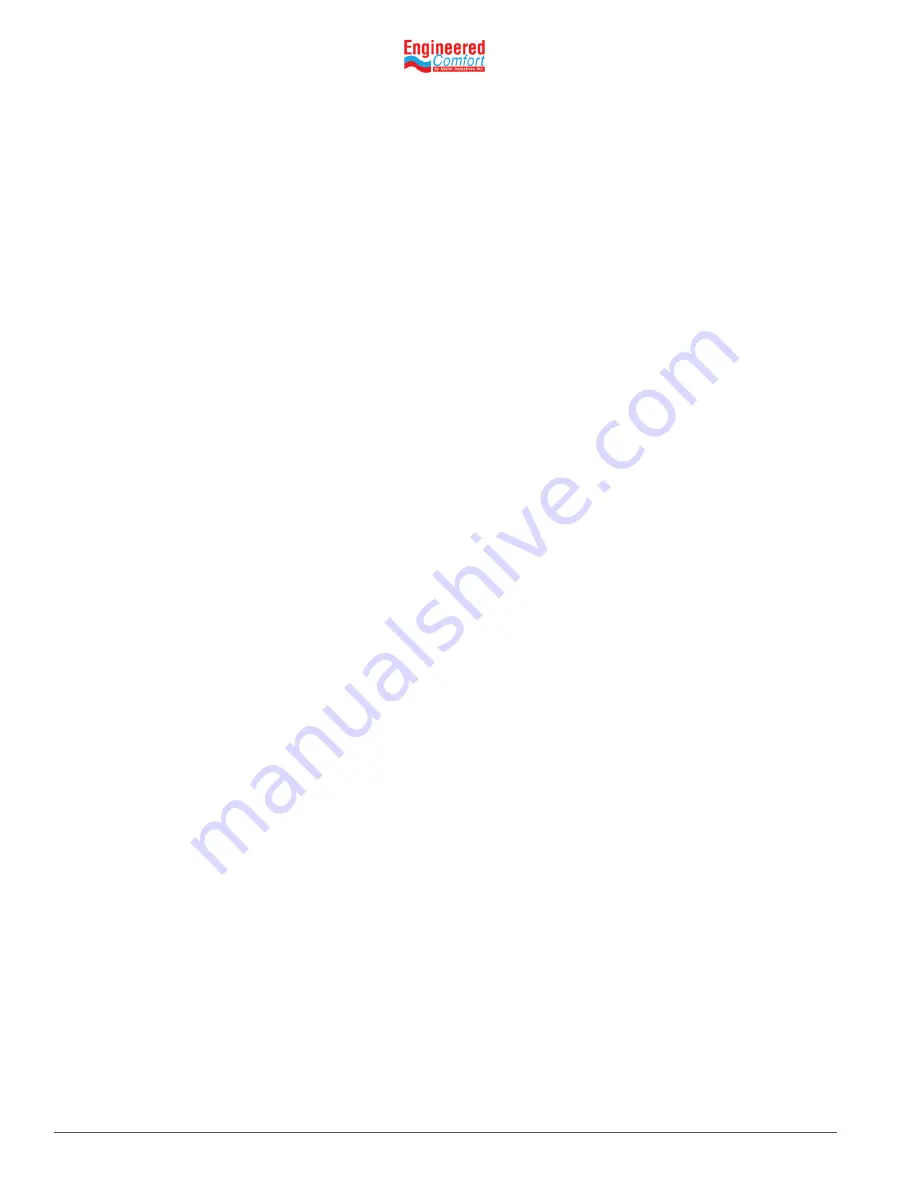
Installation and Operation Manual
●
Fan Coil Controller – EZstat
EC-EZstat
Date: 9-2014
Supersedes: NEW
Engineered Comfort reserves the right to change any information concerning product or specification without notice or obligation.
Page 28 of 36
7.3 Automatic cooling and heating changeover
The EZstat can be set to automatically change between the heating and cooling modes.
•
If the space temperature rises above the active cooling setpoint, the mode is set to cooling.
•
If the space temperature falls below the heating setpoint, the mode is set to heating.
7.4 Scheduling occupancy
The schedule in the controller is a standard BACnet schedule object. It can be changed from the display by a technician
with Password 2 or a BACnet operator workstation.
The internal occupancy schedule changes the EZstat between the occupied (ACTIVE) and unoccupied (INACTIVE) states.
7.5 Display blanking and backlight
The EZstat display and backlight can be set to take any of the following actions one minute after the last button is pushed.
•
Display an analog clock instead of the temperature display.
•
Dim the display to a preset level.
•
Remain unchanged.
When the display is dimmed or the clock is visible, the display returns to normal when any button is pushed.
7.6 Temperature sensing inputs
The EZstat includes inputs for sensing space, discharge air, and fan coil unit supply water.
Space temperature sensing
All models of EZstat include an internal temperature sensor for measuring space temperature. For remote temperature
sensing, an external, 10,000 ohm, Type II thermistor sensor or Nailor Part# H1‑1989 can be connected to terminals RS. If
the EZstat detects that a remote sensor is connected, the internal sensor is not used for determining space temperature.
Water temperature sensor
The Water Temperature Sensor input (WST) is a required sensor for two‑pipe fan coil units with both heating and
cooling applications. The EZstat is configured for a Type III thermistor sensor or Nailor Part# H1‑1764B to monitor water
temperature.
The water temperature can be monitored as an analog input and is also stored in an analog value object.
Discharge air temperature sensor
The Discharge Air Temperature (DAT) setup is a required for modulating valve applications. The EZstat is configured for a
Type III thermistor sensor or Nailor Part# H1‑0246 for DAT applications. Discharge air temperature can be monitored as an
analog input and is also stored in an analog value object.
The Loop 3 (CL_DAT_Loop) and Loop 4 (HT_DAT_Loop) modulate to the DAT set‑points. The valves are controlled off
these loops, while the DAT sensor is constantly monitoring the discharge air temperature.
7.7 PID control loops
A PID control loop calculates an error value from the difference between the measured room temperature and the active
setpoint. The error value is expressed as a percentage and is typically used in a BAS controller to control the state of
an output. When the difference between the setpoint and room temperature is large, the error is large. As the system
reduces the difference between the setpoint and space temperature, the error becomes smaller. In a simple example, if
the output of the PID loop that is controlling a modulating valve is 50% the valve would be opened half way; if the output
of the loop is 100% the valve position is fully open.
The EZstat uses the heating and cooling PID loops which are implemented in all sequences.
The PID loops in the EZstat are standard BACnet objects.
7.8 Valve operation for fan coils
Hot and chilled water valves are used for heating and cooling in the fan coil unit versions of the EZstat. The fan coil two‑
pipe programming includes also a method to determine supply water temperature.
Modulating valves
On a call for cooling or heating, a modulating valve will modulate from 0 to 100% over the first half (0‑50%) of the PID
loop output controlling the valve. The EZstat supports both normal and reverse action valves which can be set from the
user interface.