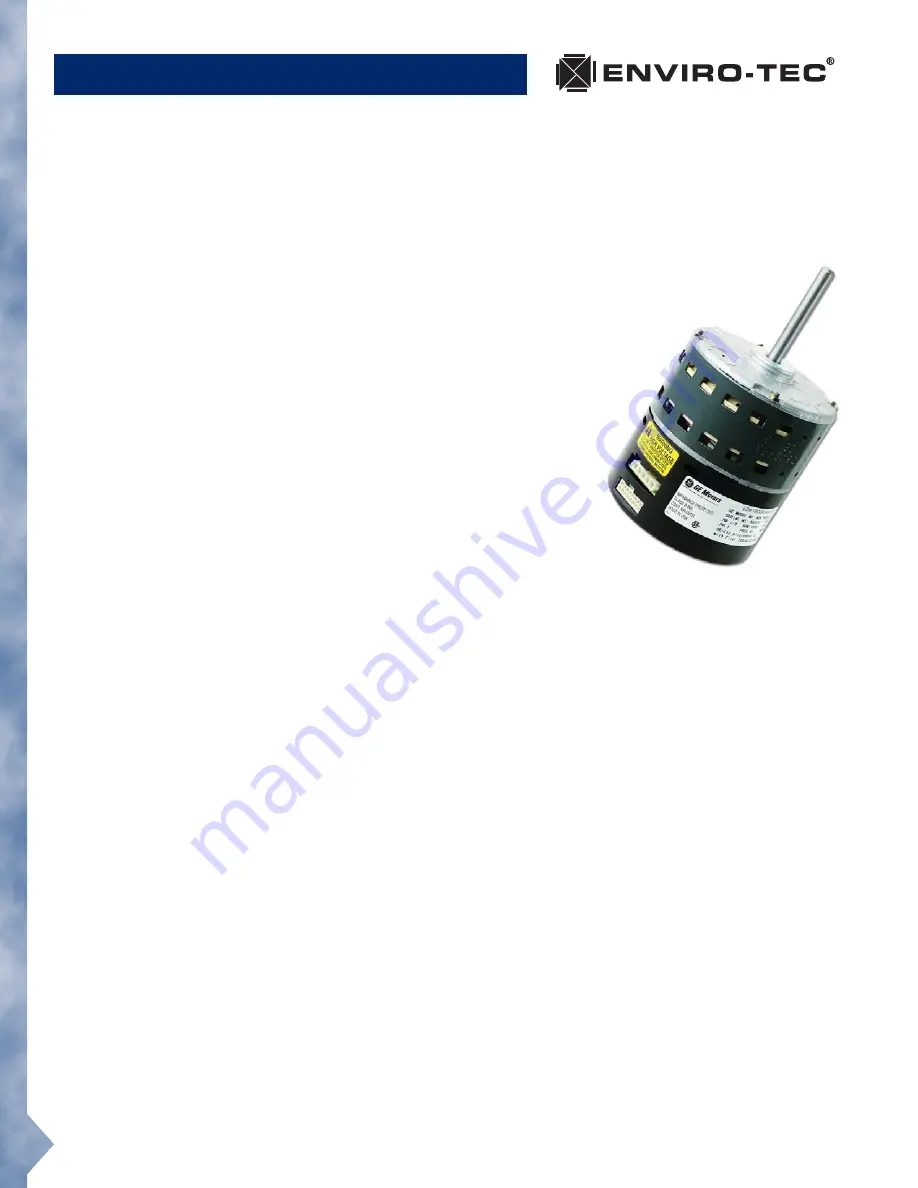
CFR •
ECM™ F
AN
M
OTOR
O
PTION
18
CFR Catalog • ©
December, 2005 Environmental Technologies, Inc.
ENVIRO-TEC
®
offers an alternative to the PSC motor
that significantly increases the operating efficiency of
fan terminal units.
This motor is frequently referred to
as an ECM™ (electronically commutated motor). It is a
brushless DC (BLDC) motor utilizing a permanent mag-
net rotor. The motor has been in production for years
and is commonly used in residential HVAC units. Fan speed
control is accomplished through a microprocessor based
variable speed controller (inverter) integral to the motor.
The motor provides
peak efficiency ratings between 70
& 80%
for most applications.
ECM™ FEATURES AND BENEFITS
Ultra-High Motor & Controller Energy Efficiency
DC motors are significantly more efficient than AC
motors. At full load the ECM™ is typically 20% more effi-
cient than a standard induction motor. Due to acoustical
considerations, the fan motor on a fan powered termi-
nal typically operates considerably less than full load. At
this condition the overall motor / controller (SCR) efficiency
can be cut in half. Due to the permanent magnet, DC
design, the ECM™ maintains a high efficiency at low speeds.
Most fan powered unit selections will have an overall effi-
ciency greater than 75%. Furthermore, the motor heat
gain is greatly reduced providing additional energy sav-
ings by reducing the cold primary air requirement.
Pressure Independent Fan Volume
The integral microprocessor based controller includes a
feature that provides sensorless (no external feedback) con-
stant airflow operation by automatically adjusting the speed
and torque in response to system pressure changes. This
breakthrough will no doubt have far reaching
benefits and endless applications. For starters, the fan
volume supplied to the space will not significantly change
as a filter becomes loaded. This provides new opportu-
nities for medical applications where space pressurization
and HEPA filters are applied. The air balance process will
become simpler and more accurate since the fan volume
will not need to be re-adjusted after the diffuser balance
is accomplished.
Factory Calibrated Fan Volume
Due to the pressure independent feature, the fan
capacity can now be calibrated at the factory. Within the
published external pressure limits, the fan motor will
automatically adjust to account for the varying static
pressure requirements associated with different
downstream duct configurations. This feature should not
preclude the final field air balance verification process
during the commissioning stage of a project. An
electronic (PWM) speed control device is provided to allow
field changes of the fan capacity as the need arises. Fan
volume can be field calibrated in two fashions. First, a
potentiometer is provided allowing manual adjustment
using an instrument type screwdriver. In addition, the
fan volume can be calibrated through the BMS using an
analog output (2 to 10VDC typical) to the speed
controller. A fan volume verses DC volts calibration chart
is provided.
Designer / Owner Flexibility
The ECM™ incorporates ball bearings in lieu of sleeve
bearings typically utilized with an induction
motor. Unlike a sleeve bearing
motor, the ECM™ does not have
a minimum RPM requirement for
bearing lubrication. This allows
it to operate over a much
wider speed range. One
motor can handle the
capacity range previ-
ously handled by two
motors, allowing sim-
plification of the
product line and con-
siderable flexibility to the
designer. The owner also
benefits since equipment
changes are much less likely with tenant requirement
changes. A reduced spare parts inventory is another plus.
Custom Applications —
Programmable Fan Operation
Boundless control opportunities arise due to the con-
trollability of a DC motor combined with an integral
microprocessor. Various input signals can direct the motor
to behave in an application specific mode. For instance,
multiple discrete fan capacities can be achieved. In
addition, the fan speed can be varied in response to the
space temperature load. The fan can also be pro-
grammed for a soft start. The motor starts at a very low
speed and slowly ramps up to the required speed. This
is especially beneficial for parallel flow fan terminals since
the perceived change in space sound levels is lessened.
Extended Motor Life
The high motor efficiency provides a significantly reduced
operating temperature compared to an induction motor.
The lower temperature increases the longevity of all
electrical components and therefore the life of the motor.
The ball bearings do not require lubrication and do not
adversely impact the motor life. Most fan powered
applications will provide a motor life between 60,000 and
100,000 hours. A motor life of twenty five years will not
be uncommon for a series flow fan terminal and a longer
life can be expected for a parallel flow unit.
The Energy Efficient Solution
Содержание CFR
Страница 1: ...December 2005 Part No PX 00 0005 ...