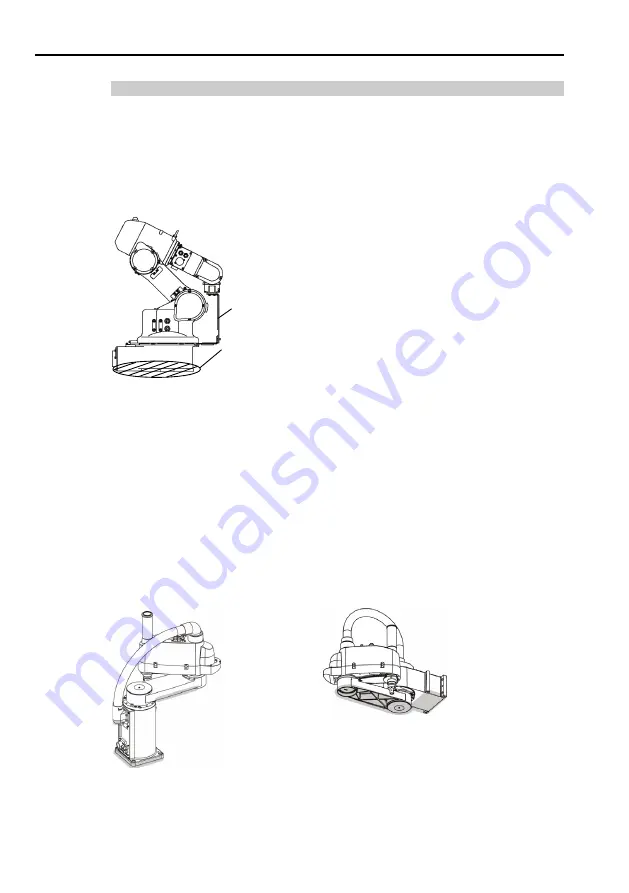
2. Installation
RC520 Safety and Installation Rev.2
20
14B
Manipulator Transportation
PS series
To carry the Manipulator, have at least 3 people to work on it and secure the
Manipulator to the delivery equipment or hold it by hand. Do not hold the
bottom of the base (the screened parts in the figure). Holding these parts by hand
is extremely hazardous and may cause your hands and fingers to be caught.
DO NOT hold
the bottom of
the base by hand.
Shipping
Bolts and Jigs
(Figure of PS3)
PS3
: Approx. 47 kg
(Manipulator weight: 45 kg (100 lb.))
PS5
: Approx. 51 kg
(Manipulator weight: 49 kg (109 lb.))
PS3L : Approx. 53 kg
(Manipulator weight: 51 kg (113 lb.))
PS3LP : Approx. 53 kg
(Manipulator weight: 51 kg (113 lb.))
Reference:
Pulse values at Manipulator transport (PS series) : 0, 2621440,
−
3140167, 0,
−
1847207, 0
E2C, E2S, E2L
To carry the Manipulator, have two or more people to work on it and secure the
Manipulator to the delivery equipment or hold the areas indicated in gray in the
figure (bottom of Arm #1 / main cable elbow fitting / bottom of the base) by hand.
When holding the bottom of the base by hand, be very careful not to get hands or
fingers caught.
Table Top
E2C : Approx. 14 kg (31 lb.)
E2S : Approx. 22 kg (49 lb.)
E2C : Approx. 16 kg (36 lb.)
E2L : Approx. 33 kg (73 lb.)
E2S : Approx. 22 kg (49 lb.)
Multiple Mountings
(Figure of E2S)
(Figure of E2S)