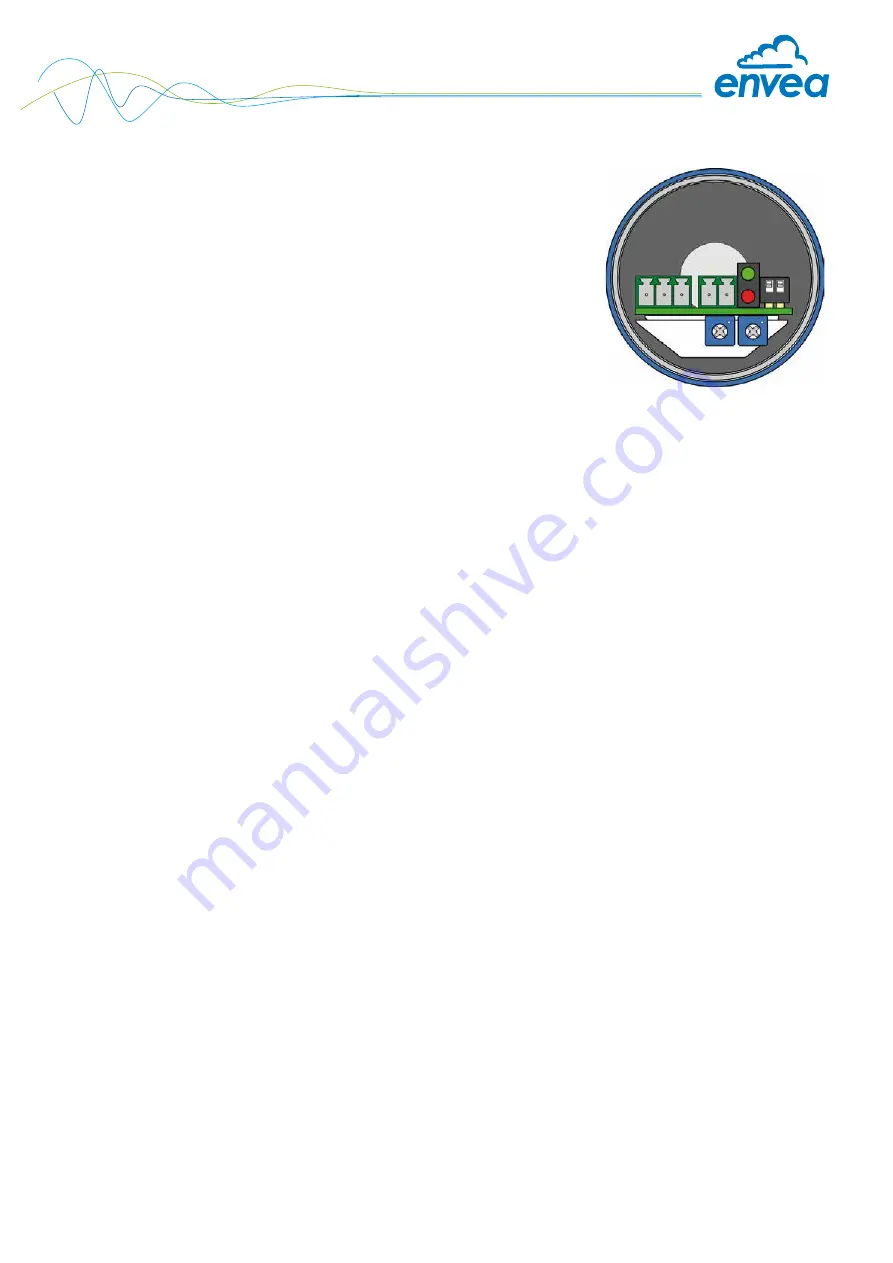
7
6. Start-up procedure
Before the ProGap 2.0 measuring point can be put into operation, the
electrical connection should be checked. After the power supply has been
switched on, a warm-up time of 5 minutes must be observed. All operating
elements required for commissioning are located in the receiver.
Electrical connection
1
Uin +24 V
2
Uin 0 V
3
Relay contact NO
4
Relay contact COM
5
Relay contact NC
Status LED
LED 1
red
The flashing frequency of the red LED provides information about the signal strength between
transmitter and receiver:
• Fast flashing
= high signal strength
• Slow flashing
= low signal strength
• LED off
= no received signal
LED 2
green
The green LED provides information about the switching state of the relay contact
• LED on
= relay is energized
• LED off
= relay is dropped
Dip-switch
S1
Changing the state of the DIP-switch S1 will invert the behaviour of relay output
S2
Switching between near and far range is accomplished by operating the DIP-switch S2.
If the state is ON (down-position), the signal will damped and the measurement of smaller
distances and low density materials could be possible.
Potentiometer
P1
Adjustment of the threshold based on the sensitivity
Left stop
= lowest sensitive
Right stop
= highest sensitivity
P2
Setting for time delay on the relay contact
Left stop
= 0.25 s
Right stop
= 5 s
Adjustment of the signal threshold with potentiometer P1
With the potentiometer P1 the signal threshold can be adjusted, so that the relay should switch. The micro-
wave barrier is adjusted in such a way that clear distinctions between interrupted or damped resp. not-
interrupted microwave beam are made.
Proceeding:
With not-interrupted beam and flashing red LED 1 turn P1 clockwise as long as the relay switches and
at the same time the LED 2 shines green. Now interrupt the beam path (put the material to be detected
between the transmitter and the receiver) and turn P1 only so far against the clockwise until the green LED
2 disappear. If the green LED 2 still lights, even with a complete left turn of P1, via S2 can be switched in
the near range. This switching will attenuate the signal on the sensor side and material detection should be
possible. To ensure that the measuring point works properly, this process should be repeated.
Fig. 5: Control elements receiver