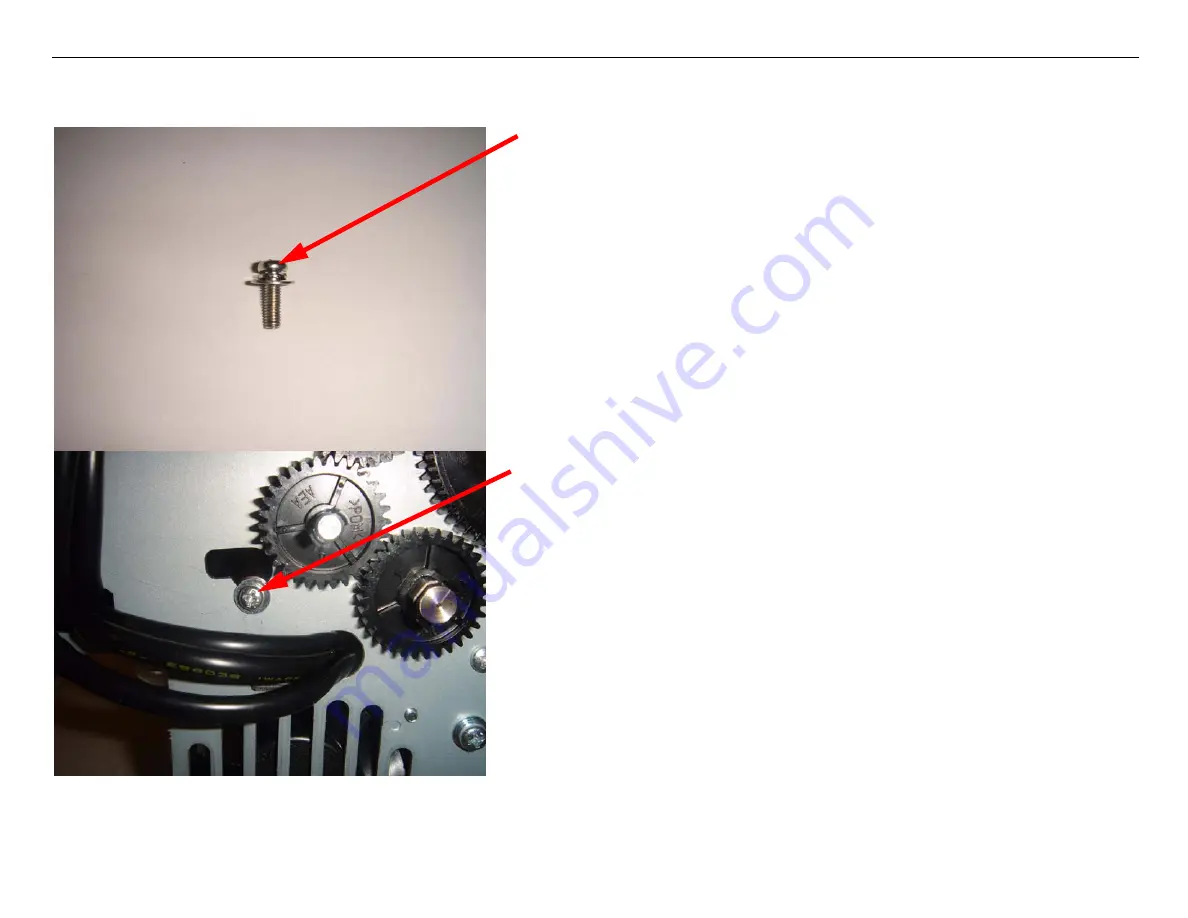
Epson DFX-9000 Field Repair Guide
3/29/07
Printer Component,
Software Item,
LCD Display,
Printer Button
Page 97.
13. Place the
SUB SHAFT
into the recessed holes in the left and right side of the frame, and then reinstall the two
C.P. (S-P1) 3 x 10 screws into its left and right side.
C.P. (S-P1) 3 x 10
Left side of SUB SHAFT with C.P. (S-P1) 3 x 10 screw