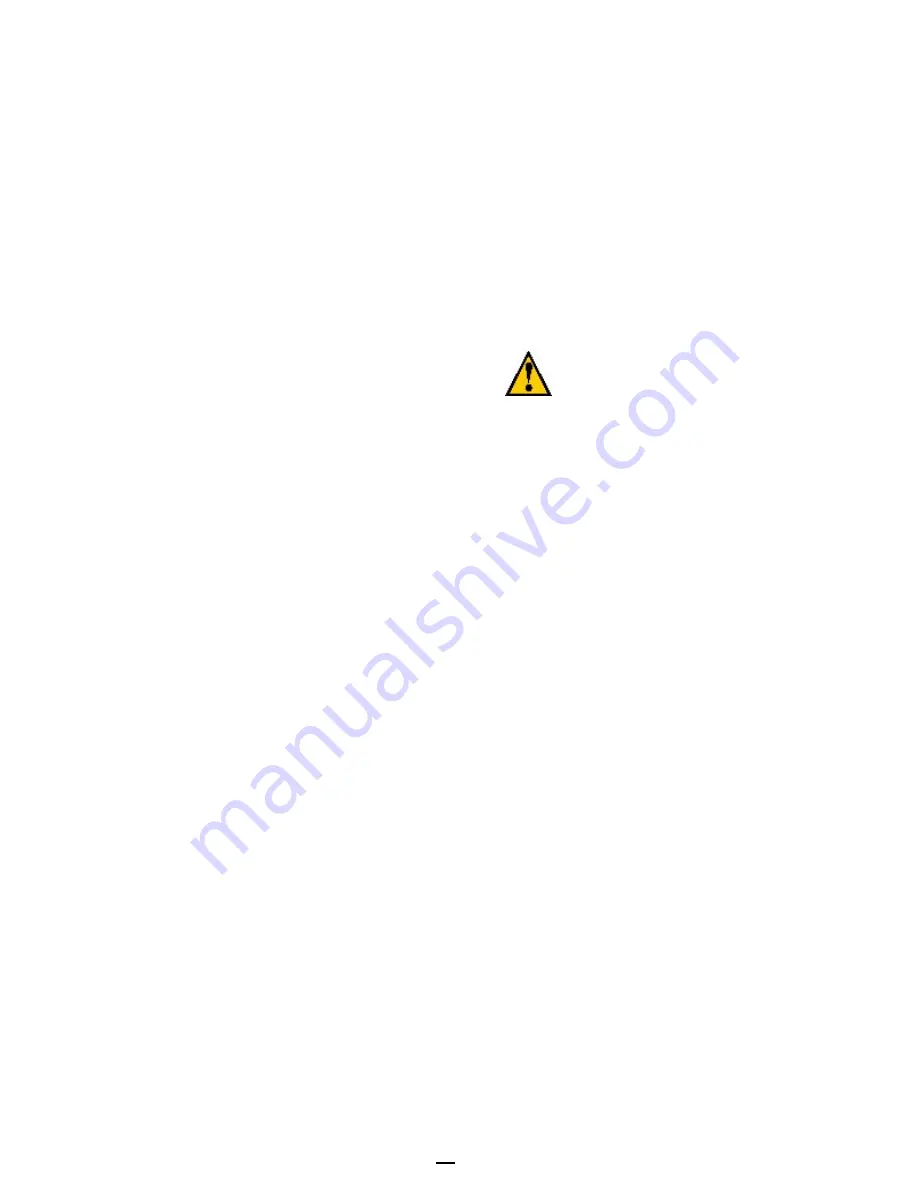
12
MACHINE START UP
1.
Start engine. To start engine, insert key into the control panel. Turn key to first position.
Warning lights should turn “ON.” Turn key to second position. Engine should start.
Release key when engine is running. Leave at idle for a few minutes. Move throttle
lever to set engine at desired speed (see Fig. 5). Make sure hydraulic control valve
switch is in the neutral position.
2.
Set temperature dials to desired temperature. Hot oil temperature should not exceed
525
O
F. and material 410
O
F. (see Fig. 6).
3.
Turn toggle switch “ON” (see Fig. 6).
CAUTION
If burners do not ignite the first time, turn toggle switch “OFF.” Turn toggle switch “ON.” Burner
should ignite. If burner still does not ignite, determine cause of malfunction (see Trouble
Shooting Guide, page 25).
4.
Allow the heating oil to continue to heat. Place bags of material in the mixer and heat.
Start the mixer as soon as possible to break up the bags. When loading solid material
into the mixer tank, the mixer will stop when lifting the lid (if equipped with lid switchs),
add material and close the lid again to start the mixer. Following this procedure will
prevent the hot material from splashing and causing serious burns to personnel.
Engage the mixer by moving the mixer hydraulic control toggle switch to forward or
reverse rotation. When changing the speed of mixing, move both bypass hydraulic
valves simultaneously. If mixer jams, switch may be moved for opposite rotation. The
speed of mixing is controlled by the position of the 2 bypass hydraulic valves
(see Fig. 8). The valves should be moved together (either in or out) not one at a time.
The minimum amount of material needed for proper mixer operation is 400 lbs.
5.
Temperature readout on burner control box indicates material temperature. When
patching material reaches correct application temperature, material may be drawn off
as desired. Discharge gate is opened by moving handle down. Drain material into
pour bucket.
Remove excess patching material from chute with scraping tool.
CAUTION:
Be sure discharge gate is completely closed after each draw off. Lock
handle with safety chain if machine is transported (see Fig. 2).
Содержание Crafco Patcher I Diesel
Страница 1: ...Patcher I Diesel PART MANUAL 56933 Rev 0...
Страница 2: ...2 Revised 02 06...
Страница 3: ...3 Patcher I Diesel Part Number 56900 Skid Mount...
Страница 13: ...13 Fig 1 Fig 2 grease fitting safety chain discharge gate...
Страница 14: ...14 Fig 3 Fig 4 heat transfer dipstick mixer control switch...
Страница 15: ...15 Fig 5 temperature dials Fig 6 throttle lever toggle switch...
Страница 16: ...16 Fig 7 Fig 8 by pass valves engine fuel tank...
Страница 20: ...20 MAINTENANCE CHART...
Страница 28: ...28 Patcher I Diesel...
Страница 30: ...30 Patcher I Diesel...
Страница 33: ...33 Patcher I Diesel Notes...
Страница 34: ...34 Patcher I Diesel HYDRAULIC DIAGRAM...
Страница 35: ...35 Patcher I Diesel HYDRAULIC PARTS...
Страница 36: ...36 Patcher I Diesel HYDRAULIC PARTS...