB 2003 18 bu20e11a Cooling unit ...
Страница 25: ... 25 notes NOTES ...
Страница 26: ... 26 notes NOTES ...
Страница 27: ... 27 notes NOTES ...