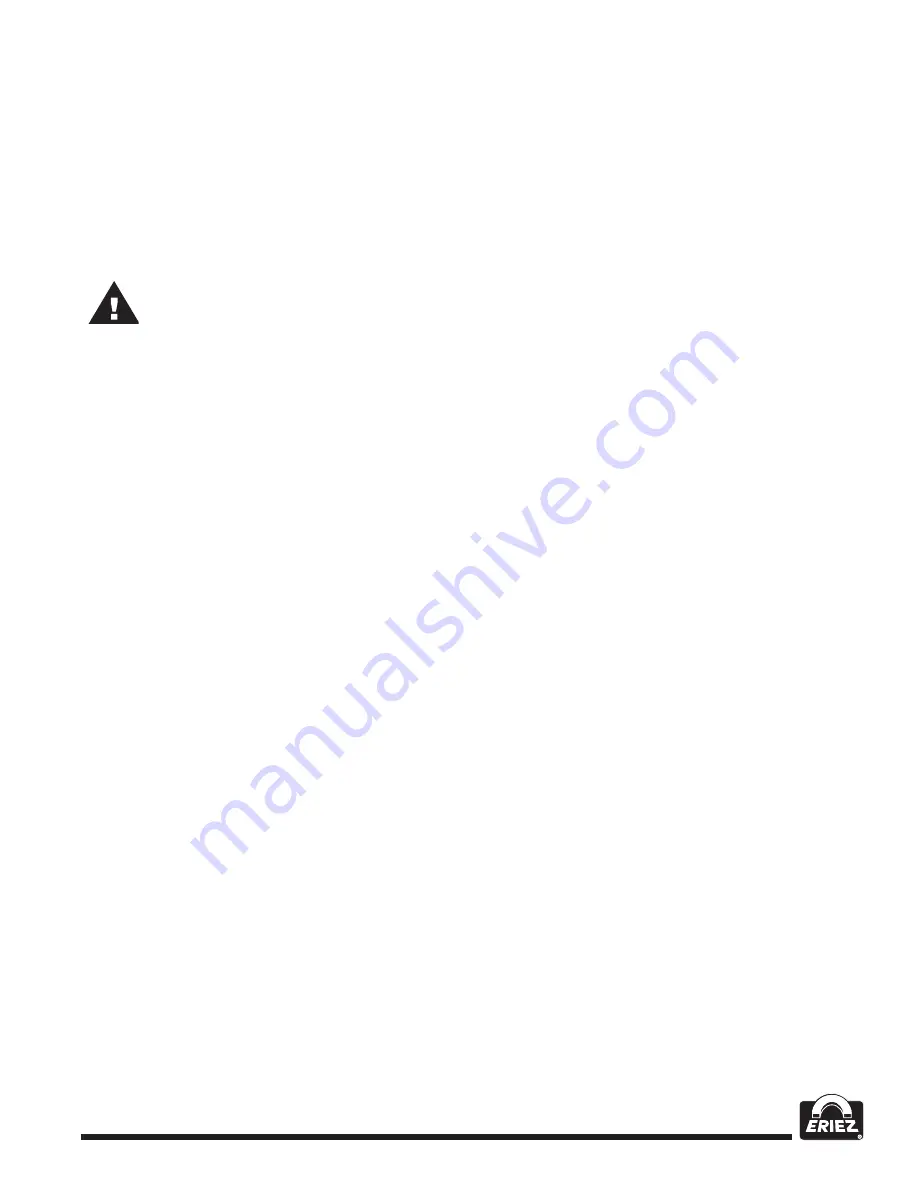
9
N12- G & HW Series Frequency Controllers 115/230VAC
Commissioning
Preliminary Steps
• Check that the unit is correct for the local mains
supply (rating plate information) and that it is
correctly rated for the feed system.
• Connect the controller according to the
connection diagram.
Important Points
Using the control units described in this
document, it is possible to adjust the feed
system so that it runs at resonance. In this
condition, it is possible to obtain excessive output for
a very low set point setting. Therefore, extreme care
should be taken to avoid causing damage to the drive
coil through hammering.
In practice, it is not possible to run at resonant
frequency without accelerometer feedback because
the system would be unstable and uncontrollable. The
system must be set safely off resonance i.e. either
above or below the natural frequency.
Resonant frequency: Depending on the spring and
mass design of the feeder system, it is possible to
have resonance at more than one frequency. These
additional resonance points are multiples of the main
frequency. For this reason, in critical situations, it is
possible that the automatic frequency search will not
find true resonance and in such cases the natural
frequency must be determined manually.
Operating Frequency of the Feeder Coil
It is possible that the current flowing through the coil
will increase for a small frequency adjustment. So this
should be checked with a true RMS instrument for each
new application as well as monitoring the coil for heat
build-up.
The coil should be designed for the correct operating
frequency to prevent excessive current draw and the
consequential overloading of the coil.
Measurement of the Output Voltage and Current
The voltage and current cannot be measured with a
regular instrument because the controller output uses
an electronic inverter with a pulse width modulation
signal. An effective measuring instrument such as
a moving iron meter (analog) must be used. It is
recommended that an analog instrument is used
rather than an electronic multi-meter which will give
a misleading reading.
Putting the Equipment into Operation
1. Establish the vibrating frequency.
2. Establish the power of the feed system (maximum
permissible current draw).
For a new feeder where settings are unknown
(see also comments below).
Without connecting the feeder, select parameter
FAC in menu C210 (reset factory settings), press the
cursor key to reset (SAFE) and press the P key to
leave the menu. The factory settings are listed in the
table in section 7, headed settings.
! Comments !
It is possible that a special parameter set, for a
machine manufacturer, has been pre-stored under
a user code and these can be recalled. In such
instances, specific machine settings will be loaded and
so the next steps are not relevant.
Basic settings:
• Connect feeder.
• Set frequency (refer to feeder data sheet).
Menu C096. parameter F.
• Check current limit (refer to feeder data sheet).
Menu C04.0 parameter I (shows the current limit
as a percentage of maximum). If applicable, use
service menu for setting.
• Increase set point, observe feeder, check running.
• Increase set point to maximum and check if power
needs limiting (hammering). If necessary, adjust
the limit as follows:
• Adjust set point to zero.
• Set parameter P (maximum limit) in
Menu C096. to 50.
• Adjust set point A to 100%.
• Increase the maximum limit P from 50% until the
required amplitude is reached.
• The full set point range of 0…100% can now
be used.
Additional settings e.g. soft start, time delays etc. can
be set to suit the particular equipment.