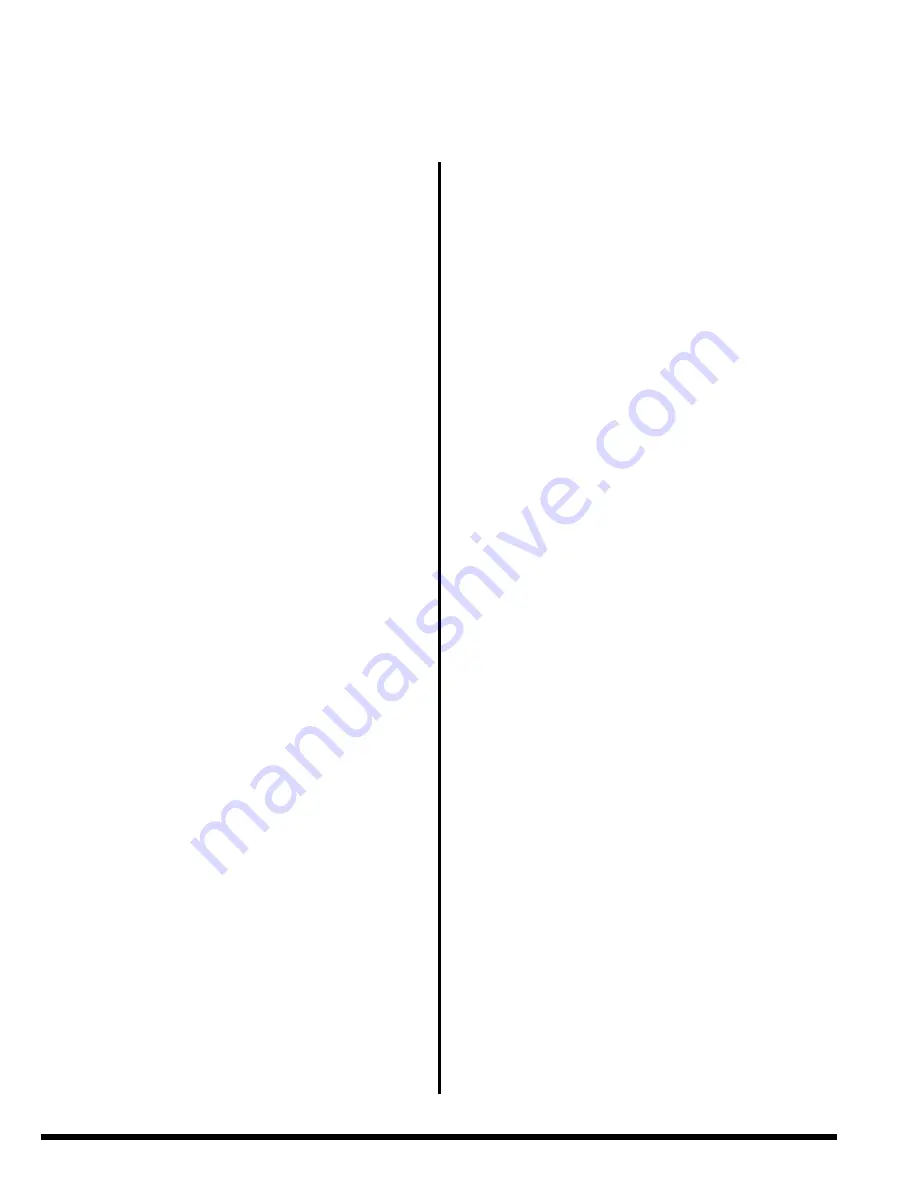
12
NOTE: The 1" x 1" (25 x 25 mm) support structure
is a solid fiberglass bar.
• Position the support bracket of the solenoid spray
valve so that the nozzle is pointed directly on the
center of the conveyor belt. The nozzle may be
positioned as shown or on the opposite side of
the arm. Bolt the bottom of the support frame to
the conveyor frame.
• The solenoid control cable is connected to the
Interface Module Timed Output (Terminal TR2,
Pins 4 & 5). Route the cable accordingly.
• Connect the hose between the tank outlet and
the solenoid valve.
• Connect the facility air source to the tank regu-
lator inlet. Be sure the facility air source is shut
off and no pressure is in the tank
• Remove the top of the spray tank.
• The spray solution is supplied by the User. The
recommended mixture is five (5) fluid ounces
(148 cc) of colorant. Chrome Yellow (or other
contrasting colors manufactured by Tenneco
Chemical (or equivalent) mixed with a two (2)
gallon (7.6 l) solution of water and antifreeze
appropriate for local climate conditions (minimum
of 25% antifreeze)
• Mix the solution and pour it into the holding tank.
Replace the cap.
• Verify that the pressure regulator valve is closed
prior to turning on the facility air.
• Apply the facility air and adjust the pressure
reg ulator between 60 and 100 psig (4-6.7 bar),
as noted on the pressure gauge on top of the
holding tank.
CALIBRATION Of MARkING DEvICE
• Refer to Section IV.E and IV.F to set the desired
timing for marking a predetermined location.
• Using a Sample piece of tramp metal, with the
belt operating at normal load, adjust the Marking
Device timing by trial and error.
part II - Installation (cont.)
Содержание 1250 ANALOG
Страница 6: ...6 Part I Operation Description cont FIGURE 1 MAIN CONTROL ENCLOSURE NEMA 4 4X 7 OR 9...
Страница 7: ...7 Part I Operation Description cont FIGURE 2 ELECTRONIC MODULE...
Страница 11: ...11 Part II Installation cont FIGURE 3 SWING AWAY FRAME ASSEMBLY FIGURE 4 FIXED FRAME ASSEMBLY...
Страница 13: ...13 Part II Installation cont...
Страница 20: ...20 TABLE 6 PROGRAMMING CONTROLS SUMMARY Part IV System Programming cont...
Страница 21: ...21 Part IV System Programming cont...
Страница 23: ...23 Part V Troubleshooting cont TABLE 7 ELECTRONICS MODULE STATUS INDICATOR SUMMARY...
Страница 24: ...24 Part V Troubleshooting cont FIGURE 5 PROGRAMMING CONTROLS AND TEST POINT LOCATIONS...
Страница 25: ...25 Part V Troubleshooting cont TROUBLESHOOTING FLOW DIAGRAM 1 INSUFFICIENT METAL SENSITIVITY...
Страница 26: ...26 Part V Troubleshooting cont TROUBLESHOOTING FLOW DIAGRAM 2 FALSE TRIPPING...
Страница 27: ...27 Part VI Maintenance 1 10 Amp Fuse 2 Spare Bulbs 1 1 16 Allen Key Wrench 1 5 64 Allen Key...