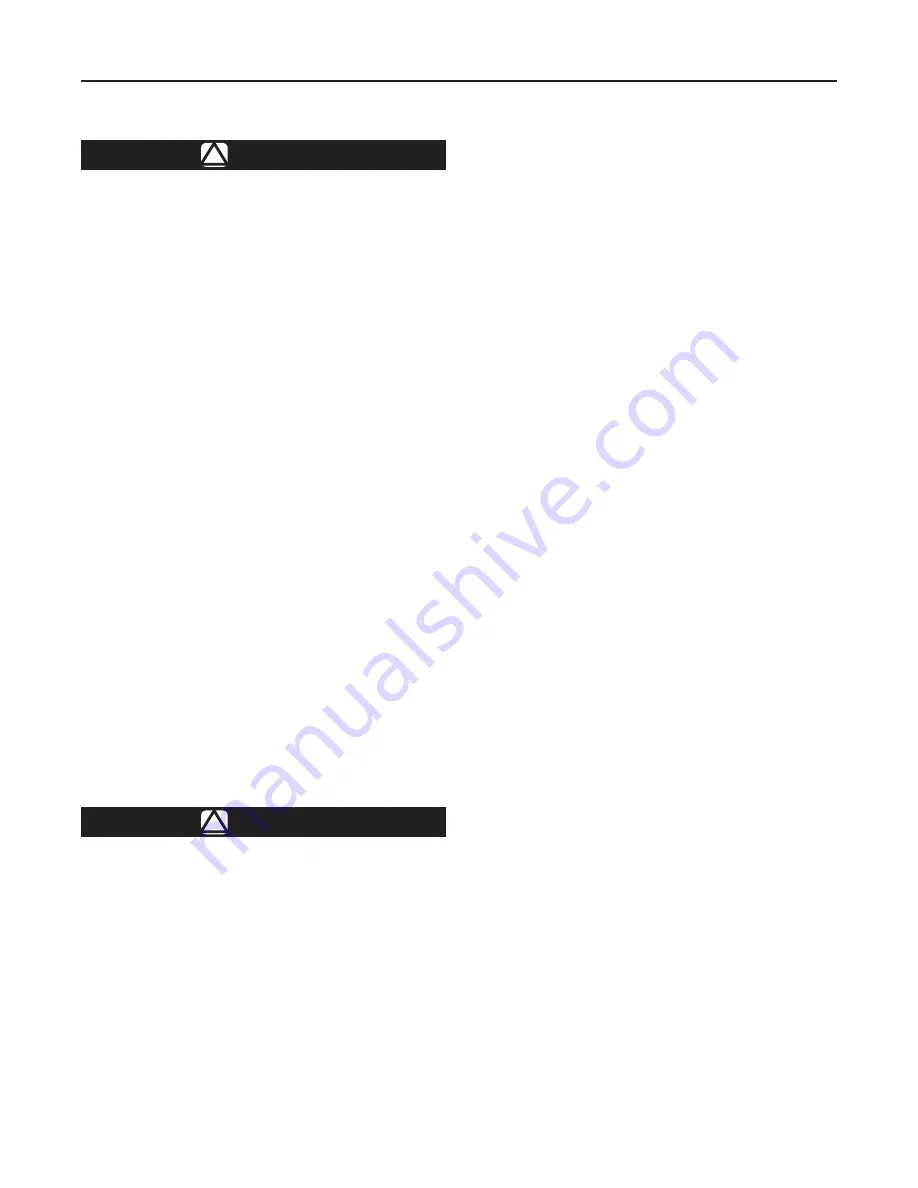
!
!
5
T205VB Series
Installation
Personal injury, property damage,
equipment damage or leakage due to
escaping gas or bursting of pressure-
containing parts may result if this
equipment is overpressured or is
installed where service conditions could
exceed the limits given in Specifications
section or where conditions exceed any
ratings of the adjacent piping or piping
connections. To avoid such injury or
damage, provide pressure-relieving or
pressure-limiting devices (as required
by the appropriate code, regulation or
standard) to prevent service conditions
from exceeding those limits.
Additionally, physical damage to this
equipment could cause personal injury
or property damage due to escaping
gas. To avoid such injury or damage,
install the equipment in a safe and well
ventilated location.
Note
If this equipment is shipped mounted on
another unit, install that unit according
to the appropriate instruction manual.
1. Only personnel qualified through training and
experience shall install, operate and maintain this
equipment. For T205VB Series equipment that
is shipped separately, make sure that there is no
damage to or foreign material in it. Also ensure that
all tubing and piping are clean and unobstructed.
This equipment may vent some gas
to the atmosphere. In hazardous or
flammable gas service, vented gas may
accumulate and cause personal injury,
death or property damage due to fire or
explosion. Vent equipment in hazardous
gas service to a remote, safe location
away from air intakes or any hazardous
area. The vent line or stack opening
must be protected against condensation
or clogging.
WARNING
WARNING
2. This equipment may be installed in any position
as long as the flow through the body is in the
direction indicated by the arrow on the body. If
continuous operation is required during inspection
or maintenance, install a three-way bypass valve
around the equipment.
3. To keep the spring case vent (key 26, Figure 3
or 4) from being plugged or the spring case from
collecting moisture, corrosive chemicals or other
foreign material, point the vent down or otherwise
protect it. The diaphragm casing (key 4) may be
rotated in order to obtain desired positioning.
4. To remotely vent the vacuum breaker, remove the
vent (key 26, Figure 3 or 4) and install obstruction-free
tubing or piping into the 1/4 NPT vent tapping. Provide
protection on a remote vent by installing a screened
vent cap into the remote end of the vent pipe.
5. The Type T205VBM requires a control line. Be
sure to install the control line before putting the
vacuum breaker into operation. Make the control
line as short and straight as possible and do not
install it in a location where flow may be turbulent.
Restrictions in the control line can prevent proper
pressure registration. When using a hand valve, it
should be a full flow valve, such as a full port ball
valve. Install the control line sloping downward
toward the tank to prevent condensation buildup
and avoid low points (or traps) that could catch
liquid. The sensing line must enter the tank
above the liquid level at a point that senses the
vapor space pressure and is free from turbulence
associated with tank nozzles or vents. The control
line pipe should be at least 1/2 in. / 13 mm in
diameter and increase 1 pipe size for every
10 ft / 3.05 m of control line, with setpoint less than
5 in. w.c. / 12 mbar.
6. An upstream shutoff valve is recommended to
simplify maintenance to the vacuum breaker. It is
advisable to install a pressure gauge between the
upstream shutoff valve and the breaker.
Startup, Adjustment and Shutdown
Note
The Specifications section provides
the maximum pressure capabilities for
each vacuum breaker construction.
Use pressure gauges to monitor inlet
pressure and outlet pressure during
startup and adjustment procedures.