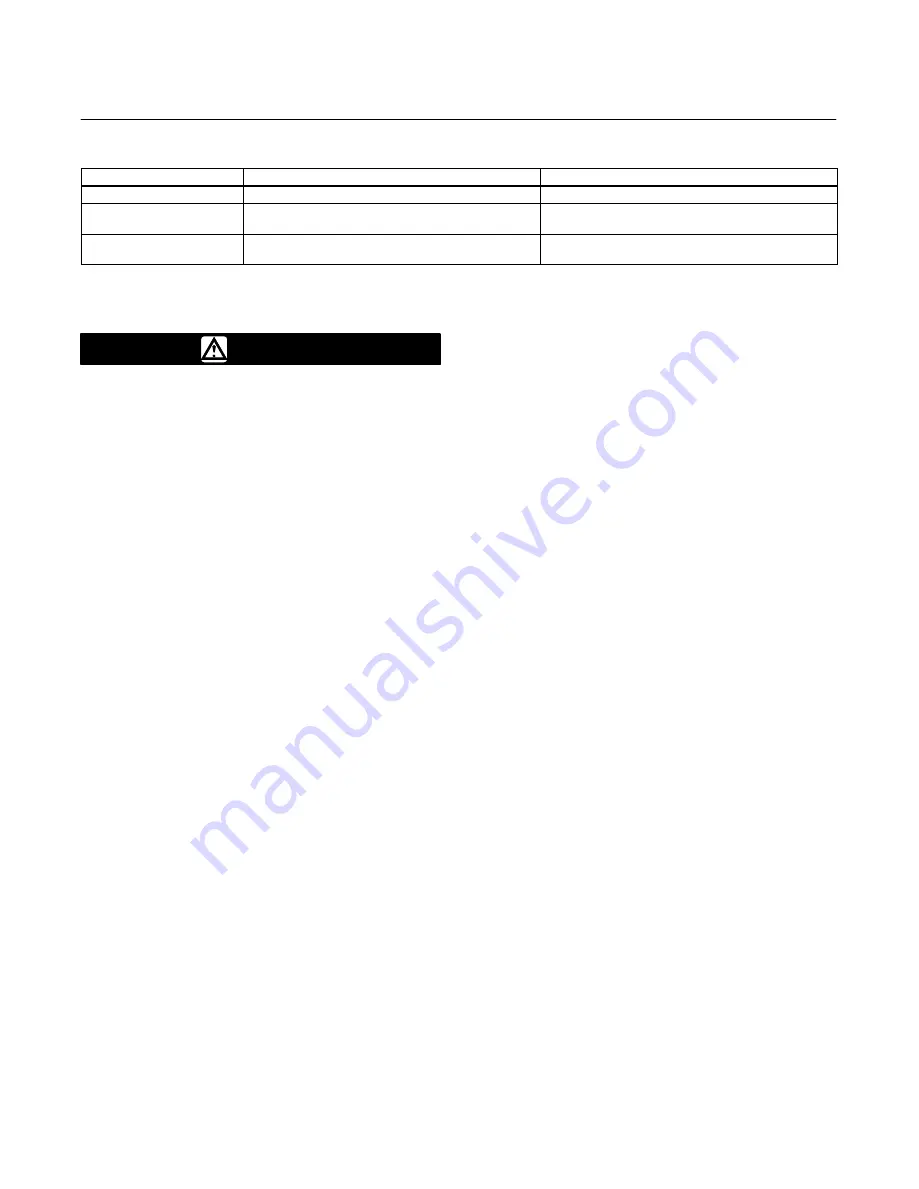
2502 Series Controllers
Instruction Manual
Form 1446
November 2006
14
Table 2. Minimum and Maximum Limits for Setting Process Variables
Application
Minimum Limit
Maximum Limit
Liquid level
Displacer must be completely out of liquid
Displacer must be completely submerged in liquid
Interface
Displacer must be completely submerged in the upper
of two process liquids
Displacer must be completely submerged in the lower
of two process liquids
Density
Displacer must be completely submerged in liquid having
highest specific gravity expected
Displacer must be completely submerged in liquid
having the lowest specific gravity expected
Calibration Procedure
WARNING
The following calibration procedure
requires taking the controller out of
service. To avoid personal injury and
property damage caused by an
uncontrolled process, provide some
temporary means of control for the
process before taking the controller
out of service.
Figure 9 shows adjustment locations for the
following steps, except as otherwise indicated. When
calibrating, open loop conditions must exist. One
way to obtain an open loop is to place the final
control element into manual control or bypass it. If
there is no provision for manual control, shut down
the process. It is recommended that a test pressure
gauge be installed in the controller output line for
subsequent calibration steps.
Several steps in these calibration procedures require
setting the process variable at its minimum and
maximum limits according to table 2. Reverse-acting
controllers produce the opposite response.
1. Connect a supply pressure source to the
controller and provide a supply pressure suitable for
the sensing element range: 1.4 bar (20 psig) for
a 0.2 to 1.0 bar (3 to 15 psig) output pressure range
or 2.4 bar (35 psig) for a 0.4 to 2.0 bar (6 to 30 psig)
output pressure range.
2. Rotate the reset knob to 0.01 minutes per repeat.
3. Rotate the proportional band knob to zero.
4. Set the liquid at the minimum limit (dry displacer).
5. Turn the RAISE LEVEL knob to zero.
6. Adjust the nozzle until output pressure is
between 0 and 0.2 bar for a 0.2 to 1.0 bar signal
range (0 and 3 psig for a 3 to 15 psig signal range)
or 0 and 0.4 bar for a 0.4 to 2.0 bar signal range (0
and 6 psig for a 6 to 30 psig signal range).
7. Set the liquid at the maximum limit (covered
displacer).
8. Turn the RAISE LEVEL knob until the output
pressure is 1.0 bar for a 0.2 to 1.0 bar signal range
(15 psig for a 3 to 15 psig signal range) or 2.0 bar for
a 0.4 to 2.0 bar signal range (30 psig for a 6 to 30 psig
signal range).
9. The controller is within its calibration accuracy if
the RAISE LEVEL knob is between the 9.0 and 10.0
positions.
10. If the controller is out of calibration, adjust the
calibration adjuster as follows:
Note
Loosen the two calibration adjuster
screws (key 45, figure 14), and slide
the calibration adjuster (key 100, figure
a. If output is
below
1.0 bar for a 0.2 to 1.0 bar
signal range (15 psig for a 3 to 15 psig signal
range) or 2.0 bar for a 0.4 to 2.0 bar signal range
(30 psig for a 6 to 30 psig signal range), move the
adjustor a small distance away from the pivot to
increase
span. Then repeat steps 4 through 9.
b. If output is
above
1.0 bar for a 0.2 to 1.0 bar
signal range (15 psig for a 3 to 15 psig signal
range) or 2.0 bar for a 0.4 to 2.0 bar signal range
(30 psig for a 6 to 30 psig signal range), move the
adjustor a small distance toward the pivot to
decrease
span. Then repeat steps 4 through 9.
Note
If the controller cannot be calibrated,
look for other problems as described
in the Troubleshooting section, such
as a nonperpendicular flapper-nozzle
condition, leaky connections, or a
binding displacer rod. If none of these
troubles is apparent, the displacer or
torque tube may be sized for a different
set of service conditions. Ensure that
the displacer is sized correctly for the
application.