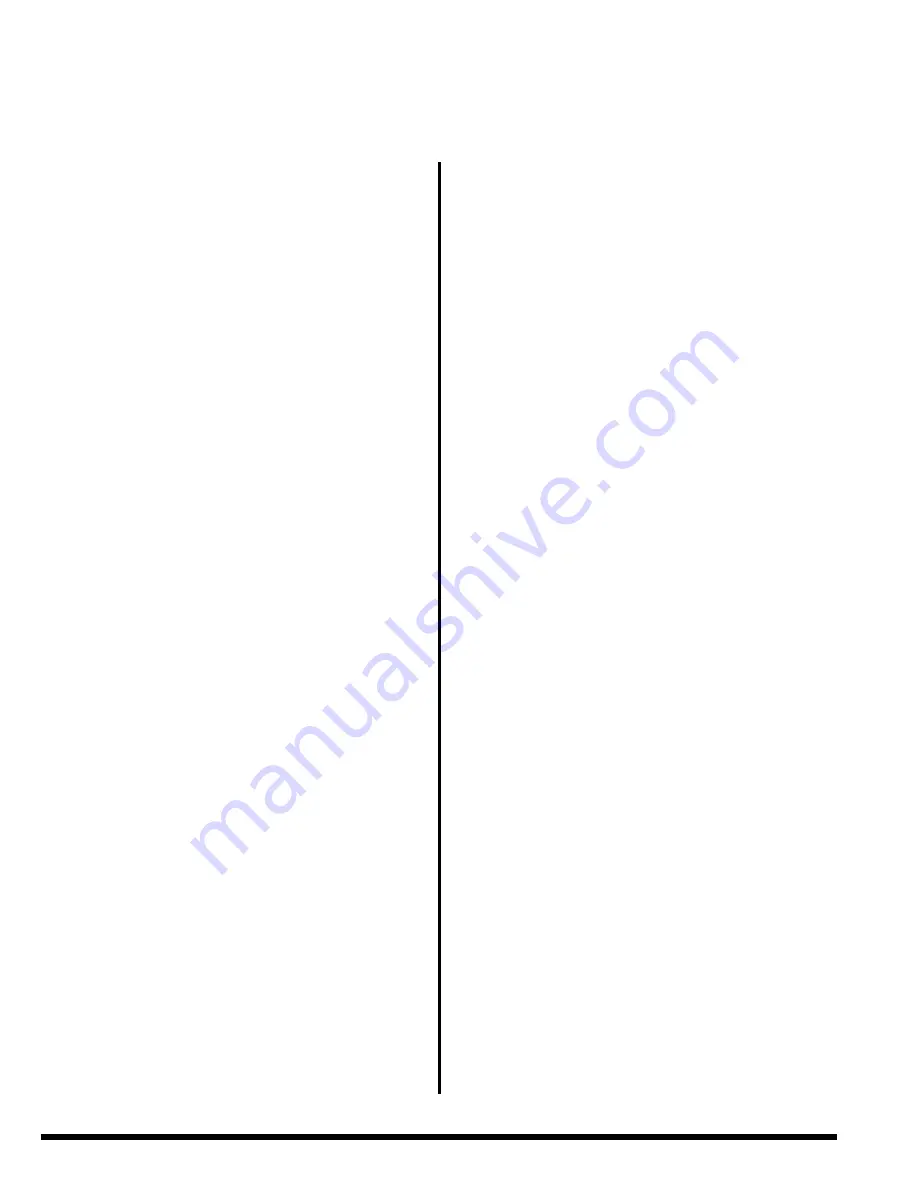
8
PLEASE READ THROUGH COMPLETELY
BEFORE BEGINNING WORK!
A. UNpACkING
Upon receipt of the crate(s) containing the Metal
Detector System, inspect the contents for physical
damage and missing parts. If anything is broken or
missing, please contact the carrier and notify the
supplier immediately.
B. SITE SELECTION &
pREpARATION
While each application is unique, the guidelines
listed below apply to most installations. Specific in-
formation concerning your installation can be found
in the Frame Assembly and Control Connection
Diagrams. Follow the steps listed below to choose
the best location for the detector.
• Choose a location for the detector so the mater
ial handling system has ample time to react to
tramp metal. Locate the detector far enough in
advance of the head pulley so the belt can come
to a stop before the metal falls off the end of the
belt If a diverter is used, consider the reaction
time of the system and speed of the conveyor
belt.
• Select a site with minimum vibration. High vibra
tion areas may degrade detector sensitivity and
shorten component life.
• Locate the Search Coil Assembly away from
sources of airborne electrical interference emit-
ted from variable-speed drives, large motors,
ballasts, FM radios, induction furnaces and oth-
er radio fre quency (RF) sources. Although the
receiver coil is shielded on five sides to reduce
the effects of RF noise, the surface facing the
transmitter is unshielded and therefore suscep-
tible to RF noise. Because RF energy travels
along a straight line (line-of-sight), position the
receiver coil or relocate RF sources so they are
below or out of the direct line-of-sight with the top
of the receiver. Cables carrying high voltage or
varying loads must be enclosed in steel conduit,
grounded at both ends and located at least 4'
(1.2 m) from the detector antennas.
• Position the entire search coil assembly so that
the bottom coil (usually the receiver) is equally
spaced between the two adjacent idler rollers.
Center the receiver coil.
Do not center the 2" x
2" uprights.
• The magnetic field generated by the transmitter
coil induces eddy currents in nearby metal cross
bracing, stairways, handrails and pipes. These
eddy currents may cause false tripping if the current
path intermittently makes contact. Eddy current
loops can be broken by cutting the conductive
paths in these structures. Use non-metallic hard-
ware as required to restore structural support. If
conveyor idlers are used in your application, the
idlers adjacent to the Search Coil Assembly may
require modification or isolation to break eddy cur-
rent loops. Refer to the Conveyor Idler Modifica tion
Diagram (if applicable) for details.
• If the Search Coil Assembly is located where
a metal skirt passes through the coils, it must
be replaced with a five-foot (1.5 m) section of
non-metallic material (i.e., wood or plastic).
• Relocate or tightly secure moving or vibrating
pieces of metal such as cables, conduit and
piping within 36" (914 mm) of the Search Coil As-
sembly. Remove metallic decking, skirt boards,
cross brac ing and return idlers below and within
3' (914 mm) of the center line of the receiver coil
(upstream and downstream).
C. MOUNTING - SEARCh COIL
ASSEMBLy
Note the material flow direction arrows match marks
and other identification on the Detector components
before beginning work. Please refer to the Frame
Assembly Diagram for installation
• Fasten the receiver coil to the material handling
system. Shim the unit as necessary to provide a
uniform and sturdy mounting surface. Maintain
clearance between the coil and any moving ob-
jects. Do not torque, twist or use excessive force
when fastening the coil to the structure. Do not
drill or weld the coil
part II - Installation
Содержание 1250 ANALOG
Страница 6: ...6 Part I Operation Description cont FIGURE 1 MAIN CONTROL ENCLOSURE NEMA 4 4X 7 OR 9...
Страница 7: ...7 Part I Operation Description cont FIGURE 2 ELECTRONIC MODULE...
Страница 11: ...11 Part II Installation cont FIGURE 3 SWING AWAY FRAME ASSEMBLY FIGURE 4 FIXED FRAME ASSEMBLY...
Страница 13: ...13 Part II Installation cont...
Страница 20: ...20 TABLE 6 PROGRAMMING CONTROLS SUMMARY Part IV System Programming cont...
Страница 21: ...21 Part IV System Programming cont...
Страница 23: ...23 Part V Troubleshooting cont TABLE 7 ELECTRONICS MODULE STATUS INDICATOR SUMMARY...
Страница 24: ...24 Part V Troubleshooting cont FIGURE 5 PROGRAMMING CONTROLS AND TEST POINT LOCATIONS...
Страница 25: ...25 Part V Troubleshooting cont TROUBLESHOOTING FLOW DIAGRAM 1 INSUFFICIENT METAL SENSITIVITY...
Страница 26: ...26 Part V Troubleshooting cont TROUBLESHOOTING FLOW DIAGRAM 2 FALSE TRIPPING...
Страница 27: ...27 Part VI Maintenance 1 10 Amp Fuse 2 Spare Bulbs 1 1 16 Allen Key Wrench 1 5 64 Allen Key...