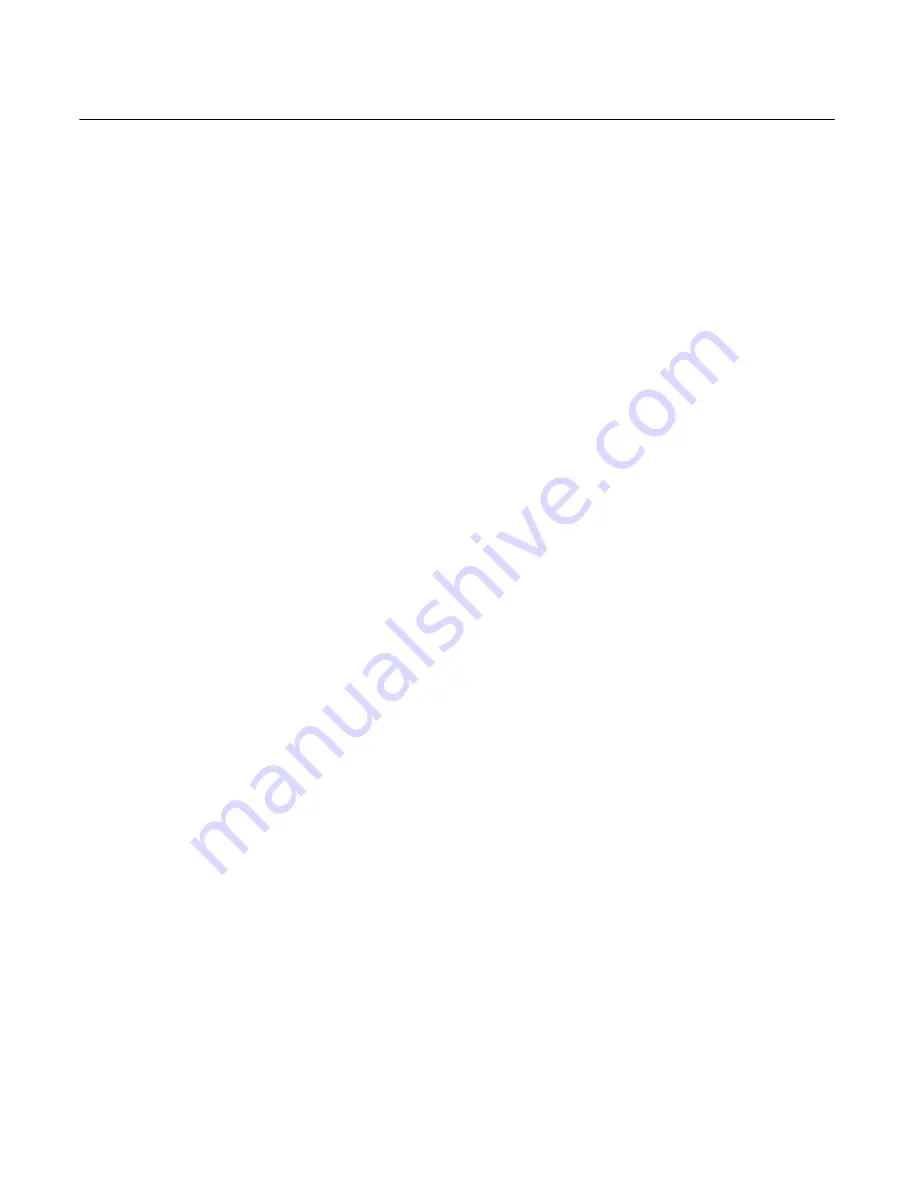
2502 Series Controllers
Instruction Manual
Form 1446
November 2006
11
than 0.2 bar (3 psig) for the 0.2 to 1.0 bar (3 to 15
psig) range or 0.4 bar (6 psig) for the 0.4 to 2.0 bar
(6 to 30 psig) range. For reverse-acting controllers,
the output pressure should be greater than 1.0 bar
(15 psig) and less than 1.4 bar (20 psig) for the 0.2
to 1.0 bar (3 to 15 psig) range or greater than 30
psig (2.0 bar) and less than 3.4 bar (35 psig) for
the 0.4 to 2.0 bar (6 to 30 psig) range. If these
conditions are not met recalibration may desired. On
a controller with indicator assembly, the pointer
should be over the low point on the indicator plate;
slight adjustment might be necessary by loosening
the hex nut (key 40, figure 14), shifting the pointer,
and retightening the nut.
4. Set the raise level control as desired. Determine
the dial setting by moving the nameplate slide until
the specific gravity on scale B is opposite the
displacer volume on scale A. Choose the percentage
of displacer length, as measured from the displacer
bottom, that you desire the liquid or interface level to
cover. Locate this percentage on scale D, and read
up from this percentage to find the RAISE LEVEL
dial setting on scale C. For example, with a liquid
level application, a specific gravity of one (water
service), and a 1.5 L (90-cubic-inch) displacer, move
the slide so that 1.0 on scale B is over 90 on scale
A. If it is desired to have water level cover 50 per
cent of the displacer length at the control point, read
up from 50 on scale D to find a 4.5 dial setting on
scale C.
5. Relocate the process variable to the control point
determined in step 4. See if output pressure
accurately reflects the process variable. If not, see if
another setting on the RAISE LEVEL dial brings the
output pressure into agreement with the process.
For example, with water level at 50 percent of the
height of the displacer, the output of a 0.2 to 1.0 bar
(3 to15 psig) unit should be approximately 50
percent of the way between 0.2 and 1.0 bar (3
and 15 psig) or 0.6 bar (9 psig). If the new setting is
more than one graduation away from the setting
determined in step 4, the unit would appear to be out
of calibration and recalibration may be desirable.
See the Calibration Procedure on page 14.
On a controller with level indicator, the pointer
should reflect the magnitude of the process variable;
for instance, with liquid or interface level covering 50
percent of the displacer, the pointer should be in the
middle of the high-low scale. Slight plate adjustment
might be necessary as described at the end of
6. If all prestartup checks are satisfactory proceed
to the Startup section.
Adjustments
Controller adjustments are provided in this section.
Refer to figure 9 for adjustment locations.
Level Set Adjustment
To perform the level adjustment, open the controller
cover, loosen the knurled adjustment screw (see
figure 9), and rotate the adjustment lever around the
RAISE LEVEL dial. To raise the fluid or interface
level, or increase density, rotate this knob in the
direction of the arrows. To lower the level or
decrease density, rotate the knob in the opposite
direction. This procedure is the same for both direct
and reverse action controllers. Tighten the knurled
screw.
Note
The RAISE LEVEL dial does not reflect
actual fluid level in the tank or fluid
level position on the displacer.
Proportional Band Adjustment
Proportional band adjustment is made to change the
amount of displacement force change required to
obtain full output pressure change, by determining
the percentage of pressure fed back to the
proportional bellows. The adjustment is performed
by opening the controller cover and turning the
percent proportional band knob (just below the
RAISE LEVEL dial).
Reset Adjustment
To adjust reset action (figure 9) turn the knob
clockwise to decrease reset time (the minutes per
repeat). Turn the knob counterclockwise to increase
the minutes per repeat. Increasing the minutes per
repeat provides a slower reset action.
The reset rate adjustment dial is calibrated in
minutes per repeat. By definition, this is the time in
minutes required for the reset action to produce a
correction which is equal to the correction produced
by proportional control action. This is, in effect, the
time in minutes required for the controller to increase
(or decrease) its output pressure by an amount
equal to a proportional increase (or decrease)
caused by a change in control conditions.