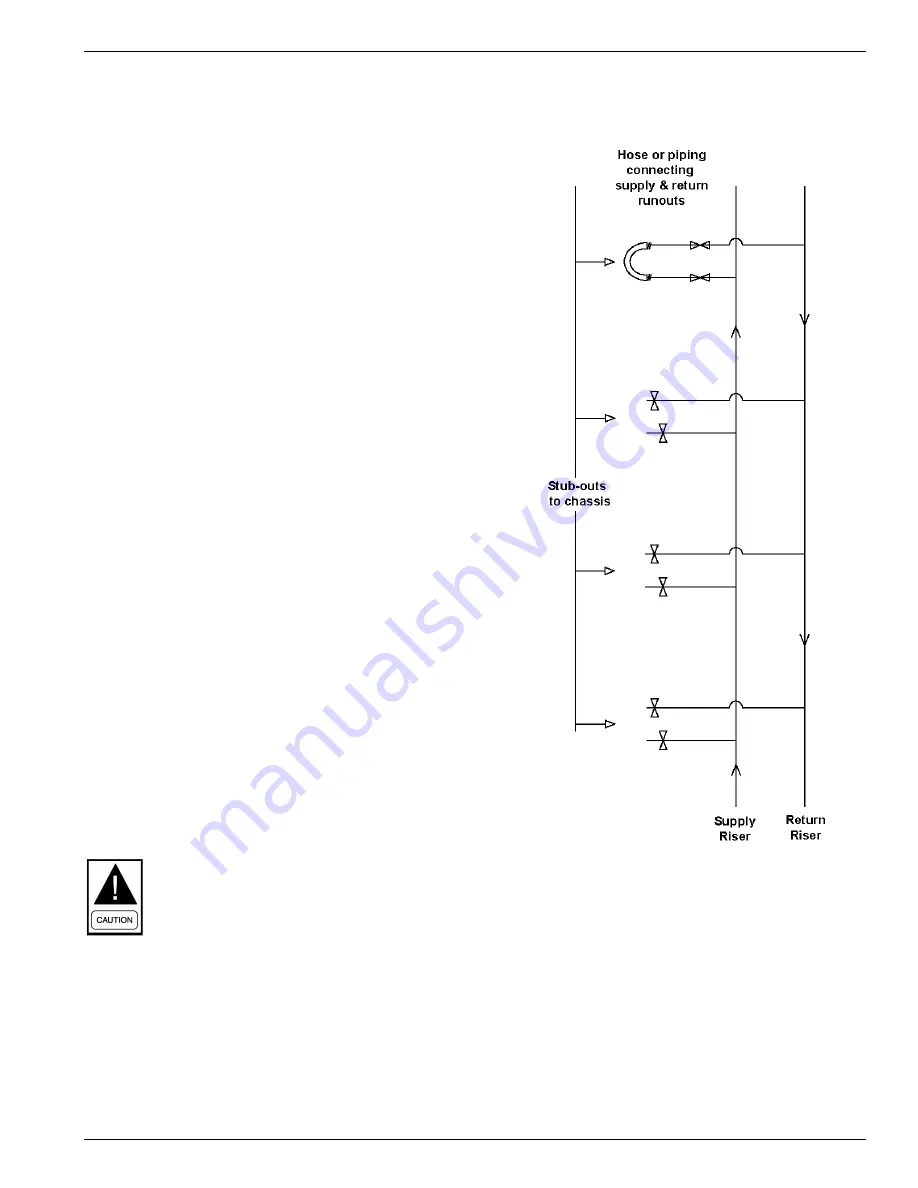
FORM ET145.18-IOM1 (115)
ENVIRO-TEC
33
14. SYSTEM FLUSHING AND CLEANING
After the piping system is complete, and prior to connection of
the refrigeration chassis, the risers should be flushed and
cleaned to ensure proper start-up and continued efficient
operation of the system.
1.
Ensure that the supply and return riser shut-off valves are
closed at each unit.
2.
Using flexible hoses or piping, connect the supply and
return stub-outs in the unit located at the end of the riser
run(s). If the building has more than 10 floors, connect the
supply and return stub-outs in the last two units to divide
the water flow and reduce pressure drop at the pump.
(See Figure below)
3.
Open the shut-off valves in the units that have had the
supply and return risers inter-connected.
4.
The water circulation system should be filled with clean
water using the make-up water supply. The air vents
should be open during initial filling (Do not allow the
system to overflow).
5.
With the air vents closed, start the circulating pump and
then crack each air vent to ensure that all air is bled from
the system.
(Make-up water must be available in
sufficient volume to replace the volume occupied by the
air that is bled off.)
6.
When all air is vented, and the water is circulating under
pressure, the entire system should be checked for leaks.
Make any repairs as required.
7.
Set the loop temperature controls to raise the
temperature to approximately 85
o
F. Perform a visual
check for any leaks that may have occurred due to the
increased heat. Repair as required.
8.
Open the drain at the lowest point in the system (make-up
water flow rate must be equal to rate of drain bleed).
Continue to bleed system until water leaving the drain is
clear, but not less than 2 hours.
9.
Completely drain the piping system.
After the initial Flushing, the system should be chemically
cleaned. The procedure for re-filling the system, and
circulating the cleaning solution, is the repeat of the above
flushing method.
The services of a professional water treatment company are
recommended with regards to the type of solution to be used,
and the duration of the cleaning application.
Once the cleaning process is complete, shut off the circulating
pump and completely drain the system. Refill the system with
clean water in preparation for connection of the refrigeration
chassis, and system start-up.
It is strongly recommended a professional water
treatment company is used to perform on-going
maintenance of water loop including chemical
analysis, and if necessary flushing. The water loop
testing
should
be performed at intervals
recommended by the professional water treatment
consultant. It is up to the customer to carry out
adequate water loop maintenance over the lifespan
of the units otherwise damage to the units may
occur.
Содержание VB09-36
Страница 6: ...FORM ET145 18 IOM1 115 ENVIRO TEC 6 FIGURE 1 Cabinet Chassis Model Nomenclature ...
Страница 7: ...FORM ET145 18 IOM1 115 ENVIRO TEC 7 ...
Страница 19: ...FORM ET145 18 IOM1 115 ENVIRO TEC 19 FIGURE 9A Optional Return Air Panel with ADA Mounted Thermostat ...
Страница 21: ...FORM ET145 18 IOM1 115 ENVIRO TEC 21 FIGURE 11 Unit Mounted Supply Grille Installation Dimensions ...
Страница 34: ...FORM ET145 18 IOM1 115 ENVIRO TEC 34 APPENDIX PSC MOTOR WIRING DIAGRAM ...
Страница 35: ...FORM ET145 18 IOM1 115 ENVIRO TEC 35 ECM WIRING DIAGRAM ...
Страница 36: ...FORM ET145 18 IOM1 115 ENVIRO TEC 36 CONTINUOUS FAN WITH ECM WIRING DIAGRAM ...
Страница 37: ...FORM ET145 18 IOM1 115 ENVIRO TEC 37 MOTORIZED DAMPER ECM WIRING DIAGRAM ...
Страница 39: ...FORM ET145 18 IOM1 115 ENVIRO TEC 39 NOTES ...